Providing Solutions That Meet Needs Quickly: Leveraging Statistical Methods for Material Formulation
Over the years, NOK has accumulated approximately 88,000 rubber material formulation recipes developed in response to changing needs and demands. Currently, the company leverages this vast dataset of recipes to optimize new material formulations through statistical methods. This approach shortens development time and serves as a powerful tool to quickly respond to needs even amidst rapid environmental changes, such as improving vehicle fuel efficiency and adapting to electrification.
Strength in mass-producing products with diverse performance
Since its founding in 1941, NOK has been dedicated to rubber research and development, achieving a substantial body of work reflected in its accumulated data. NOK handles approximately 5,500 types of raw materials, including rubber, vulcanizing agents, reinforcements, and fillers. The recipes for materials that have been evaluated or mass-produced to create rubber products amount to 88,000 types. Tomonori Furukawa of NOK R&D Material Engineering Department, Material Development Section 1, proudly highlights NOK's strengths: "Stable procurement of 5,500 types of raw materials, the capability to discover a wide range of functional raw materials, and the formulation expertise to understand and utilize the characteristics of these raw materials."
Please enlarge the screen to view
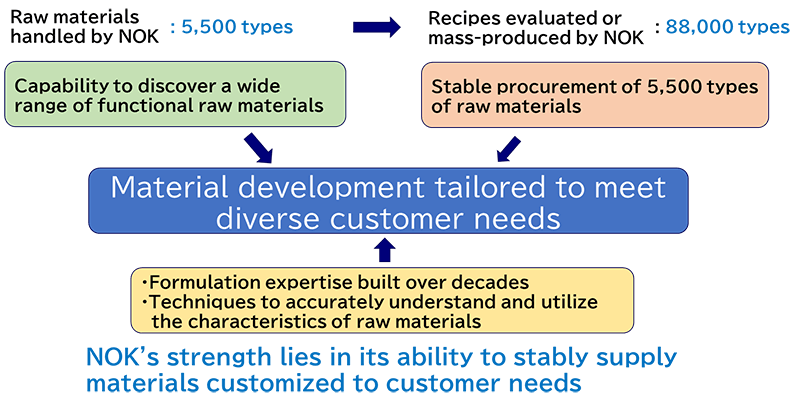
The number of material recipes continues to grow as customer needs diversify and the number of R&D personnel increases. Katsumi Abe from the Materials Technology Department notes that in the past five years, the number of recipes has been growing at a pace of 4,000 to 4,500 per year. Abe explains, "In recent years, the needs have become increasingly varied, and in addition to basic functionality, customers are seeking added features," highlighting the increasing complexity of research and development. A typical example is the low-friction product "Le-μ's," which fulfills the dual need for oil seals to maintain sealing functionality while reducing friction to support energy efficiency and fuel economy. As development becomes more challenging, the number of engineers in the Materials Technology Department has also increased.
Accelerating development is crucial
Material development at NOK begins with gathering customer product functionality requirements. First, materials that meet these needs are selected from those already in mass production. If a suitable recipe exists, it is adopted. If not, material development comes into play. The goal is to develop materials that meet the requirements, can be mass-produced, and maintain stable quality.
Please enlarge the screen to view
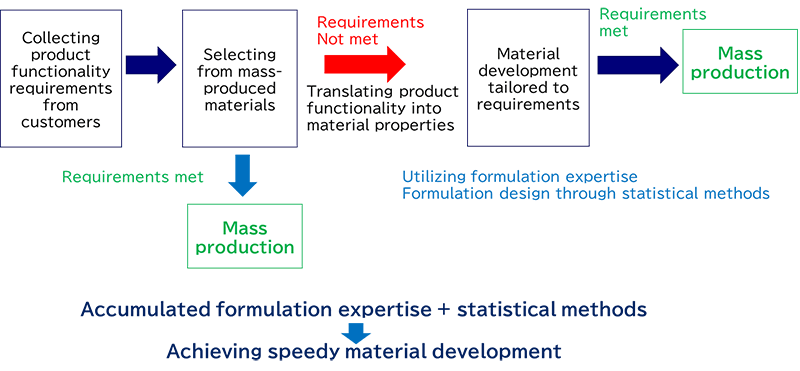
According to Furukawa, there are approximately 200 development projects per year, of which about 160 involve material development. Quick responses are essential, and while development was previously based on the experience of engineers, the introduction of statistical methods has significantly accelerated material development.
Statistical methods are designed to handle complex parameters (variables), reducing the number of experiments needed to determine optimal values to only the minimum required. For example, suppose that five different fillers with varying blending ratios should be used when developing low-friction oil seal materials. To calculate the optimal blending ratios that meet requirements like friction coefficient and hardness, selecting three blending ratios for each filler would require over 200 experiments (35 = 243 in a simple calculation). With statistical methods, the number of experiments can be reduced to 30. Since experiments typically take a long time, 200 experiments might require about a month, whereas statistical methods can shorten this to just five days. NOK utilizes analytical software to apply statistical methods. Engineers involved in material engineering study statistical methods daily, and every one of them possesses the analytical skills necessary for this approach.
Please enlarge the screen to view
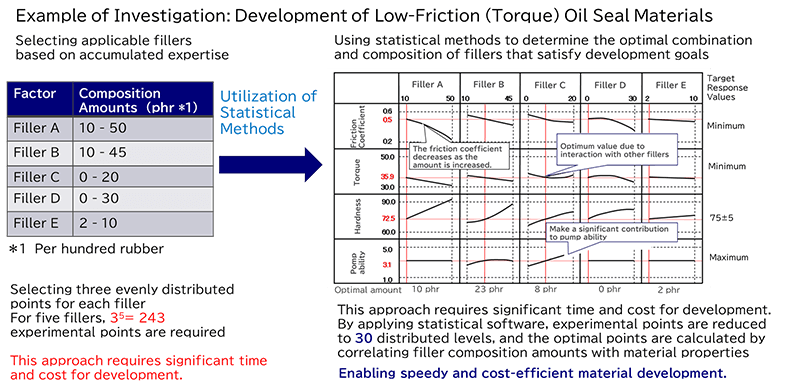
According to Abe, NOK promotes digital transformation (DX) in material development. Previously, some measurement results were managed on paper, but a system has been introduced to enable immediate data entry. Basic properties are already integrated into the data system, and plans are in place to allow for the immediate digitization of results such as friction coefficients, tensile strength, and compression set in the future. Looking ahead, Abe envisions a system where "conditions and requirements necessary for development can be entered, and the system suggests appropriate recipes." However, he acknowledges that full automation is challenging. "Considering factors such as mass producibility and ease of processing will likely remain tasks for engineers." The challenges faced by engineers in material development will continue into the future.
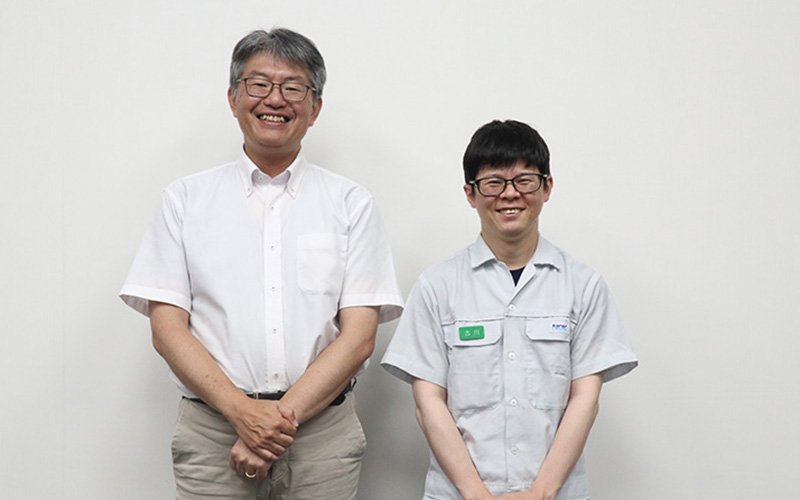
(Photo left)
Katsumi Abe
Department Manager, NOK R&D Material Engineering Department, NOK Corporation
After joining NOK, Katsumi Abe was involved in the formulation design of oil seals and the development of adhesives and surface treatment agents. In 2015, he was seconded to Thai NOK, where he managed various aspects of material management. He returned to the Materials Technology Department in 2018 and, since 2023, has been leading a team of 56 members as the department head.
(Photo right)
Tomonori Furukawa
Material Development Section 1, NOK R&D Material Engineering Department, NOK Corporation
Tomonori Furukawa joined NOK in 2008 and has been engaged in developing materials for oil seals. In 2016, he was seconded to NOK Elastomer, a compounding site, where he acquired skills related to mass-production compounding. He returned to NOK in 2018, working on developing materials for high-pressure hydrogen seals and electronic components. Since July 2023, he has been involved in tasks related to oil seals, gaskets, and marine-related products.
- Note:Data, positions, and titles in this article are current as of August 2023.