Providing the Right Products for Advanced Technologies: NOK's Response to Automotive Electrification
NOK's largest customer, the automotive industry, is experiencing what is often called a once-in-a-century transformation. The spread of advanced technologies such as CASE (Connected, Autonomous, Shared, Electric) and the global imperative to achieve carbon neutrality (net zero greenhouse gas emissions) are demanding significant adaptive measures from the automotive sector. To keep pace with these rapid changes and ensure its survival, NOK must focus on developing products tailored to these themes.
Developing optimal products for e-mobility
Oil seals, a key product for NOK, are already widely used in engines. However, with the impending bans on gasoline vehicle sales in regions such as Europe, the U.S. and China — and their replacement with electric vehicles (EVs) and hybrid vehicles (HVs) — the development of products that support e-mobility has become a major challenge for NOK.
At NOK’s R&D hub, the Shonan R&D Center, research and development efforts are underway to create products for e-mobility.
According to Akihiro Suzuki, section manager of Material Development Section 2 in the NOK R&D Materials Technology Department, unlike internal combustion engine vehicles, e-mobility uses electricity to power motors. That increases the number of components such as batteries, motors and power conversion units. While oil seals for engines have historically required heat and oil resistance, Suzuki notes that e-mobility demands greater resistance to water and dust. "Moreover, as the number of electronic control units (ECUs) and other electric circuits increases in e-mobility, materials such as silicon-based low-molecular-weight siloxanes, which could lead to contact failure, cannot be used. Instead, ethylene propylene diene monomer (EPDM) rubber, which offers excellent water resistance, is a practical material," he explains. EPDM is already increasingly adopted for gaskets (seals used in fixed components) for ECU covers.
Please enlarge the screen to view
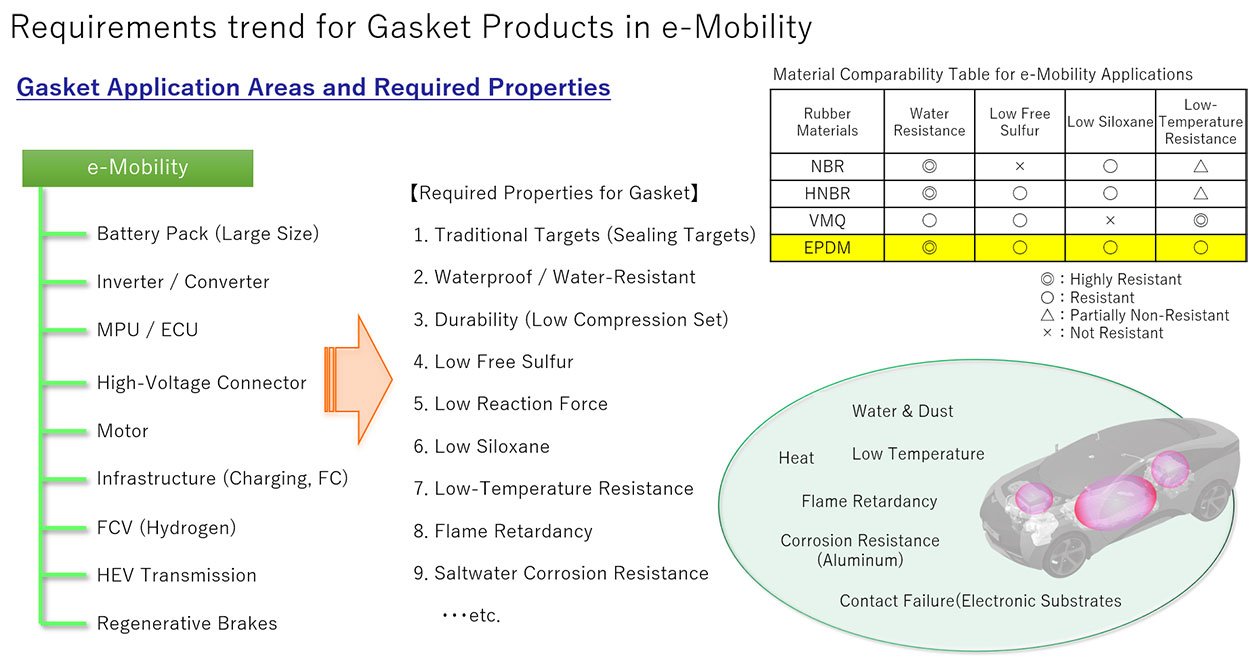
Leveraging expertise to meet new demands
Seals for lithium-ion battery (LiB) electrolytes are currently under intensive research and development within the realm of oil seal technology. These seals must maintain the electrolyte's performance while preventing corrosion of the electrodes. While EPDM is a suitable material, it is necessary to address the issue of surface degradation (referred to as "surface roughening"). To resolve this, NOK is looking to commercialize "e-mobility EPDM," an enhanced version of EPDM achieved through advanced compounding techniques.
E-mobility systems also require the integration of numerous electrical circuits within confined spaces. In such cases, there is an anticipated demand for seal materials with added thermal dissipation capabilities to handle the heat generated by electrical circuits. Furthermore, communication devices and sensors — essential for CASE applications — are becoming increasingly common. Suzuki states, "To stabilize communication environments, it is crucial to incorporate conductive properties into the seals to block specific frequencies." By adding conductivity through fillers, electromagnetic waves can be effectively shielded. This approach increases the number of materials requiring consideration compared to those for conventional engine vehicles.
The development of new fields extends beyond the automotive industry. For example, NOK is also researching O-rings used to seal refrigerants and refrigeration oils in air-conditioning systems commonly found in households.
These O-rings are designed to seal systems with wide temperature fluctuations, ranging from -40°C to 120°C. Refrigerants, which transfer heat through state changes between liquid and gas, also require seals that suppress foaming within the rubber. This is because refrigerants dissolved in the rubber can rapidly change into gas when heated, potentially damaging the rubber due to sudden volume expansion. Low-temperature HNBR, a hydrogenated nitrile rubber with enhanced low-temperature resistance, is the current choice. As refrigerants evolve, however, new materials will also be necessary. For instance, alternatives like R32, which have lower greenhouse gas emissions and are less harmful to the ozone layer, are now in use. Looking ahead, environmentally friendly natural refrigerants are expected to become the norm, prompting NOK to accelerate its research on seal materials compatible with carbon dioxide (CO2) refrigerants.
NOK is also committed to delivering reliable products for water supply applications. Resistance to chlorine and the heat resistance required for water heaters are essential, alongside growing demands for long-lasting performance.
Please enlarge the screen to view
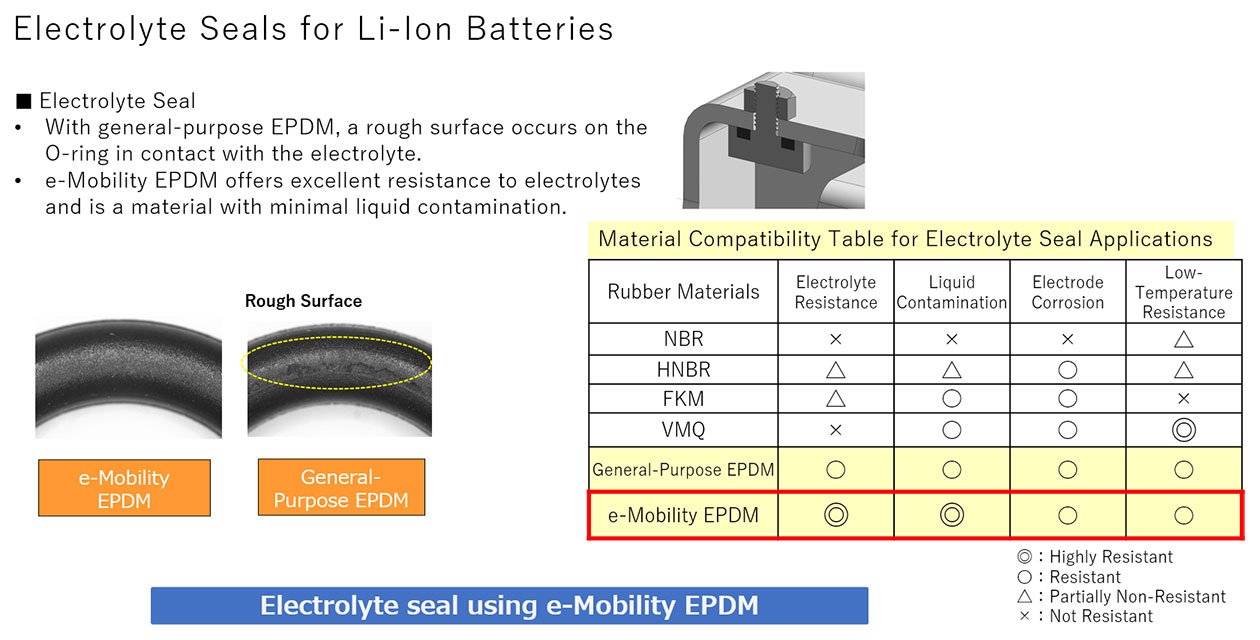
Please enlarge the screen to view
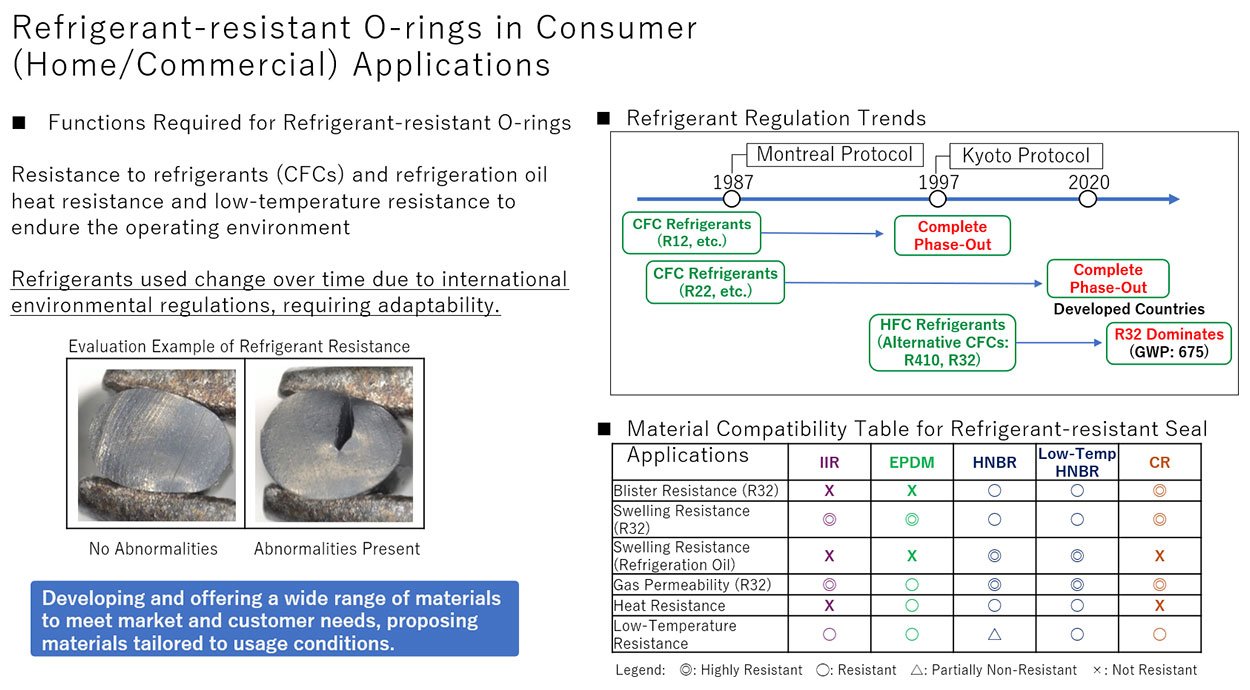
Developing e-mobility products for the future
Since 2020, Material Development Division 2, led by Suzuki, has focused on research and development for e-mobility-related products. While Division 1 primarily handles oil seals for conventional engine vehicles and drive systems also used in EVs, Division 2, comprised mainly of younger employees, continues its R&D efforts with a team of around 10 people. Suzuki notes a growing demand for environmentally friendly materials such as biomass that align with life cycle assessment (LCA) principles. "The requirements are becoming increasingly challenging, and the number of projects is also rising," he explains.
Although developing new functionalities for oil seals has become increasingly difficult after years of ongoing research, Suzuki remains determined and ambitious. "We plan to actively incorporate new technologies and collaborate closely with onsite teams to drive product development forward."
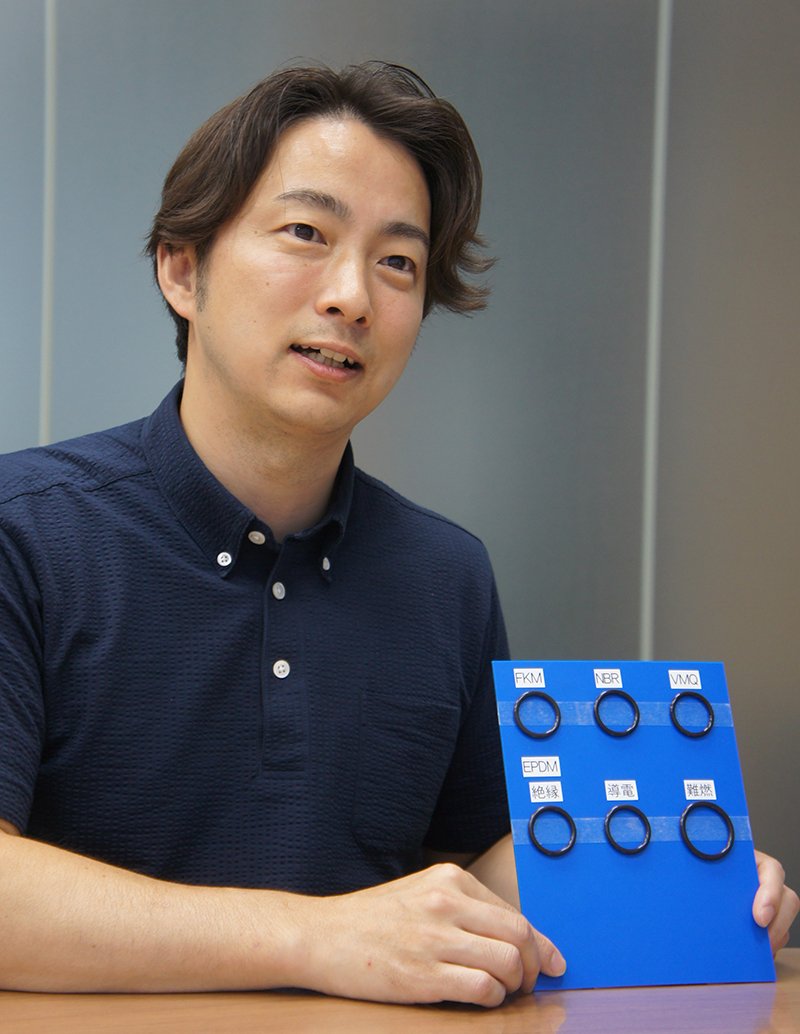
Akihiro Suzuki
Section Manager, Material Development Section 2, NOK R&D Materials Engineering Department, NOK Corporation
After joining NOK, Akihiro Suzuki worked on analysis operations and surface treatment technology development. From 2014, he was involved in the development of materials for anti-vibration rubber, and from 2016 focused on cell seal materials and new product material development. In 2023, he became the manager of Material Development Division 2, focusing primarily on materials for e-mobility and environmentally friendly materials.
- Note:Data, positions and titles in this article are current as of June 2023.