Applying Seal Technology to Meet Needs: Supporting Automobiles with NOK
Japan's first oil seal manufacturer, NOK provides high-performance, high-quality products to a wide range of industries, including automotive, construction machinery, agricultural machinery and electronics. Oil seals are used in engines, gears and other components that perform repetitive rotational or reciprocating motions. Their role is to prevent oil, liquids and gases from leaking while ensuring smooth rotational and reciprocating movement. Since decarbonization has become a critical theme for the automotive industry and other sectors, oil seals are also required to achieve higher performance than ever before. Leveraging its long-standing technical expertise, NOK is advancing research and development to ensure every oil seal has optimal functionality.
Automotive oil seals: Around 80,000 types of materials*3
NOK oil seals are most widely used in the automotive sector. They are applied to numerous components, such as engine seals that prevent engine oil leakage, differential gears essential for vehicle movement, suspensions, and hub bearings that connect tire wheels and axles.
When people hear "oil seal," many may think of a ring-shaped component made of rubber*1. However, various shapes and diverse rubber materials are used for oil seals depending on the product. NOK has registered approximately 80,000 types of rubber compounds, for example. According to Yasuaki Kitajima, section manager of the Material Administrative Section in the NOK R&D Material Engineering Department: "The number of rubber candidates considered during product development ranges from several thousand to tens of thousands." The best-suited rubber is selected based on performance, cost and other factors.
Selecting materials based on required performance and cost
How is the rubber for oil seals selected? Kitajima explains: "We start with a base rubber determined by our past knowledge and then adjust the materials to compensate for any performance deficiencies using specific raw materials*2. Rubber's raw materials are mostly polymers, with reinforcing agents such as silica or carbon, vulcanizing agents, anti-aging agents, and performance-enhancing additives added to achieve the desired shape and performance. Since polymers play a primary role in functionality, deciding which polymer to use is crucial."
There are numerous types of rubber materials. The selection process involves evaluating the conditions the rubber will face, such as whether it will be exposed to heat (heat resistance), how much rotational or reciprocating motion it must endure (wear resistance), the intensity of deformation or force it must withstand (mechanical strength), exposure to sunlight or rain (weather resistance), and whether it needs to maintain its function in low-temperature environments (cold resistance). Cost is also a key consideration, and the rubber with the best balance of these factors is chosen.
For example, in the case of engine seals used on the rotating shafts of high-speed engines, fluoroelastomer (FKM) is often selected. FKM withstands the high temperatures of the engine and remains stable, even when sealing engine oil. Although FKM is expensive, it is the optimal material for engine seals, capable of lasting up to 100,000 kilometers.
Please enlarge the screen to view
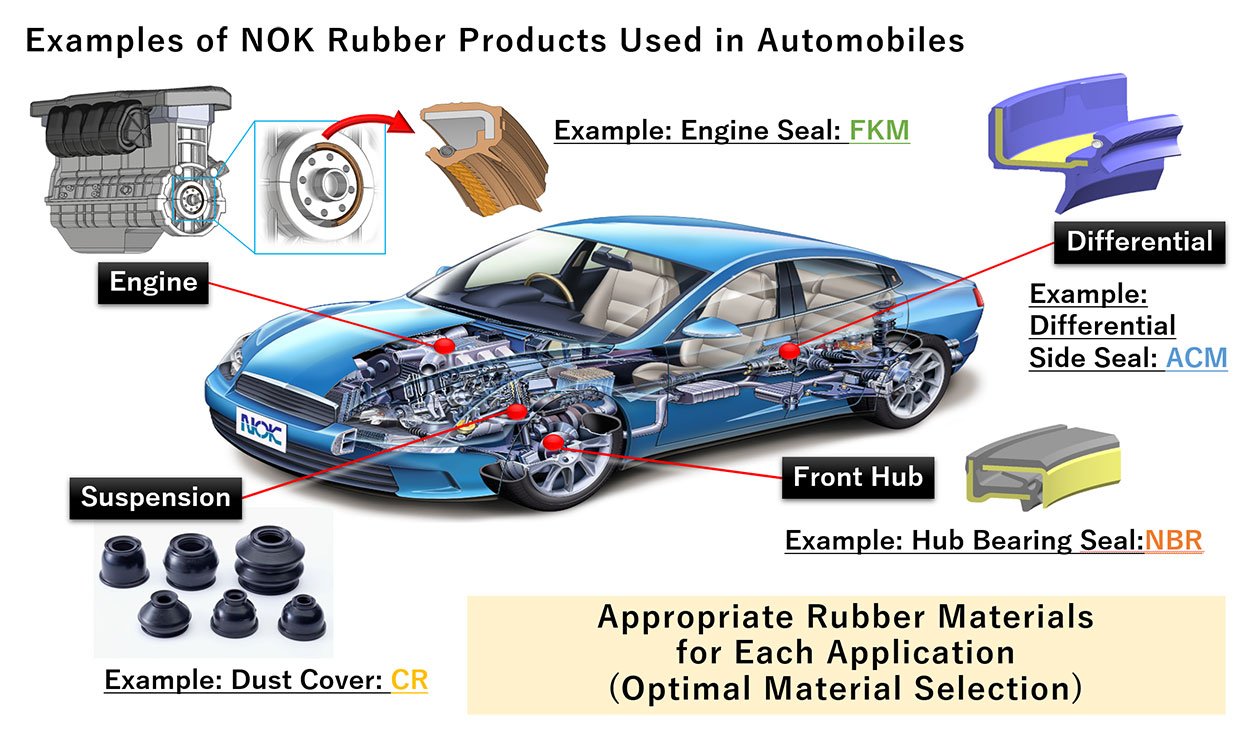
On the other hand, nitrile rubber (NBR) is the most commonly used material for hub bearing seals. NBR offers excellent cost performance and a good balance of cold and wear resistance. However, its weakness lies in low heat resistance, making it unsuitable for environments exceeding 100°C. In other words, it cannot be used near heat sources but is well-suited for locations exposed to dirt and dust. Protecting the bearings from dirt and dust is the highest priority for hub bearing seals. “Using other materials would lead to over-specification,” Kitajima says. Chloroprene rubber (CR) is ideal for dust covers that protect suspension components from dirt and dust. Although CR also has low heat resistance, it excels in adaptability — maintaining its shape under repeated forces — and in fatigue flex resistance, which prevents damage even after repeated bending.
Tuning to meet advancing demands with precision
Kitajima notes: "There is no universal material with all the desired properties." The most suitable material is selected, considering strengths, weaknesses and cost. In some cases, blending different materials or altering additives improves performance, but such changes often involve trial and error to understand their impact on other properties. This process is referred to as "tuning," which traditionally requires significant expertise. NOK is working hard to streamline tuning by building a comprehensive database of procedures and refining usability.
Tuning must also consider cost. It is crucial to continue using existing mass-production facilities, adding complexity to the process. Moreover, users increasingly demand contributions to fuel efficiency, emphasizing low-friction requirements for oil seals to ensure smooth rotational and reciprocal movements. Proactive R&D efforts addressing future challenges are becoming more crucial, presenting Kitajima's team with exciting and rewarding opportunities to tackle impactful themes.
Notes:
- Material: Refers to rubber as a specific category among classifications such as rubber, plastic and metal.
- Raw materials: Rubber components.
- Compound: A combination of raw materials.
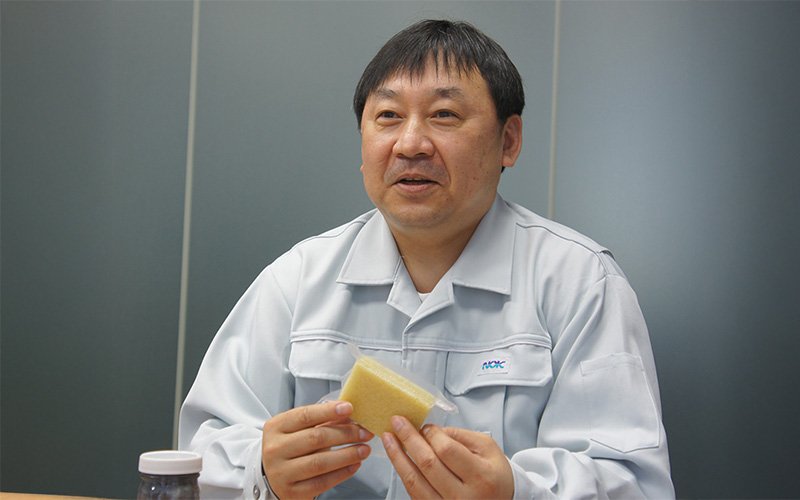
Yasuaki Kitajima
Section Manager, Material Administrative Section, NOK R&D Material Engineering Department
After joining NOK, Yasuaki Kitajima initially focused on analytical work. In 2000, he transferred to the Material Engineering Department, where he was involved in developing adhesives and surface treatment agents. In 2011, he moved to the Process Engineering Department in the Oil Seal Division, where he worked on improving issues and supporting launches of materials and adhesives. He returned to the Materials Engineering Department in 2017, and has been in his current role since 2019.
- Note:Data, positions and titles in this article are current as of June 2023.