The Foundation of Oil Seals: Dual Mechanisms for Lubrication and Sealing
Oil seals are designed to prevent leakage of oils, liquids and gases while also providing lubrication that ensures the smooth motion of components like rotating shafts and pistons, as well as low friction. Oil seals used in automobile engines and motors are also built to last for 10 years or 100,000 kilometers without replacement. But how do they maintain seal integrity, preventing the leakage of oil and ther fluids through the gap between roating or reciprocating components and the seal, while also sustaining low friction over time? It might seem almost too convenient, but the secret lies in the coexistence of two mechanisms: lubrication, which enables low friction, and sealing, which prevents leakage. This article will explain these mechanisms in detail.
The lubrication mechanism
First, it is essential to understand the structure of an oil seal. A typical oil seal used in engines or motors is composed of a metal ring that maintains a fixed position even under the forces of rotation and reciprocating motion, a spring that presses the seal tightly against the shaft or other components, and a rubber "lip" that provides the actual seal. The part of the seal that comes into contact with the rotating or reciprocating component is called the "lip." Oil seals feature a primary lip to prevent oil or other fluids from leaking and a dust lip to keep dust and debris from entering. To minimize contact with the rotating or reciprocating component at the sliding lips, the lips are designed with a narrow, pointed shape.
Please enlarge the screen to view
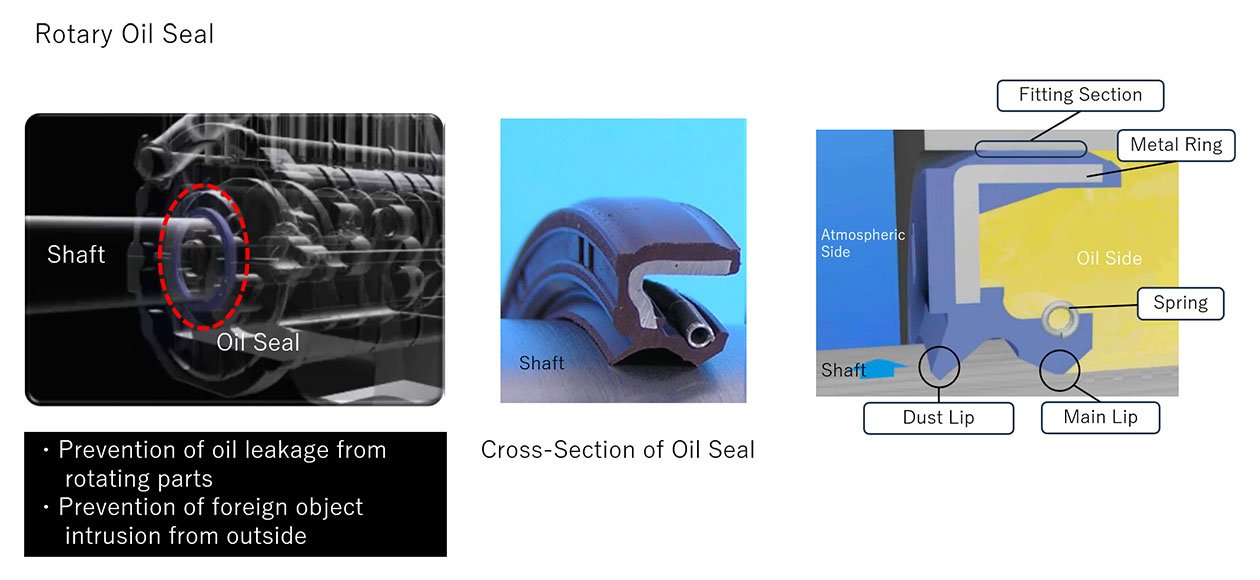
When it comes to rotary oil seals, a film of oil or other liquid forms between the lip and the rotating shaft as the shaft begins to rotate. According to Hiroyuki Sato, section manager of the Sealing Research Section in the NOK R&D Engineering Research Department, this phenomenon is called fluid lubrication. It is based on the theory that when liquid flows, it generates a force that pushes gaps wider. Incidentally, the widening force ceases when the rotation stops, and the liquid film gradually disappears due to the lip's tightening force.
The liquid film formed between the lip and the rotating shaft is just a few micrometers (one micrometer equals one-millionth of a meter) thick, and helps prevent wear. NOK was the first in the world to successfully visualize the flow of oil on the seal's sliding surface and its surroundings. This visualization has become a key element in understanding the lubrication mechanism.
What is the sealing mechanism?
The secret to preventing liquid leakage lies in the asymmetric pressure difference between the inside and outside of the lip. This is easier to understand when looking at a cross-sectional view. The lip's angle differs on each side, and the pressure spring is positioned closer to the sealing target. According to Dr. Ayako Aoyagi, assistant section manager of the Sealing Research Section in the NOK R&D Engineering Research Department, this pressure distribution at the sliding surface enables a pumping action that pulls liquid from the outside to the inside.
In addition, microscopic protrusions at the tip of the lip, visible only under a microscope, regulate the pumping action by circulating the liquid on the sliding surface, maintaining an appropriate film thickness. ""If too much liquid circulates, resistance from the flowing liquid increases friction. Conversely, if there is too little liquid, the rubber and shaft make contact, increasing friction,"" Sato explains. ""Controlling the film thickness is key to reducing friction."
These microscopic protrusions have a shallow angle on the external (atmospheric) side and a steeper angle on the internal (liquid) side resulting from the pressure distribution. This design enhances the pumping action, preventing liquid from leaking to the outside. In experiments, oil dripped onto the shaft from the external side using a pipette during rotation can be seen being drawn inward.
Please enlarge the screen to view
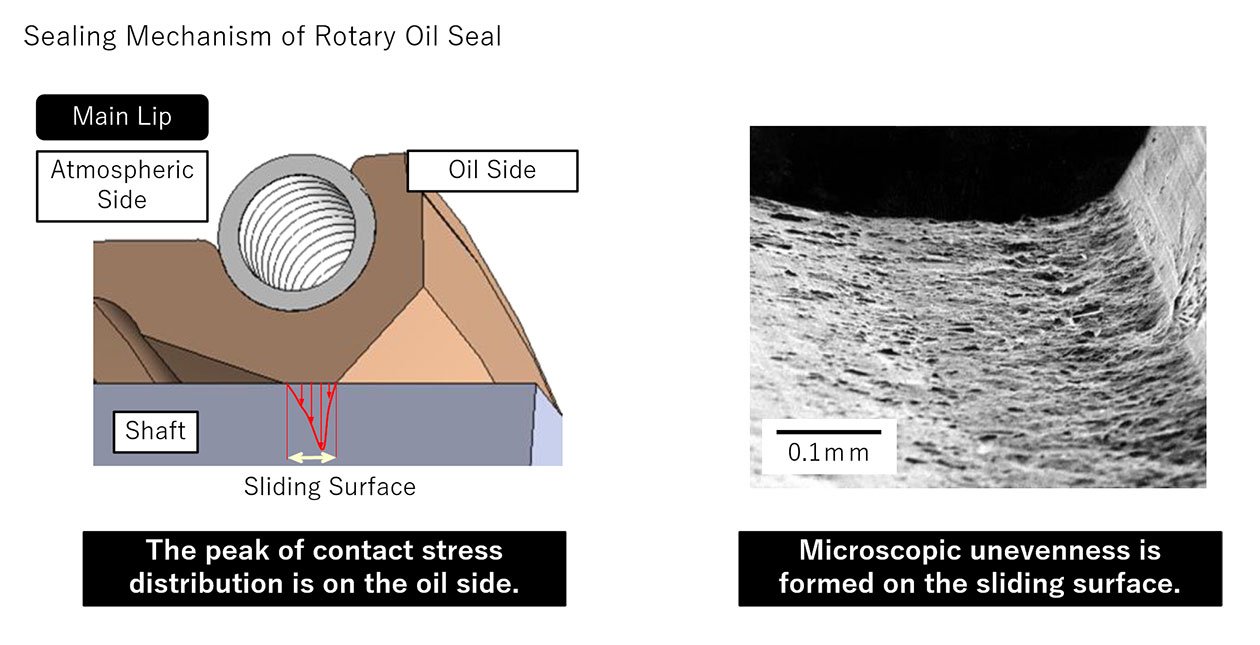
Please enlarge the screen to view
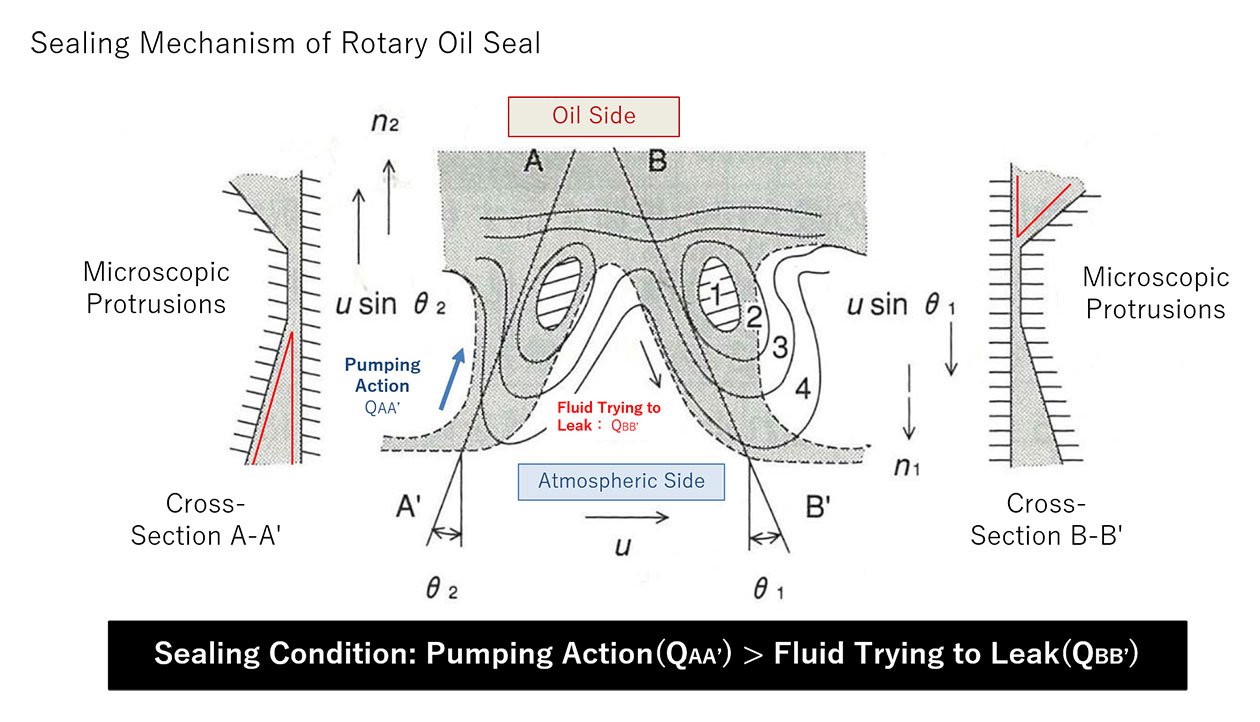
Enhancing pumping action with hull-shaped projections
There are also innovations in lip design. Keel-shaped helix projections have been incorporated into lip designs, while screw-shaped projections that align with the rotational direction of the shaft have been used for a long time. This allows the lip to maintain some level of pumping action even after wear. NOK pioneered this technique in the 1990s.
Another approach has been pursued in recent years: reducing wear by combining rubber materials and coatings. Our "TF Coat," developed in 2006, successfully reduced torque friction by 30% compared to conventional products. The continuing evolution of surface functional design technology will remain essential to improving the performance of oil seals.
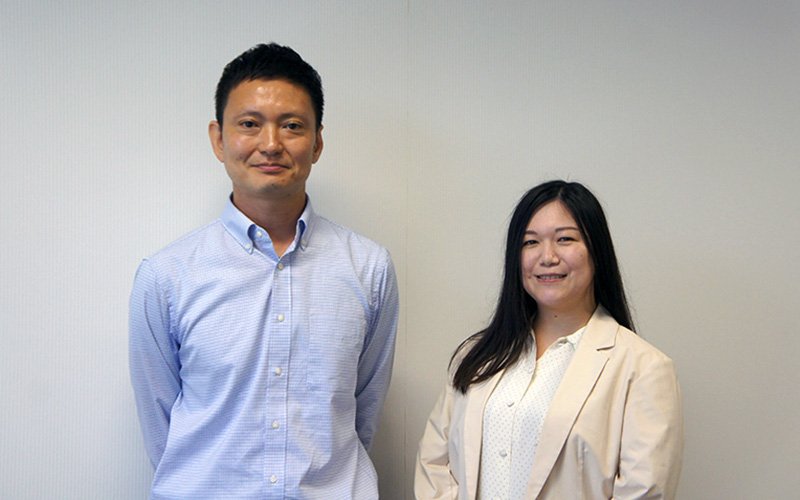
(Photo Left)
Hiroyuki Sato
Section Manager, Sealing Research Section, NOK R&D Engineering Research Department, NOK Corporation
After joining NOK, Hiroyuki Sato was responsible for the product design of rotary oil seals for general industrial machinery and reciprocating oil seals for automobiles. From 2005, he worked at the Shonan Development Center on technical development for various seal products. He was later involved in developing rubber rollers for office equipment at the Group company Synztec. He returned to the technical development of seal products in 2016 and, since 2021, has been engaged in research related to seal technologies, including low friction.
(Photo Right)
Ayako Aoyagi
Assistant Section Manager, Sealing Research Section, NOK R&D Engineering Research Department, NOK Corporation
Dr. Ayako Aoyagi specialized in polymer science in graduate school. After joining NOK, she worked on developing rubber materials for seals, such as O-rings, and performed chemical analyses. During her career, she took two maternity and childcare leaves, and in 2019 began researching oil seals. In October of the same year, she enrolled in the adult doctoral program at Kyushu University, researching rubber's lubrication mechanisms. She earned her Ph.D. in 2023. She is now engaged in research on seals for new environments, such as hydrogen and low-lubrication conditions.
About the Shonan R&D Center (Fujisawa City, Kanagawa Prefecture)
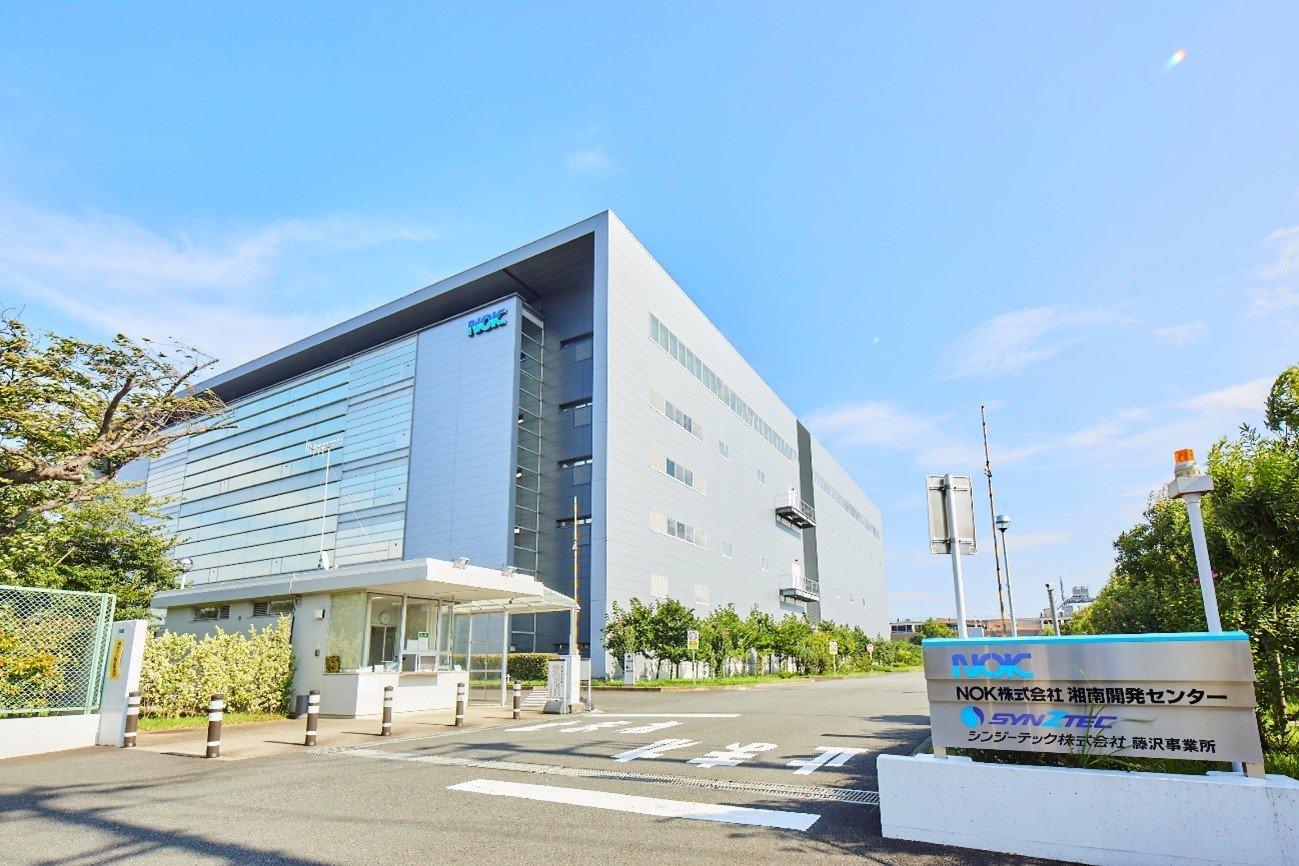
Established in 2005 as the core of NOK Group's technology research and development, the Shonan R&D Center responds swiftly to the accelerating transformation in mobility and global environmental changes. The center integrates strategic planning, research, product development, material development and process development for mass production. This cross-functional structure allows for flexible collaborations across departments as needed. By leveraging NOK’s proprietary technologies, the center addresses societal challenges and promotes solution-driven business models that contribute to product development and problem-solving.
- Note:Data, positions and titles in this article are current as of June 2023.