Making a Hydrogen Society Possible with Rubber Technology
The push to promote hydrogen use is gaining momentum. As carbon neutrality (net zero greenhouse gas emissions) becomes a cucial goal for industries worldwide, hydrogen and ammonia are spotlighted as energy sources that do not emit carbon dioxide (CO2). Ammonia derived from hydrogen further elevates expectations for hydrogen as a next-generation energy source.
Leveraging comprehensive expertise and technologies
NOK has cultivated a wide range of materials, design and manufacturing expertise through its core products, such as oil seals and O-rings. By leveraging these capabilities, NOK is helping to create a hydrogen society.
NOK's hydrogen-related product lineup includes a gasket for fuel cells (FCs) used in vehicles and households, known as CELLSEAL, as well as hydrogen-resistant O-rings, humidification membranes that recover water vapor generated within FCs from exhaust gases to humidify intake gases, and hydrogen control solenoid valves that regulate hydrogen gas pressure. NOK also offers gaskets for water electrolysis systems that produce hydrogen from water. These products are indispensable across the entire hydrogen infrastructure, encompassing hydrogen production, storage, transportation and utilization.
Supporting fuel cell advancements: CELLSEAL
Among these products, NOK's expertise and knowledge are most evident in CELLSEAL. A CELLSEAL is used inside the cells that make up FCs. A cell consists of separators made of metal or graphite plate sandwiching a catalyst layer. Stacking approximately 300 of these cells creates an FC. Hydrogen, oxygen and water flown inside the cells, and gaskets seal them off to prevent leakage. Gas leaks compromise performance and also pose significant safety risks, making gaskets crucial components.
FCs require high output and improved power generation efficiency, leading to advancements in cell miniaturization and multilayering. Gaskets also need to be miniaturized, with increasingly stringent standards for positional accuracy during assembly.
NOK has fully utilized its long-standing technologies and expertise to establish a technique for integrally molding separators and gaskets. Through integral molding, positional and dimensional accuracy at the micrometer level (a micrometer is one-millionth of a meter) has been achieved. When FC manufacturers assemble 300 cells under pressure simultaneously, any misalignment in the shape or position of the gasket can result in uneven force distribution, causing gaps and preventing the FC from delivering its expected performance. Additionally, integral molding reduces manufacturing processes and helps control costs.
As further multilayering and miniaturization are anticipated, integral molding is expected to become an indispensable technology for FCs.
Please enlarge the screen to view
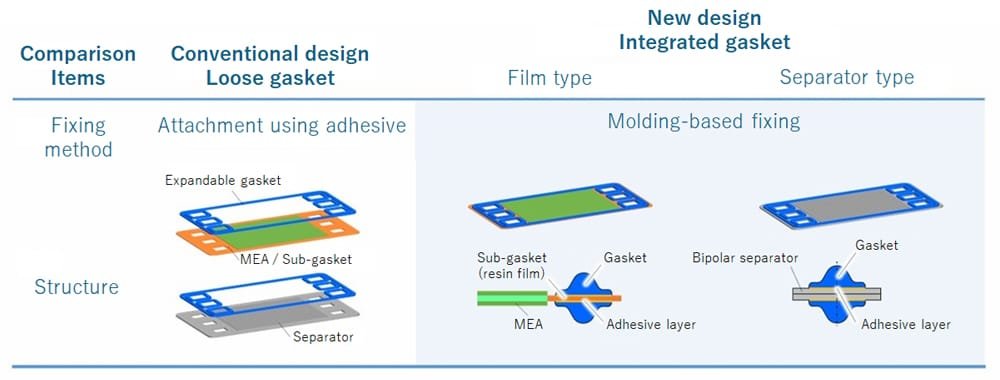
Taisuke Matsuda of the NOK Group R&D FC Solution Advanced Development Department was involved in developing CELLSEAL. He explains the challenges of manufacturing them: "Integrated molding uses injection molding machines. The rubber material for CELLSEAL is either liquid or solid, and solid materials in particular have difficulty flowing evenly within molds. NOK possesses the technology needed to manage the design, temperature and pressure required to flow materials uniformly through fine channels."
The materials themselves also pose challenges. Matsuda notes: "For example, commercial vehicles demand high durability in automotive fuel cells, while passenger vehicles require low-temperature resistance for cold climates. The required functions vary depending on the application, which naturally affects the composition of the rubber material." He emphasizes NOK's strengths In this regard: "We have the technology to select materials and establish production processes that balance the necessary functionality and cost."
Applying technologies already developed to other products
Commercial vehicles are expected to adopt automotive FCs earlier than passenger vehicles. These vehicles require higher durability and longevity. This means that components must be designed to last longer to ensure that FC adoption moves forward, which could lead to changes in separator requirements. NOK is determined to refine its technology to seamlessly integrate any type of separator material. The company intends to build capabilities that meet diverse requirements and performance standards to stay ahead of competitors. NOK also plans to apply the technologies developed through CELLSEAL production to other NOK products.
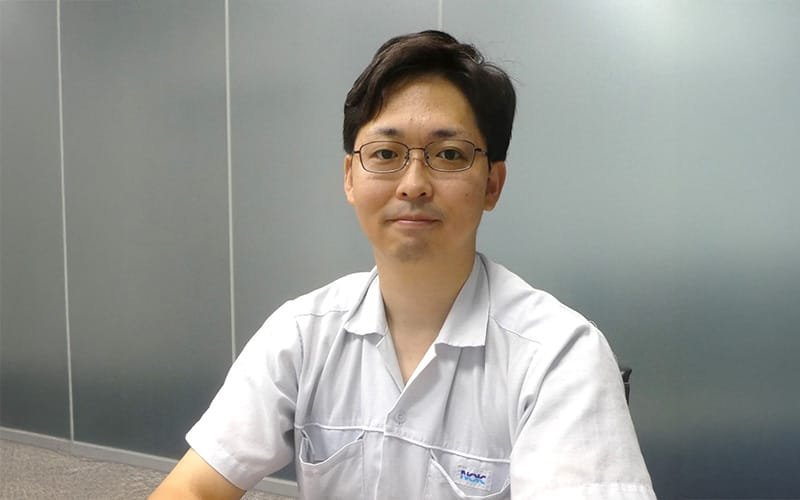
Taisuke Matsuda
Development Section, FC Solution Advanced Development Department, NOK R&D, NOK Corporation
After joining NOK, Taisuke Matsuda worked in the Technical Research Department, supporting technology for FC CELLSEAL. Since 2018, he has been engaged in developing CELLSEAL, and is currently working on gasket molding technology for carbon separators.
- Note:Data, positions and titles in this article are current as of September 2024.