Driving Reliability with Lubricants: NOK Klüber
The NOK Group holds the largest domestic market share in oil seals and O-rings, and our products contribute to the stable operation of a diverse range of machines. These include automotive engines, powertrains, hydraulic equipment in construction machinery, and multifunction printers. Beyond our seal technologies, such as those used in oil seals and O-rings, the Group also ensures stable operation by reducing wear on moving parts in machinery through lubricants. NOK Klüber, based in Minato, Tokyo, takes on this essential role.
Lubricants as essential core materials
Lubricants reduce friction and wear in contact areas, such as rotating shafts or gears where metals or other solids come in contact with each other. To explain this in more familiar terms, the hydroplaning phenomenon that occurs on rainy or snowy days — when a thin film of water forms between the tires and the road surface — can reduce friction at the contact point and make tires slip. In this situation, the water acts as a lubricant, lowering the friction needed for stable contact.
Lubricants are available as liquid oils, semi-solid greases and solid coatings, and their use varies depending on the application. According to Akira Otani from the Application Engineering Section of NOK Klüber's Development Department, lubricants are indispensable because machinery would break down quickly without them. However, simply apply lubricants indiscriminately is not enough. To maximize a machine's performance requires selecting and using lubricants suited to specific applications and characteristics.
Data highlights the importance of lubricants. Research from a U.S. study, for example, shows that 55% of roller bearing failures involve lubrication issues. A closer look reveals that contamination by incompatible lubricants (25%) and incorrect lubricant selection (20%) are among the main reasons for these failures. Otani emphasizes that "lubricants are critical functional materials in ensuring that machinery reaches its full lifespan."
What are lubricants made of? According to Masaki Tahara from the Chemical & Tribology Section of NOK Klüber's Development Department, oils are composed of a base oil and additives, while greases include an additional thickener to give them a semi-solid composition. Base oils can be mineral, synthetic or fluorinated, while additives primarily consist of substances like antioxidants and rust inhibitors. Coatings, on the other hand, have a different composition. They combine a base binder resin with additives and solid lubricants that offer lubrication properties. NOK Klüber has approximately 2,000 products, and the company selects and/or develops the most suitable lubricant based on the user's operating environment.
Please enlarge the screen to view
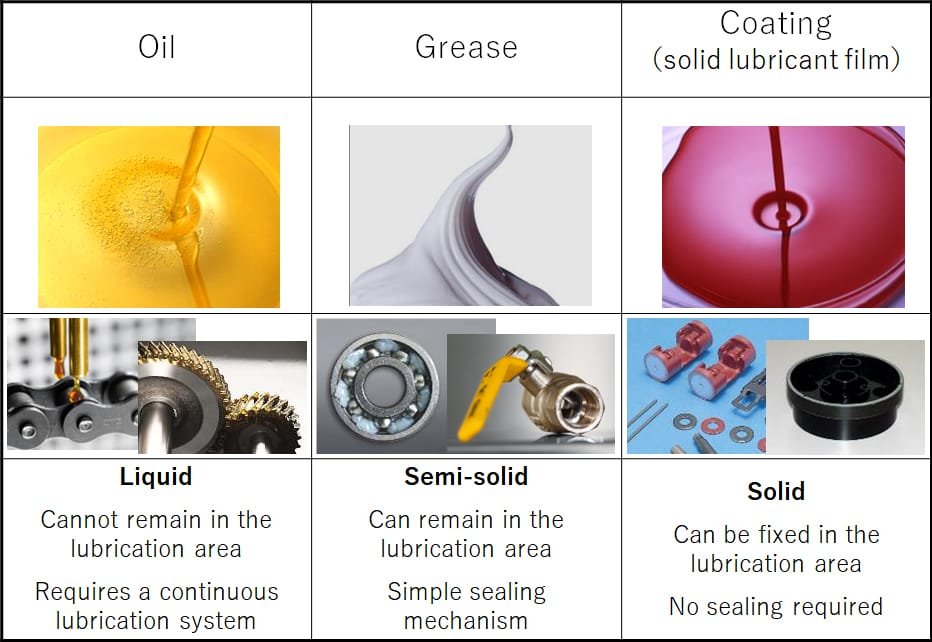
Strength in specialized applications
NOK Klüber specializes in lubricants designed for niche areas that require specialized performance, such as extreme environments involving low temperatures, high loads, high temperatures, or vacuum conditions. According to Tahara, the company's strengths include formulation design technologies, the handling of small quantities and many types of products, and meticulous technical services that address specific customer needs.
Established in 1976, NOK Klüber is jointly owned by NOK (51% stake) and Klüber Lubrication München GmbH & Co. KG, a German company in the Freudenberg Group that is a global leader in specialty lubricants (49% stake). Initially, the company's primary role was serving as a distributor for Klüber Lubrication München's products in Japan. As the need arose to customize products for domestic users, however, NOK Klüber formed its own development team and now independently develops and supplies its own products. Its customers span a wide range of industries, including automotive, construction machinery, robotics, shipping, chemicals and semiconductors.
Leveraging the NOK Group's network, NOK Klüber regularly generates proposals and ideas as a dedicated lubricant division. It has recently expanded into new applications such as food machinery and wind-power generation.
The needs for lubricants are also changing.
Given its involvement in diverse industries, NOK Klüber's lubricants must meet a wide range of performance demands, including operating in temperatures from -40°C to 200°C, low friction, and high durability. Tahara explains: "In the future, demand will shift toward lubricants that support miniaturization, high output, and low-temperature performance."
These needs will extend beyond miniaturization, high output, and low-temperature compatibility, Tahara adds. Among such innovations, for example, one standout product that addresses these demands is "self-locking grease," explicitly developed as a lubricant for automotive power windows.
Self-lock grease was created to prevent power window malfunctions. In the past, issues such as windows being forcibly pushed down by hand or sliding down under their own weight were common. Self-locking grease had to combine two seemingly contradictory properties: easily transmit force from the motor while also resisting the force from the window. In other words, friction had to be reduced when the mechanism moved, and increased when stationary. NOK Klüber successfully controlled friction by using the unique properties of solid lubricants added to the grease. They achieved this by optimizing factors such as the type, hardness, shape, and amount of added particles.
Looking ahead, the company will promote its ability to achieve such opposing performance characteristics and expand the applications for self-locking grease.
Please enlarge the screen to view
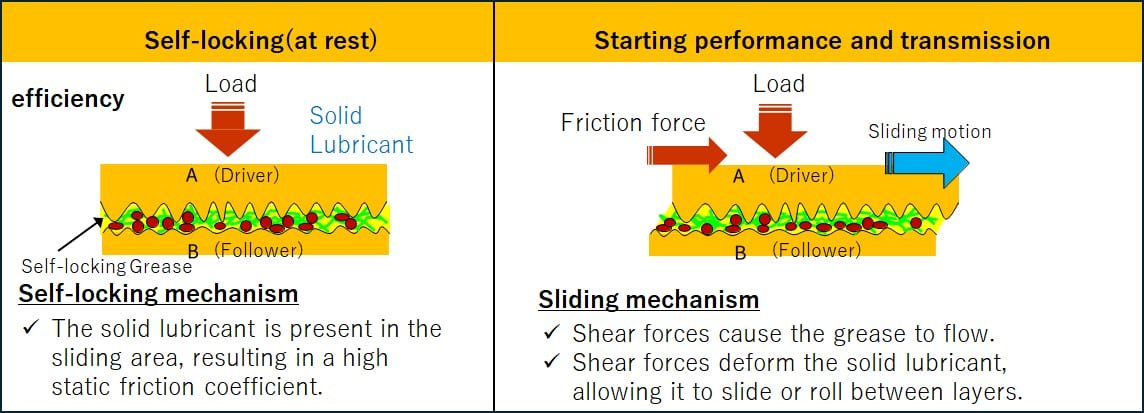
Meeting user needs
Lubricants are critical functional materials that support various machines, but they can only perform effectively if tailored to each specific machine. Tahara explains: "Since the structure of machine parts and the way forces are applied vary for each user, fine-tuning the lubricant to match these conditions is essential. That's where our lubricant development capabilities come into play." However, while lubricant development requires close collaboration with users, users often don't fully understand the necessity of optimization. Communicating the essential nature of lubricants and fostering deeper engagement with users remains a challenge.
Another emerging theme is the development of environmentally friendly products. NOK Klüber is developing biodegradable lubricants and products derived from biomass materials. Otani states: "Minimizing the maintenance frequency of products that use lubricants is another way to differentiate ourselves. We promote our high-performance greases by emphasizing these advantages, particularly for general industrial machinery."
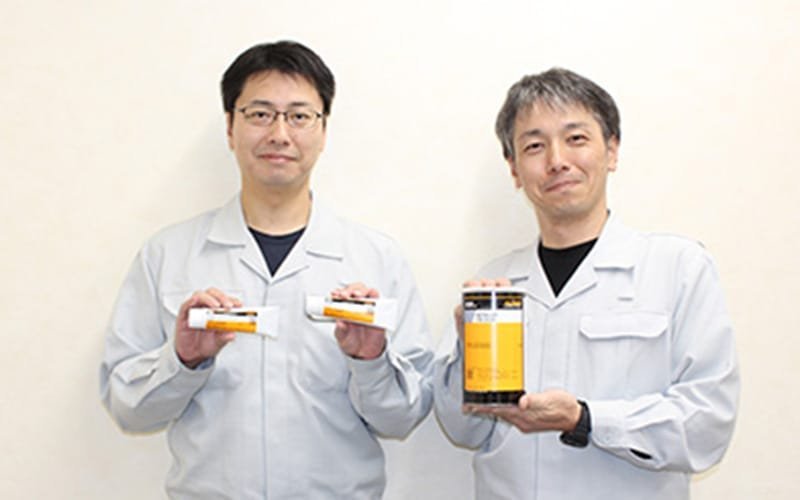
(Photo left)
Masaki Tahara
Manager, Head, Chemical & Tribology Section, Development Department, NOK Klüber Co., Ltd.
After helping to develop solid lubricant coatings and surface treatment agents for rubber, Masaki Tahara transitioned to product design for greases and oils. In October 2024, he transferred to the Chemical & Tribology Section, where he is focused on developing lubricants using sustainable new materials and collaborating on joint development projects within the NOK Group.
(Photo right)
Akira Otani
Manager, Head, Application Engineering Section, Development Department, NOK Klüber Co., Ltd.
After joining the company, Akira Otani was involved in tribology research and technical support for mechanical components such as switches and gears within the Development Department. From 2016, he spent six years in the Sales Planning Department, handling planning-related tasks. In October 2022, he returned to the Development Department, where he now works as an application engineer, assessing existing products and making proposals to identify and meet customer requirements.
- Note:Data, positions and titles in this article are current as of October 2024.