Leveraging Material and Design Expertise to Ensure Safety and Reliability in Electric Vehicles
The advent of electric vehicles (xEVs) presents many new challenges, including thermal management and electromagnetic noise. Drawing on its expertise in material formulation and shape design gained while developing seal products, NOK offers a lineup of high-performance products tailored for electric vehicles, including a wide range of components and products to meet customer expectations. Senior Planner Junichi Watanabe and Masahiro Tanioka, manager of the Mobility Products Planning Section,NOK R&D Technical Planning Department at NOK, shared insights into NOK's offerings for electric vehicles.
Flame-retardant materials and designs to prevent fire from spreading
"Currently in development, NOK's insulated and flame-retardant rubber sheet is placed between battery cells to reduce heat transfer and suppress the spread of fire in the event of thermal runaway. This is essential for nickel-manganese-cobalt (NMC) lithium-ion batteries (LiBs), which offer high energy density but are prone to thermal runaway caused by overcharging or internal short circuits.
The sheet's flame-retardant properties meet the high-grade "V-0" rating of the U.S. UL 94 standard. Additionally, compared to flat sheets, the sheet's protrusions reduce the contact area between the sheet and the battery cell, creating an air layer that enhances thermal insulation. These protrusions compress to absorb the cells' deformation during the charging and discharging cycles. The compressive properties can also be adjusted by modifying the shape of the protrusions."
Innovative manufacturing that contributes to carbon neutrality
NOK also proposes products that contribute to decarbonization across the supply chain. To extend driving range, automakers are equipping vehicles with large-area batteries set under the floor. This requires large-size gaskets for the battery cases. Conventional gasket manufacturing involves preparing molds to shape the gasket. For larger areas, that requires a large heating range during the vulcanization process, consuming significant energy. To address this, NOK developed a new method for its large-size gaskets, forming them in a compact, folded state. These gaskets are then unfolded when attached to the counterpart component. Two types of large-size gaskets are available: foldable rubber and spiral gasket. Both can be flexibly adjusted to fit the installation area. The foldable rubber gasket does not require a groove in the counterpart component for fitting. Instead, it is positioned using guide pins, and can accommodate a circumference of approximately two meters. The spiral gasket, which fits into a groove on the counterpart component, supports circumferences of up to around six meters.
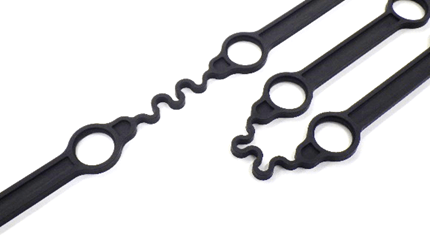
Preventing radio noise and electrical corrosion to ensure safety and durability
The conductive ring addresses specific challenges caused by high-voltage motors. These motors produce electric currents that cause the shaft to become electrically charged, which can generate noise that interferes with radio reception. Radios are critical communication tools during disasters, so equipping electric vehicles with functioning radios makes this a pressing issue. Additionally, prolonged shaft charging can cause electric currents to pass through the bearings supporting it, leading to discharges (sparks) that melt the rolling surfaces of the bearing balls — a phenomenon known as electrical corrosion. This reduces the bearings' lifespan, necessitating countermeasures. To address these issues, NOK has developed products that enable electrical conduction from the shaft to the housing. These products include a type using conductive rubber, a type combining an oil seal with conductive fabric, and a type combining an oil seal with conductive fluoro resin (PTFE). Compared to conventional conductive products used to prevent shaft charging, such as ground brushes and knuckle grounds, these solutions offer the advantages of being more space-efficient and cost-effective.
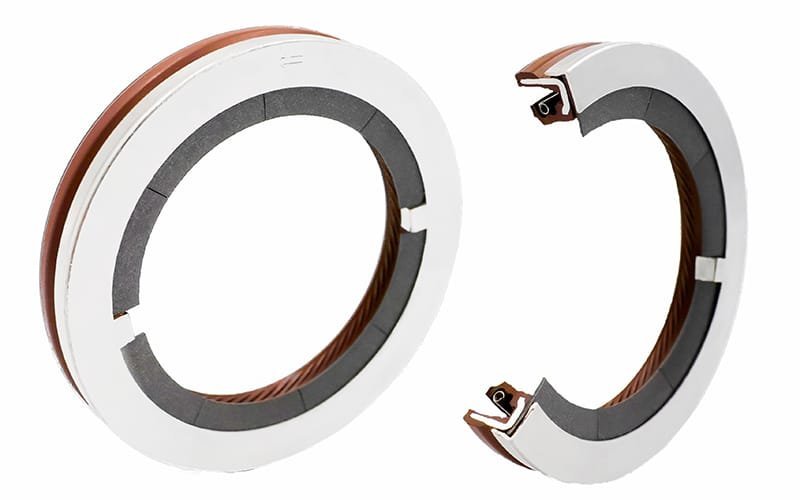
Proposing variations tailored to customer needs
NOK offers a range of heat-conductive materials that can be applied to various components. With options tailored to customer requirements, the variations include combinations of thermal conductivity, hardness, and heat-resistant materials. The QLEASE rubber type, for example, retains the elasticity of rubber while achieving several times the thermal conductivity of standard rubber. This material can be molded into three-dimensional shapes to fit the contours of complex electronic enclosures and uneven circuit boards, increasing the contact area and improving heat dissipation efficiency. In addition to its excellent heat dissipation properties, QLEASE also absorbs the expansion and contraction of components caused by heat.
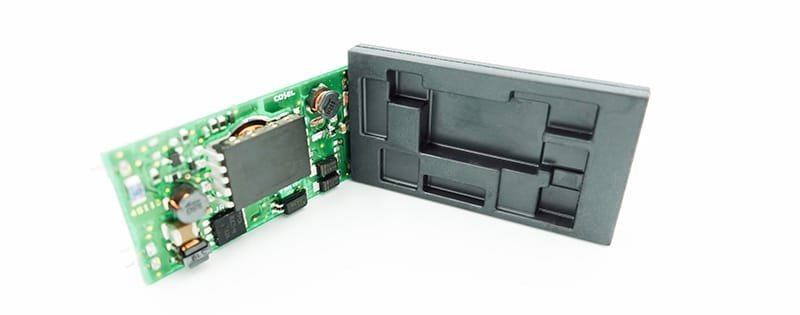
The QLEASE "clay" type in the same series is clay-like in consistency, allowing for even greater flexibility to conform to heat-generating components. To enable automated assembly, a lower-viscosity version that can be applied using a dispenser has been developed, as well as a hybrid type that combines rubber and clay. As a material that balances the opposing properties of thermal conductivity and electrical insulation, NOK also offers the Quantix series. NOK's technical partner, Germany's Freudenberg, developed this resin material. For electric vehicles, the series is intended for use in applications requiring high insulation for safety, such as motor bobbins and molded bus bars. Depending on the application and required functionality, NOK provides optimal thermal management solutions ranging from clay to resin and rubber.
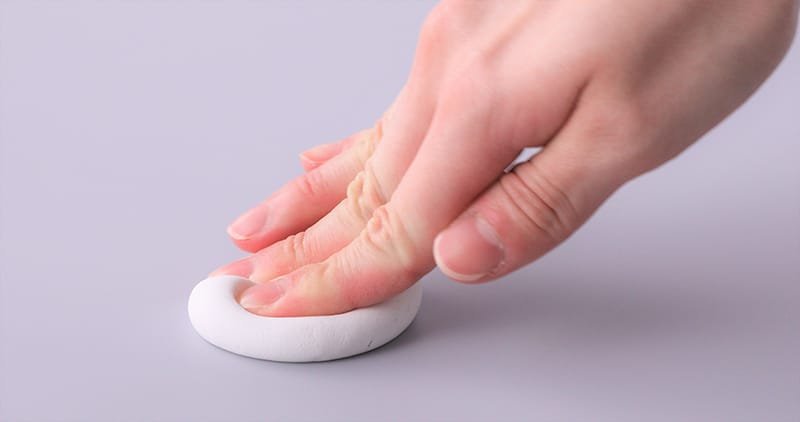
Experience the technology through games and demos
At Japan Mobility Show 2023, NOK showcased a wide range of products and technologies expected to play key roles in the future of mobility, including its conductive ring. The exhibition booth was designed with a game center theme, introducing NOK's technologies for safety and comfort through interactive games and demonstrations. In addition to its core seal products, the booth showcased new fields such as biometric sensing to monitor driver conditions. With visitors coming from the automotive industry and other sectors, the event was an excellent opportunity to enhance brand recognition and widely promote NOK's technologies and product lineup.
[Visit the virtual booth here]
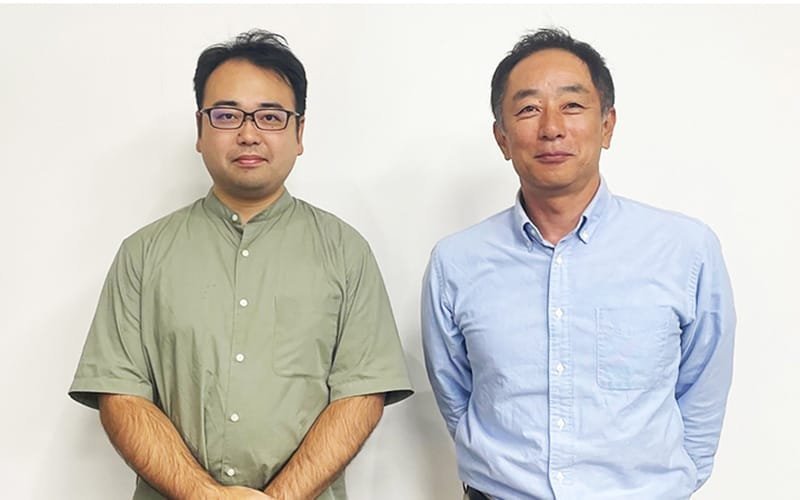
(Photo right)
Masahiro Tanioka
Manager, Mobility Product Planning Section,NOK R&D Technical Planning Department, NOK Corporation
After joining NOK, Masahiro Tanioka worked in the sales department. In 2023, he transferred to NOK R&D's Product Planning Department, where he is primarily responsible for mobility-related planning.
(Photo left)
Junichi Watanabe
Senior Planner, Mobility Product Planning Section,NOK R&D Technical Planning Department, NOK Corporation
Junichi Watanabe joined NOK in 2009 and initially worked in technical sales for major automobile manufacturers. Since 2021, he has been involved in sales planning for e-mobility. In 2022, he transferred to NOK R&D, where he focuses on product planning for e-mobility.
- Note:Data, positions and titles in this article are current as of September 2023.