Evaluating Material Properties in Manufacturing to Enhance Efficiency
To produce oil seals and O-rings, various raw materials are blended to achieve the desired performance and physical properties. While raw materials come with data provided by manufacturers and finished products undergo a thorough evaluation, there is less readily available data on intermediate materials, those still in the processing stage before becoming final products. However, analyzing their properties is crucial for product development and manufacturing processes, as they play a key role in industrial production. For nearly 20 years, NOK has independently measured the processing characteristics of these intermediate materials. By expanding the scope of its evaluations, the company aims to improve production efficiency and strengthen its competitive edge.
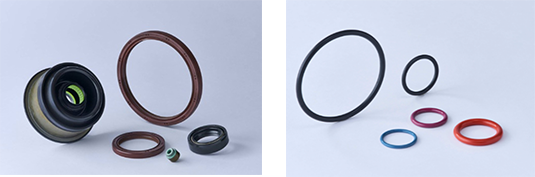
Refining processing data to improve manufacturing efficiency
For manufacturers like NOK, minimizing defects and shortening development time are key to better manufacturing. Engineers are constantly exploring new methods to achieve these goals. At NOK, the Manufacturing Research Department is taking a new approach by developing evaluation methods that assess processing characteristics to optimize manufacturing efficiency.
Shunji Iwasaki, who leads the Processing Engineering Section within NOK Group R&D's Manufacturing Research Department, explains that NOK began evaluating the release resistance of rubber materials nearly 20 years ago when the department was still known as the Technology Development Department. Release resistance refers to how easily a rubber material separates from its mold, a critical factor in manufacturing. Even if a rubber compound meets all performance requirements, poor mold release can cause major production issues, making large-scale manufacturing difficult. By assessing and quantifying release resistance, NOK optimized its selection of rubber materials, mold release agents (chemicals applied to molds to aid separation), and coating methods, ensuring smoother production before moving into mass manufacturing.
In recent years, however, the complexity of product shapes has increased. More intricate designs raise the risk of materials tearing unevenly when removed from the mold. Additionally, a rough surface — where unintended patterns or irregularities appear — can prevent the product from achieving its intended performance. "We are developing new evaluation methods to assess both the risk of tearing due to mold release and the risk of rough surface defects," explains Ryo Maruyama of the Manufacturing Research Department's Processing Engineering Section.
Exploring new evaluation methods and effective use of data
Oil seals must achieve the delicate balance of maximizing sealing performance while minimizing friction resistance. This requires intricate and precise surface and lip designs, which, in turn, increase the risk of tearing when removed from the mold, potentially compromising sealing effectiveness. Recognizing the importance of evaluating the physical properties of intermediate materials, NOK is developing more advanced and precise evaluation methods to address this challenge.
Please enlarge the screen to view
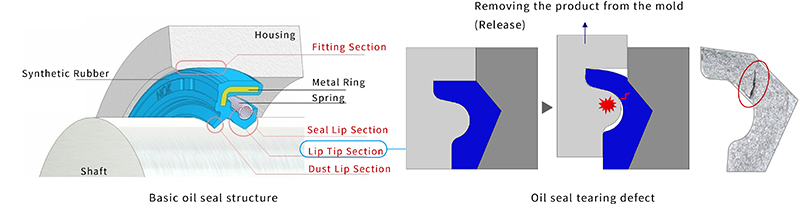
Currently, one method for assessing the risk of tearing is a tensile test using test pieces to measure how much the rubber can stretch and withstand deformation. However, this method requires reheating the cooled test pieces to match the mold temperature before testing. Since this does not fully replicate the conditions under which tearing occurs, discrepancies can arise in the measured physical properties.
To address this, NOK has developed a new evaluation method and device that allows tensile testing to be performed simultaneously with molding in an actual molding machine. Assessing test pieces immediately after molding improves data accuracy. These evaluation devices will be installed at the Shonan R&D Center (Fujisawa City, Kanagawa), NOK's hub for technology development, as well as at the Kumamoto Plant (Aso City, Kumamoto) and Fukushima Plant (Fukushima City, Fukushima). "Placing the equipment in production facilities helps prevent variations in evaluation results due to environmental factors such as temperature and humidity," explains Iwasaki.
Please enlarge the screen to view
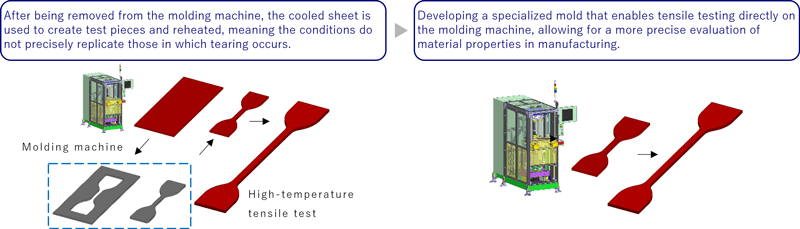
NOK is also developing a new evaluation method to assess the risk of rough-surface defects. A rough surface occurs when the outer layer of the rubber solidifies before it has fully spread across the mold.
Please enlarge the screen to view
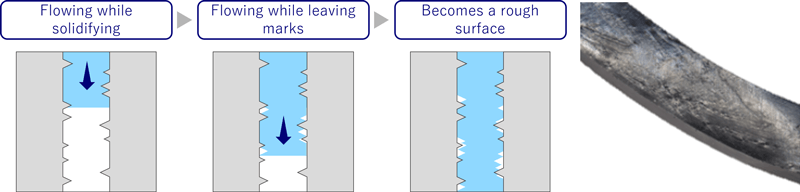
The new evaluation method uses a spiral flow mold designed with grooves similar to the shape of a mosquito coil. Rubber is injected from the center, allowing assessment in conditions closely resembling an actual mold's intricate and narrow spaces. This approach enables a more precise measurement of the filling time, the time it takes for the rubber to fully spread when rough surface defects occur. It also clarifies the correlation between rubber flow behavior and the degree of roughness in the final molded product. With accurate data, manufacturers can optimize production conditions, such as adjusting the amount of vulcanization accelerators or the mold temperature, to improve efficiency. Additionally, by integrating this method with rubber flow simulations, rough surface defects can be mitigated during the mold design phase, helping to prevent defects before production even begins.
Please enlarge the screen to view
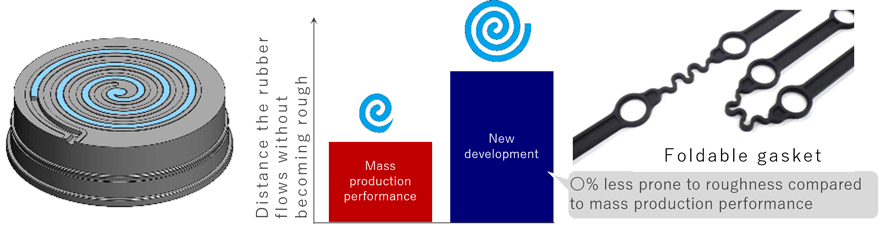
Through this new evaluation approach, NOK aims to reduce development lead time and minimize trial-and-error iterations during the manufacturing process.
Expanding scope to maximize benefits
Beyond developing the evaluation method itself, NOK is working to make the collected data more accessible by organizing it into a centralized database. This initiative allows measured material property data to be transferred directly to computers, enabling real-time analysis and review of results. NOK is also establishing a system that ensures key material property data is readily available for computer-aided engineering (CAE) simulations and for troubleshooting defects that arise during molding.
Iwasaki explains, "One of the challenges across the NOK Group is the transfer of technical knowledge. By compiling past experiments and evaluation data into a database, we aim to share expertise more efficiently and enhance data utilization."
The evaluation of material properties in manufacturing will be expanded beyond rubber to include other materials used by NOK Group companies. It will also extend to additional processes, such as material preparation and injection performance (charging). Since developing these evaluation methods takes several years, Maruyama explains, "we will prioritize tasks strategically to maximize impact."
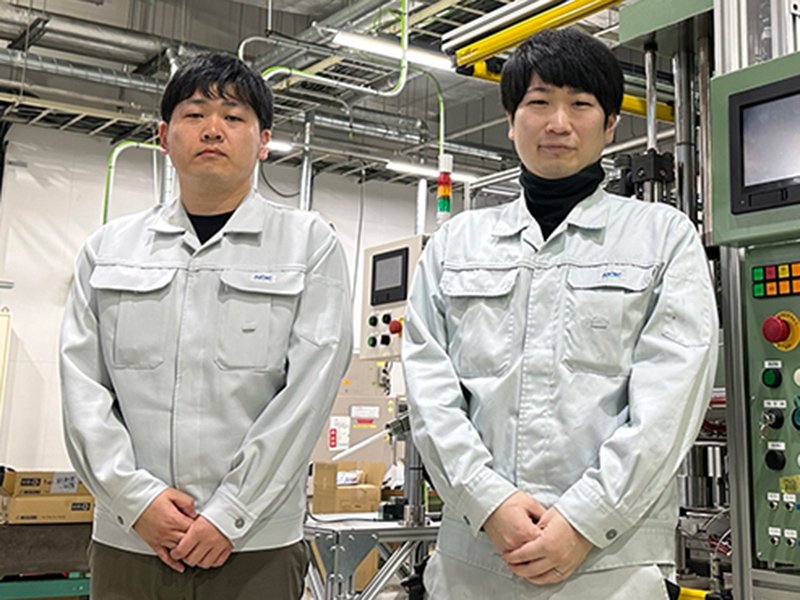
(Photo left)
Shunji Iwasaki
Section Manager, Processing Engineering Section, Manufacturing Research Department, NOK Group R&D, NOK Corporation
After joining NOK, Iwasaki worked in the research and development division, specializing in rubber processing technology. Following a role in the gasket prototyping department, he shifted his focus to CAE development for manufacturing technology. He has held his current position since 2024.
(Photo right)
Ryo Maruyama
Processing Engineering Section, Manufacturing Research Department, NOK Group R&D, NOK Corporation
After joining NOK, Maruyama worked in the research and development division, focusing on mold technology development. Since 2021, he has been engaged in the development of rubber processing evaluation technology.
- Note:Data, positions, and titles in this article are current as of January 2025.