Differentiation Through Group Strength: Acrylic Polymers as Core Materials
NOK's seal products — including its flagship oil seals — primarily use synthetic rubber, which is a common material in automotive components because of its essential oil and heat resistance. The main element of acrylic rubber is acrylic polymer, which is essential to determining the performance of oil seals and other similar products. Unimatec, a member of the NOK Group based in Minato, Tokyo (led by President Hiroaki Kikuchi), specializes in developing and producing acrylic polymers. As the automotive industry's business environment evolves, Unimatec leverages the Group's strengths to meet diverse needs.
Acrylic polymers determine oil seal performance
Acrylic polymers are commonly found in consumer goods and cosmetics. However, they are also widely used in industrial applications such as hoses, adhesives and coatings. Unimatec supplies acrylic polymers as materials for automotive oil seals and gaskets. The development of acrylic polymers initially focused primarily on seal applications. Over time, though, Unimatec has applied its expertise to create grades suitable for automotive hoses, and its acrylic polymers are now widely used in hose products as well.
According to Hiroyuki Sano, Department Manager of the Elastomer Engineering Department at Unimatec, the rubber portion of an oil seal (excluding metal components,) typically consists of 60 to 70% acrylic polymer. However, other additives and materials also play critical roles in determining the product's performance. To optimize these materials, Unimatec closely collaborates with NOK's Materials Development Department to drive the development of both oil seal formulations and acrylic polymers.
Key properties: heat resistance, oil resistance and cold resistance
The essential characteristics required of acrylic polymers for automotive engine-related seal products are heat resistance, oil resistance and cold resistance. Oil seals are commonly used in engines, crankshafts and transmissions, making these three properties crucial. Acrylic polymers must balance these attributes to meet varying needs. For example, engine oil seals operate at temperatures between 150°C and 170°C, and must demonstrate strong oil resistance. Additionally, given that vehicles operate in cold climates, cold resistance is indispensable. Developing well-balanced acrylic polymers requires in-depth knowledge of the final product's applications and the capability to ensure reliability during extended use. This process cannot rely solely on Unimatec's efforts; it requires the collective strength of the NOK Group.
Please enlarge the screen to view
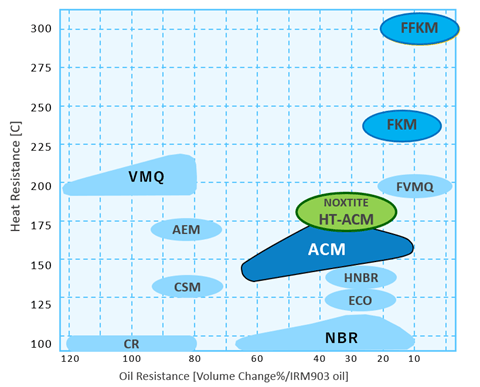
The chemical structure of acrylic polymers consists of a carbon-based main chain with no double bonds, while various alkyl ester structures are connected to the side chains. The components of these alkyl ester structures determine the balance of heat resistance, oil resistance and cold resistance. "We try to anticipate what characteristics users will demand, and proceed with development accordingly," says Unimatec's Sano.
Collecting feedback on changing needs and user demands relies heavily on NOK's strong marketing capabilities, so the Group maintains robust connections with suppliers and automakers. As a leading manufacturer of oil seals, NOK plays a pivotal role in understanding how Unimatec's acrylic polymers perform when used in oil seal production. This expertise is gained through close collaboration with NOK, allowing Unimatec to develop acrylic polymers tailored to the required performance of the final products.
Currently, Unimatec offers five key products (and ten grades) of acrylic polymers designed for seal and hose applications, targeting essential functionalities for each use. The company also provides a wide range of products to meet various requirements.
Please enlarge the screen to view
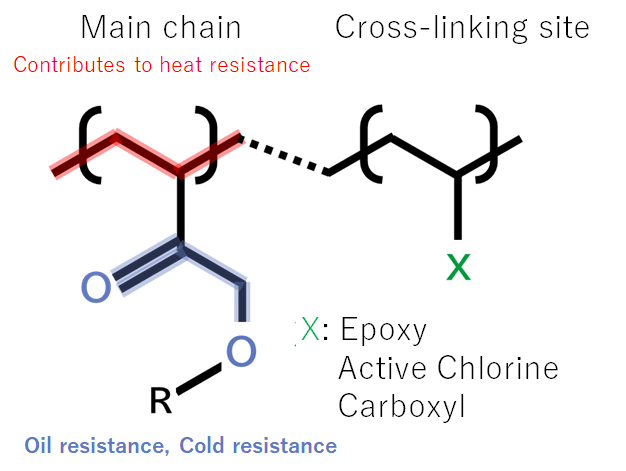
Please enlarge the screen to view
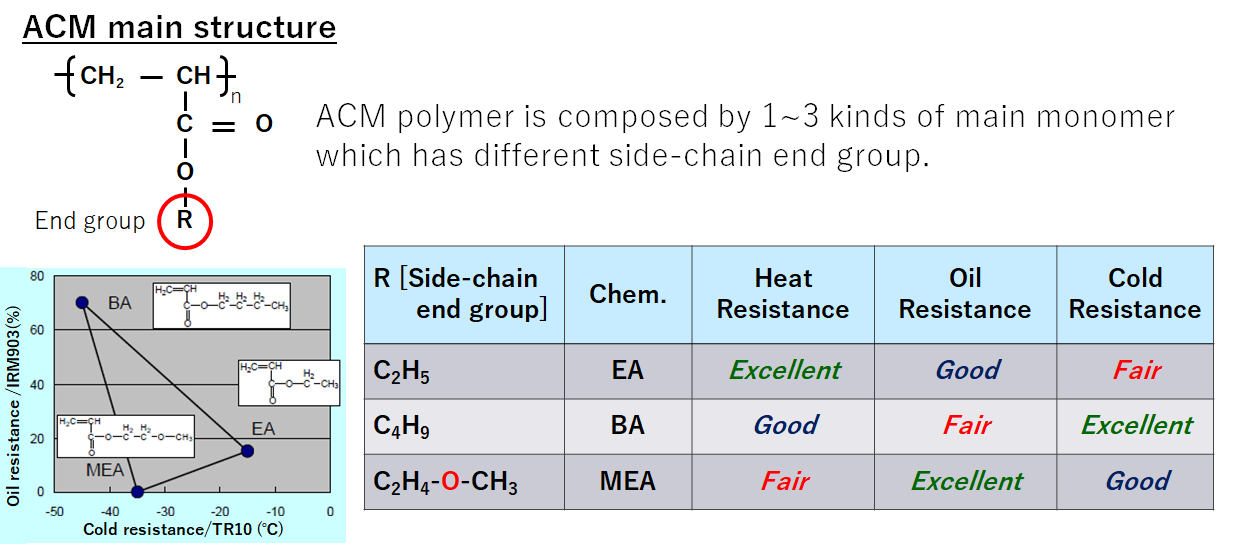
Leveraging Group strengths to enhance technical capabilities
NOK carries out product evaluations and oil seal formulation design, providing Unimatec with a significant advantage. "Even if we develop an acrylic polymer that we think is great, we quickly receive feedback like, 'It's not quite right, and this part doesn't work,' " Sano says, highlighting how the process strengthens Unimatec's development capabilities.
Establishing a stable supply system is also essential for a polymer manufacturer. Unimatec's production system for acrylic polymers is not limited to its primary site in Kitaibaraki, well northeast of Tokyo; it has also developed a second production base in Singapore (Unimatec Singapore). This dual-site approach ensures a robust business continuity management system, enabling stable production at both locations through accumulated technical expertise.
Moreover, for sales outside the NOK Group — particularly for hose applications — it is crucial to propose formulations tailored to customer needs beyond just supplying these polymers. In such cases, NOK employs techniques like machine learning-based formulation prediction to boost efficiency and accelerate the speed of formulation proposals.
Looking ahead, Sano expresses interest in exploring materials informatics, which use data science to enhance development capabilities.
Please enlarge the screen to view
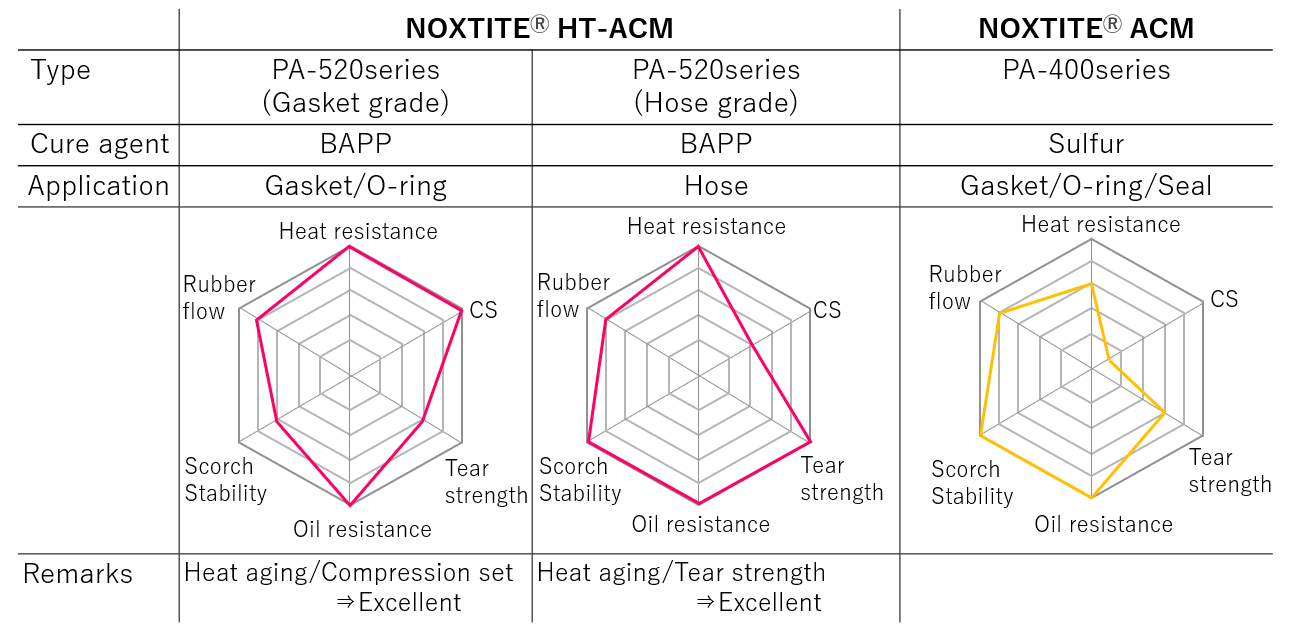
Getting ready for sweeping changes in the automotive industry
The automotive industry is undergoing significant transformation. The rise of EVs, which require fewer components, is expected to reshape existing supply chains. Engine components in particular are expected to change radically, sparking concerns that manufacturers specializing in engine parts may struggle to remain viable.
NOK, which excels at making engine oil seals, is tackling the challenge of exploring new markets throughout the Group. For Unimatec, opening up new fields is also a crucial mission. The company is conducting research and investigations with an eye on new sectors, targeting areas such as healthcare and battery technology.
Even with the growing adoption of EVs, engines are not expected to disappear anytime soon. With a mid - to long-term perspective — looking one to two decades ahead — Unimatec is eager to discover new opportunities by collaborating with universities and other institutions.
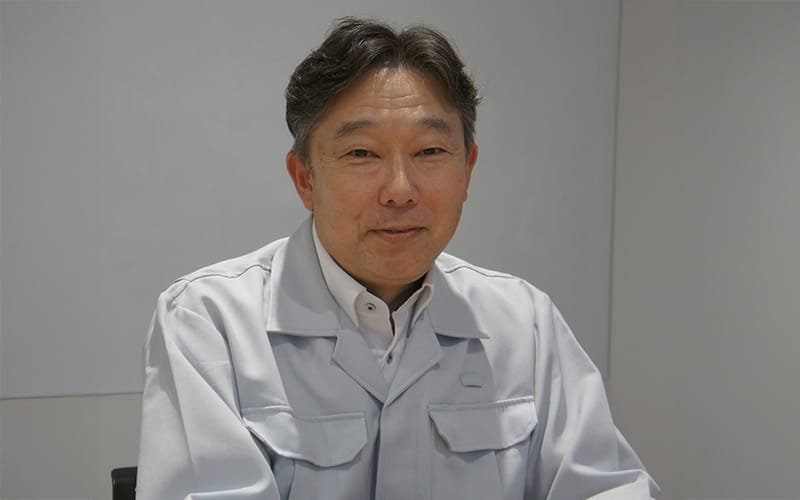
Hiroyuki Sano
Department Manager, Elastomer Engineering Department, Unimatec Co., Ltd.
After joining NOK, Hiroyuki Sano was responsible for developing rubber materials, helping to create materials for various NOK products. He later focused on material research and analysis before transferring to Unimatec in 2019. Shifting from using polymers to producing them, he now leverages his extensive expertise to drive new development projects.
- Note:Data, positions and titles in this article are current as of October 2024.