Making the Invisible Visible: Analytical Techniques for Visualization at the Molecular Scale
NOK's strength lies in its technological capability to produce rubber with a wide range of properties that meet various societal needs. At the core of this capability is our advanced analytical technology. By visualizing and understanding rubber structure at a molecular scale, NOK develops safe and reliable products.
Visualizing rubber structure through multifaceted analytical techniques
At NOK, rubber is analyzed from multiple perspectives using a variety of methods, including molecular structure analysis through nuclear magnetic resonance (NMR), surface nanostructure analysis through atomic force microscopy (AFM), and surface composition analysis through X-ray photoelectron spectroscopy (XPS). Kei Sekiguchi of the Materials Research Section, NOK R&D Technical Research Department, asserts: "Rubber analysis is an essential technology for ensuring safety and reliability." For example, analyzing defective products can help identify their causes, which can then be used to enhance product quality. As explained in the article "What Exactly Is Rubber?" rubber is comprised of polymer chains joined by cross-links. Its properties are determined by various factors, including the product's shape, the substances mixed into the rubber, and its structure at the molecular scale. Therefore, analysis need to be conducted across a wide range of scales, from millimeters to nanometers (a nanometer is one billionth of a meter). Takahiro Anzai of the Materials Research Section, NOK R&D Technical Research Department, states: "NOK has unique expertise in analytical technologies, which serves as a key strength."
Since 1960, NOK has been in a capital partnership with Germany's Freudenberg Group, fostering technological exchanges. For example, NOK and Freudenberg share insights into areas of expertise such as simulation techniques — Freudenberg's forte — and experimental methods, NOK's forte. By exchanging information and encouraging collaborations among personnel with expertise in various technical domains, both companies continue to refine their proprietary technologies.
Please enlarge the screen to view
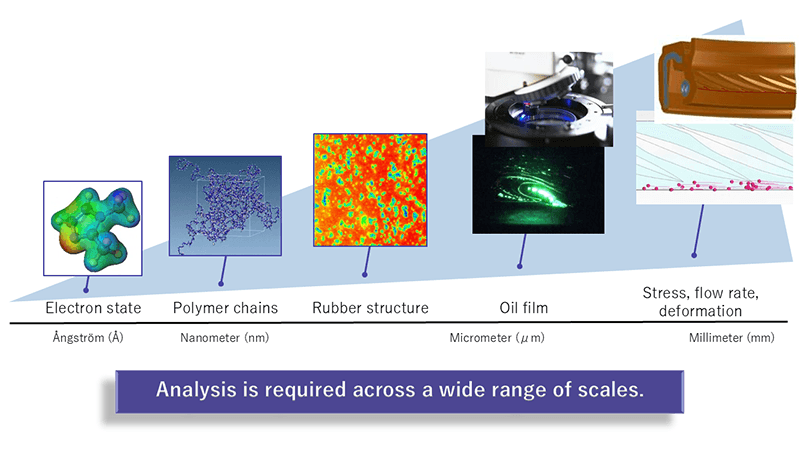
Evaluating performance through nanoscale-level analyses
At NOK, the structure of rubber materials is visualized on a nanoscale level to support material development. One example of this is a joint research project with Professor Ken Nakajima from the Tokyo Institute of Technology (current name: Institute of Science Tokyo), who is known for his studies on evaluating properties on the nanoscale level using AFM. According to Anzai, it has been understood for over a century that mixing carbon black into rubber enhances its strength and durability (the reinforcement effect). However, the mechanism behind this effect and how the structure of rubber changes can only be understood through nano-level analyses. Using a method developed by Professor Nakajima to measure mechanical properties (such as elasticity) on a nanoscale with AFM, it was confirmed that the interaction between polymer chains in the rubber and the carbon black creates a layer that contributes to the reinforcement effect.
Please enlarge the screen to view
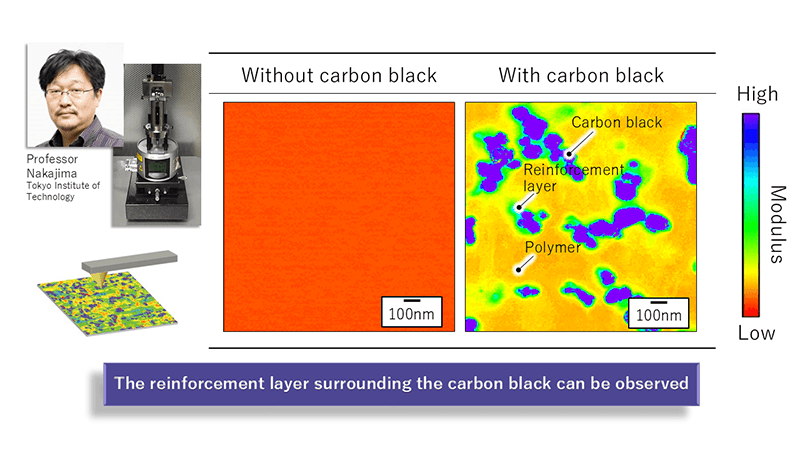
Please enlarge the screen to view
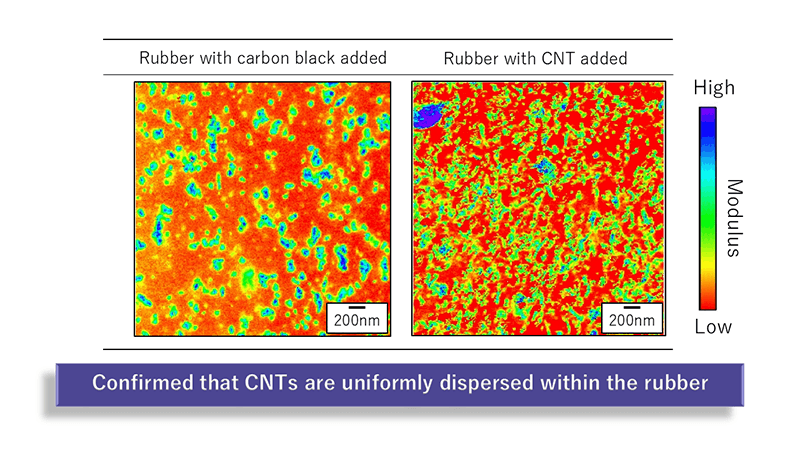
Responding to environmental regulations with trace quantitative analysis
At NOK's Shonan R&D Center in Fujisawa City, Kanagawa Prefecture, over 40 analytical devices are in operation, including AFM and XPS. According to Sekiguchi, various environmental regulations, such as the European Restriction of Hazardous Substances (RoHS) directive, have been introduced in recent years, making it essential to verify that regulated substances are not present in products. Some NOK products require the ability to measure content levels at the ppb (parts per billion) scale — one billionth of a unit.
Sekiguchi and Anzai emphasize: "Automotive-related products, which are an NOK specialty, are directly connected to human lives. We feel a strong sense of responsibility for ensuring their safety and reliability." To uphold safety and reliability, NOK will continue refining its analytical technologies.
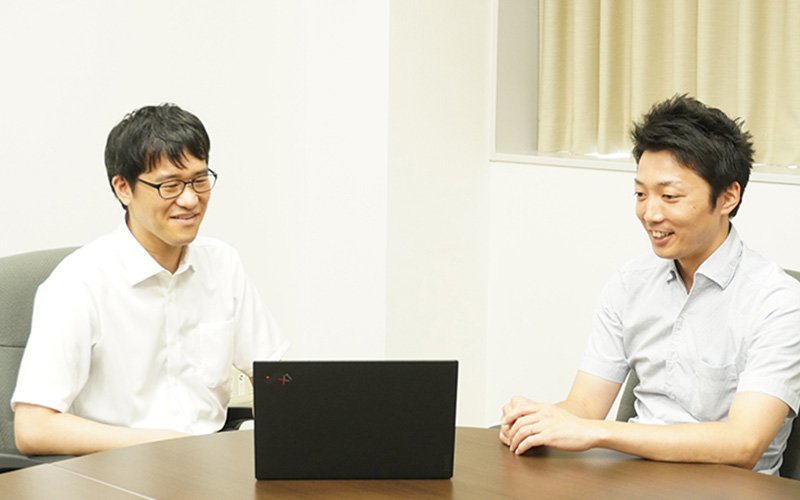
(Photo left)
Kei Sekiguchi
Supervisor, Materials Research Section, NOK R&D Technical Research Department, NOK Corporation
After joining NOK, Kei Sekiguchi was assigned to the Materials Technology Department, where he worked primarily on chemical analysis and developing and improving rubber materials for O-rings. In 2021, he transferred to the Technical Research Department. Since 2022, he has been the leader of the Analytical Research Group, handling analysis inquiries from both within and outside the company as well as developing new analytical methods.
(Photo right)
Takahiro Anzai
Materials Research Section, NOK R&D Technical Research Department, NOK Corporation
After joining NOK, Takahiro Anzi was responsible for analytical work and material development. From 2017, he worked on the development of materials for oil seals. Since 2019, he has been engaged in research on sealing technologies, including low friction. In 2022, he began collaborating with Professor Ken Nakajima of the Tokyo Institute of Technology (current name: Institute of Science Tokyo) on research related to controlling the physical properties of rubber.
- Note:Data, positions and titles in this article are current as of August 2023.