NOK Adapts to Automotive Industry Changes with New Technologies
NOK's goal is to achieve consolidated sales of one trillion yen by FY2031, coinciding with its 90th anniversary. The automotive industry is undergoing a once-in-a-century transformation, and as a key supplier to the sector, NOK is evolving to handle these changes.
On May 22, 2024, at the Automotive Engineering Exposition 2024 held at Pacifico Yokohama, NOK showcased cutting-edge products and technologies to address critical societal challenges, including electrification and carbon neutrality (net zero greenhouse gas emissions). Earlier in April, the company introduced a unified corporate identity (CI) for its 92 Group companies worldwide, underscoring its commitment to innovation and collaboration. The exhibition featured standout technologies and products that reflect the Group's combined expertise.
Self-lubricating rubber contributing to improved EV energy efficiency
In response to the expanding electric vehicle (EV) market and the pursuit of new opportunities, NOK is introducing its innovative self-lubricating rubber. When used in the motor drive components of EV drive systems, such as the e-Axle, this material can reduce friction by up to 40%, enhancing energy efficiency compared to the company's conventional products.Co-developed with ENEOS, a leading oil and energy company, this rubber material prevents oil and grease from leaking through gaps in rotating and reciprocating shafts within machinery. NOK, which holds the largest market share of oil seals in Japan, is positioning this material as a key offering, with anticipated applications in the growing fields of robotics and hydrogen technology in the future.
Please enlarge the screen to view
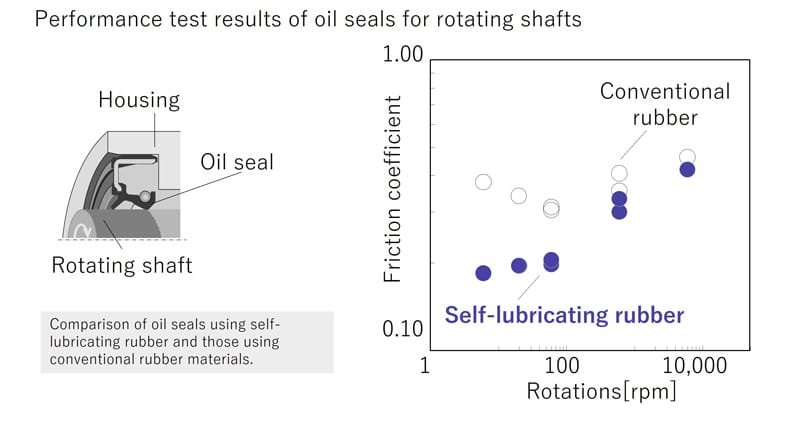
Traditionally, NOK has supplied oil seals for internal combustion engine (ICE) vehicles, sealing lubricating oil inside engines to reducing friction between metal components such as crankshafts during rotation. In recent years, the industry has been shifting toward reducing energy loss caused by oil stirring resistance, leading to the use of lower-viscosity lubricants — which are made as fluid as possible — to enhance fuel efficiency. Similarly, lubricants used in the sliding components of EV motors, such as those in e-Axles, are also trending toward lower viscosity to improve electric power efficiency.
The continuous and unidirectional rotation of internal combustion engines makes it relatively easy to maintain an oil film between the seal and the metal shaft. In EVs, however, the motor stops when the vehicle comes to a halt at traffic signals or during other stops, making it difficult to maintain an oil film during these intervals. When the vehicle resumes movement, the oil film re-forms. This constant stop-and-go pattern creates a harsh environment for oil seals.
Additionally, lower-viscosity lubricants are more prone to escaping from interfaces, which increases direct contact between the seal and the shaft and leads to accelerated seal wear.
To address these challenges, NOK partnered with ENEOS, a long-standing collaborator and an expert in oils, combining their expertise in seals and oils. "We exchanged ideas and technology to create this product together," explains Takahiro Anzai, superviser of the Materials Research Section at the NOK R&D Center.Unlike conventional approaches involving surface modification or coatings, this self-lubricating rubber was developed by optimizing its formulation to control interfaces at the molecular level. This innovation enables the oil film to remain more effectively between the rubber and the metal.
This technology reduces oil seal wear and is expected to extend their lifespan. NOK envisions applications for self-lubricating rubber not only in EVs but also in robots, which operate at lower speeds than automotive engines and frequently reverse rotational direction, making this material particularly suitable for them. "I would be delighted if this technology spreads globally and makes a meaningful contribution," says Yuichi Aoyagi, manager of the Materials Research Section at the NOK R&D Center. He also expressed optimism about showcasing the product, emphasizing that raising awareness is the first step toward achieving this goal. NOK also aims to expand into new fields it has identified as growth sectors, such as hydrogen-related technologies.
Preventing EV battery thermal runaway with pressure control valves
While global demand for EVs has slowed recently, NOK anticipates medium- to long-term growth, and is strengthening its product offerings for this market. One of these is a series of pressure control valves currently under development, designed to prevent fires and explosions caused by "thermal runaway" in EV batteries. These valves are installed on the sides of battery packs and release pressurized gas built up inside the packs.
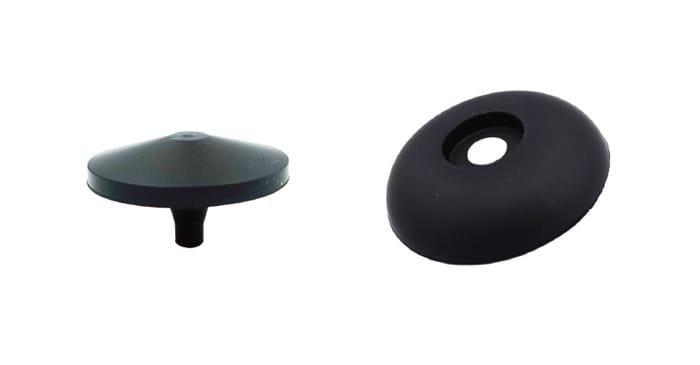
Under normal conditions, the pressure control valves prevent water and dust intrusion. In the event of abnormal internal pressure, the gas release area and airflow volume are linked. NOK proposes three different types based on flow volume and product size. The high-flow type can release 4,000-6,000 liters of gas per minute, the medium-flow type releases 2,000-4,000 liters per minute, and the small-flow type releases less than 200 liters per minute. These options allow battery manufacturers to select the appropriate valve based on installation location, available space, and required ventilation performance.
The high-flow type is an assembled product consisting of a plate and cover with an integrally molded seal lip and a spring. The seal lip is directly bonded to the plate, making it more reliable than products assembled from individual materials such as rubber, resin and metal. Additionally, the spring is a flat spring, which reduces the product height by approximately 20 millimeters compared to similar products using coil springs. This product meets the IPX9K rating for protection against high-pressure steam jet washing, as defined by the Japan Quality Assurance Organization's high-pressure steam cleaning jet test.
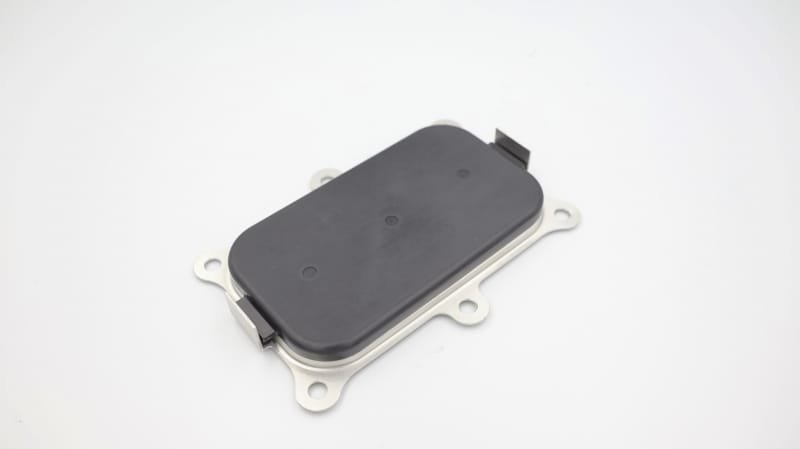
These features were made possible by NOK's rubber design technology and the processing techniques of its partner manufacturers. Naoki Hagiwara, from Product Development of the Gasket and Boot Business Unit, was in charge of the development. He shares his aspirations: "As the EV market grows, I would be delighted if this product, which plays a crucial role in safety, is adopted and makes a meaningful contribution."
The low-flow type features a rubber valve with an umbrella-shaped design, while the medium-flow type uses a rubber umbrella valve secured with pins or bolts, resulting in a simple structure. Opening pressure and flow volume can be adjusted by varying the diameter, rubber thickness, hardness and compression margin. These valves are compact and have fewer components, making them cost-efficient. The rubber materials can be selected to suit the sealed object, including flame-retardant materials equivalent to UL94-V0 grade.
NOK's in-house capabilities include evaluations of heat resistance, durability, and vibration resistance for pressure control valves and flow tests that mirror actual usage conditions. This ability to conduct comprehensive testing is a major strength of the company. All three types — low-, medium- and high-flow — have already garnered customer interest, and further expansion is anticipated.
Jiro Nagashima, from Product Development 2 of the Precision Moldings & O-rings Business Unit, expressed enthusiasm for future development, stating: "We intend to continue developing products that closely address the challenges our customers face."
- Note:Flow volume figures are based on a differential pressure of 15 kPa (internal pressure relative to external atmospheric pressure) per minute.
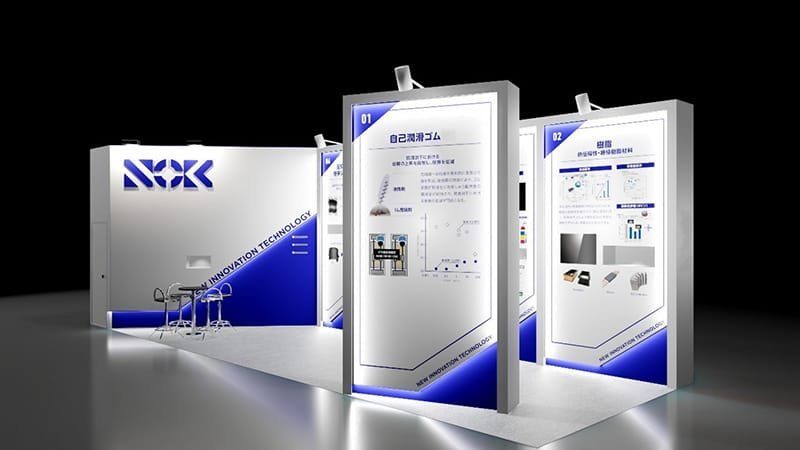
- Organizer: Society of Automotive Engineers of Japan, Inc.
- Dates: Wednesday, May 22 - Friday, May 24, 2024
- Venue: Pacifico Yokohama Exhibition Hall (North)
- List of NOK’s products for electric vehicles
- NOK Virtual Booth
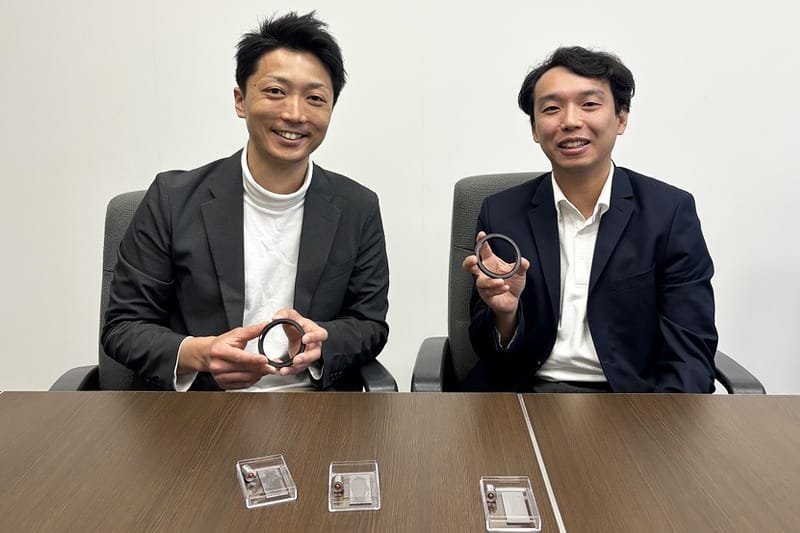
(Photo left)
Takahiro Anzai
Supervisor, Materials Research Section, NOK R&D
After joining NOK, Takahiro Anzai was responsible for analytical work and material development. From 2017, he worked on the development of materials for oil seals. Since 2019, he has been engaged in research on sealing technologies, including low friction. In 2022, he began collaborating with Professor Ken Nakajima of the Tokyo Institute of Technology on research related to controlling the physical properties of rubber.
(Photo right)
Yuichi Aoyagi
Manager, Materials Research Section, NOK R&D
Yuichi Aoyagi specialized in quantum chemistry during his graduate studies. After joining NOK, he worked on rubber material research and the development of analytical techniques. He was seconded to NOK's partner company, Freudenberg (Germany), where he researched the mechanisms of seal rubber materials degradation at the DIK (German Institute for Rubber Technology) in 2018 and earned a doctorate. He is currently involved in material research activities supporting the foundation of the NOK Group.
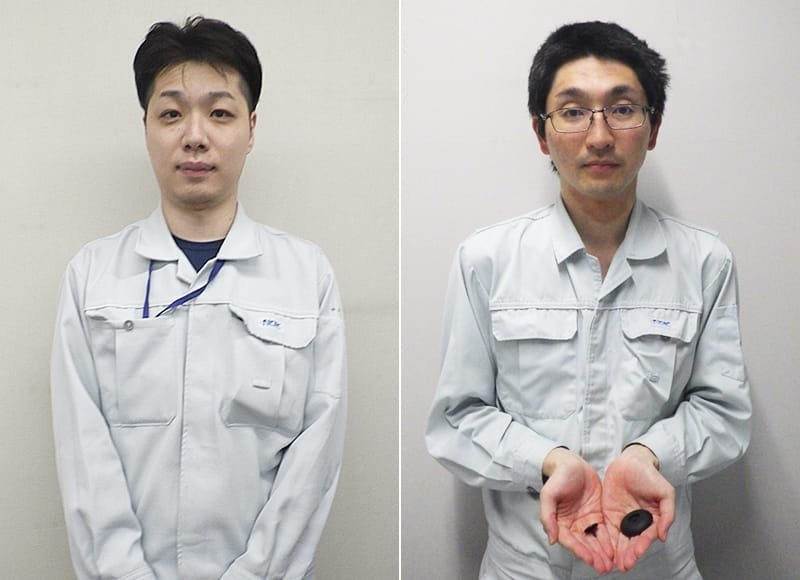
(Photo left)
Naoki Hagiwara
Product Development of the Gasket and Boot Business Unit
Since joining NOK, Naoki Ogiwara has been engaged in the design and evaluation of rubber overmolded products, which are components where rubber is integrally molded with materials such as metal or resin. In 2022, he began working on the development of pressure control valves, and he is currently mainly responsible for the design and development of products for new applications such as EVs, including pressure control valves.
(Photo right)
Jiro Nagashima
Product Development 2 of the Precision Moldings & O-rings Business Unit
After joining NOK, Jiro Nagashima was responsible for quality control of products in the Precision Moldings & O-Ring Business Unit. Since 2012, he has been involved in the design of products such as O-rings and gaskets, and in recent years has mainly been engaged in the development of pressure control valves.
- Note:Data, positions and titles in this article are current as of May 2024.