Evolving Beyond Engine Applications: Oil Seals and Shape Design Technology
Oil seals — one of NOK's core products — vary significantly in shape, materials and structure depending on what is being sealed, the size of the shaft they are mounted on, and the type of movement involved. NOK produces around 60,000 types of oil seals, most of which are specifically designed for particular applications. While oil seals are widely used in automobiles, those used for engines and those installed in drivetrain components require entirely different properties. Despite all being referred to as "oil seals," they are fundamentally distinct products. For example, oil seals used in hub bearings near the wheels have undergone their own unique evolution.
Maintaining functionality in harsh environments
The development of oil seals generally involves technical approaches involving surface functional design, material design, and shape design. Shape design technology examines the structure of the oil seal and the shape of its sliding surface. One area where shape design technology has driven dramatic advancements, particularly to reduce torque, is in hub bearing oil seals.
Hub bearings connect a vehicle's body to its wheels and are located near them. They enable smooth wheel rotation while keeping the wheels securely attached to the vehicle, ensuring a smooth driving experience. Since hub bearings rotate along with the wheels, they are lubricated by grease. Hub bearing oil seals are required to prevent this grease from leaking out, and also stop mud, water and dust from entering the hub.
Oil seals for engines are mounted on rotating shafts that spin between 1,000 and 8,000 revolutions per minute (rpm). In contrast, hub bearings rotate at speeds of up to 2,000 rpm. Hub units have limited space for seals, however, and are exposed to harsher environments than the engine, which is located within the vehicle body.
According to Kazuki Hirota, assistant section manager of AI Design Section 3 in the Oil Seal Division at NOK’s Fukushima Plant, the design of hub bearing oil seals has undergone significant changes since the 1990s, when they began to be widely adopted. These changes aimed to reduce torque and lower production costs.
Examining the design changes over time, before 1990, a "dust lip" (wedge-shaped protrusion) was added to the parts of oil seals that came into contact with the wheel's rotating shaft. This addressed the increasingly severe environmental conditions for vehicle undercarriages, such as off-road driving. By 2000, two dust-lips were incorporated, followed by the mass production of side-lip designs in which the lips were oriented nearly parallel to the shaft. This maintained seal integrity while reducing torque. In the 2010s, multiple lips were converted to side-lip designs and thinner lips were developed after structural analysis and various experimental evaluations. This achieved the dual goals of maintaining functionality and reducing production costs.
Please enlarge the screen to view
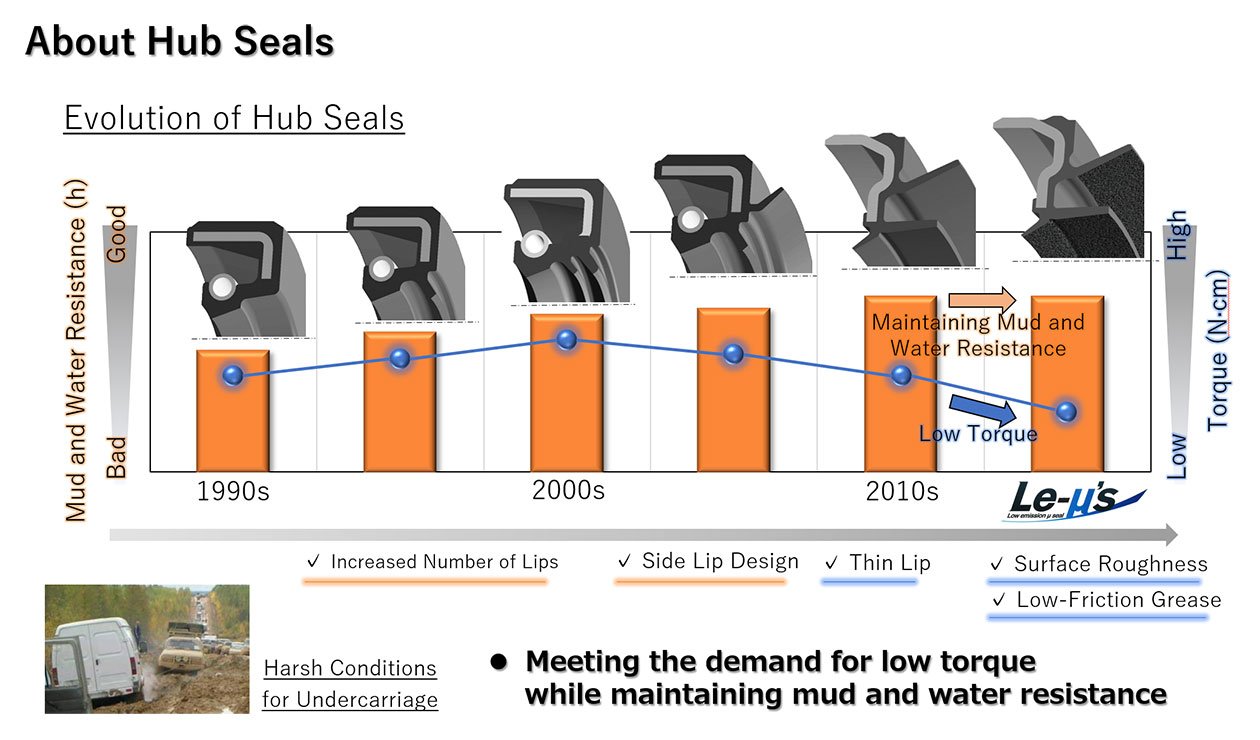
Please enlarge the screen to view
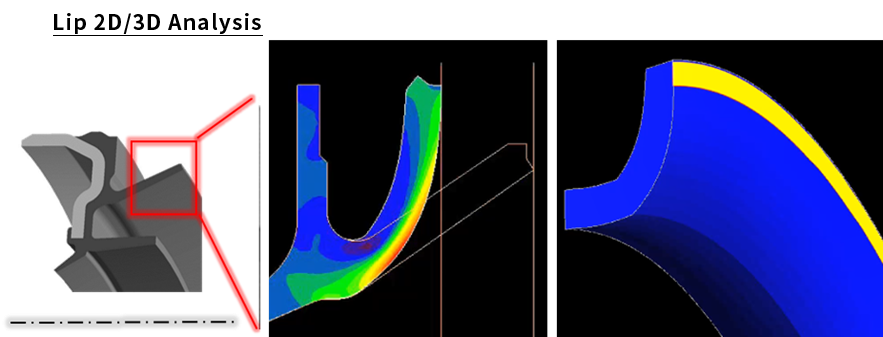
Using grease and surface texture for reduced torque
Structural modifications alone are no longer sufficient to further reduce torque. To address this, a textured surface known as "pear-skin texture" was applied to one side of the lip, creating random, fine irregularities with a roughness of less than 20 micrometers (twenty millionths of a meter). A proprietary low-viscosity grease was also adopted for the sliding surface of the lip, forming a rich grease film. This combination reduced torque by over 30% compared to conventional products. The pairing of the pear-skin texture and low-torque grease was branded as the "Le-μ's" series, which has been proposed to automakers and Tier 1 suppliers. Numerous manufacturers have already adopted it.
Hirota explains the challenges of shape design: "Even if the shape of the lip is determined through theoretical analysis, the actual lifespan doesn't always align with expectations." Since the shape of the Le-μ's design varies depending on the specific vehicle in which it is used, further refinement will be necessary.
Please enlarge the screen to view
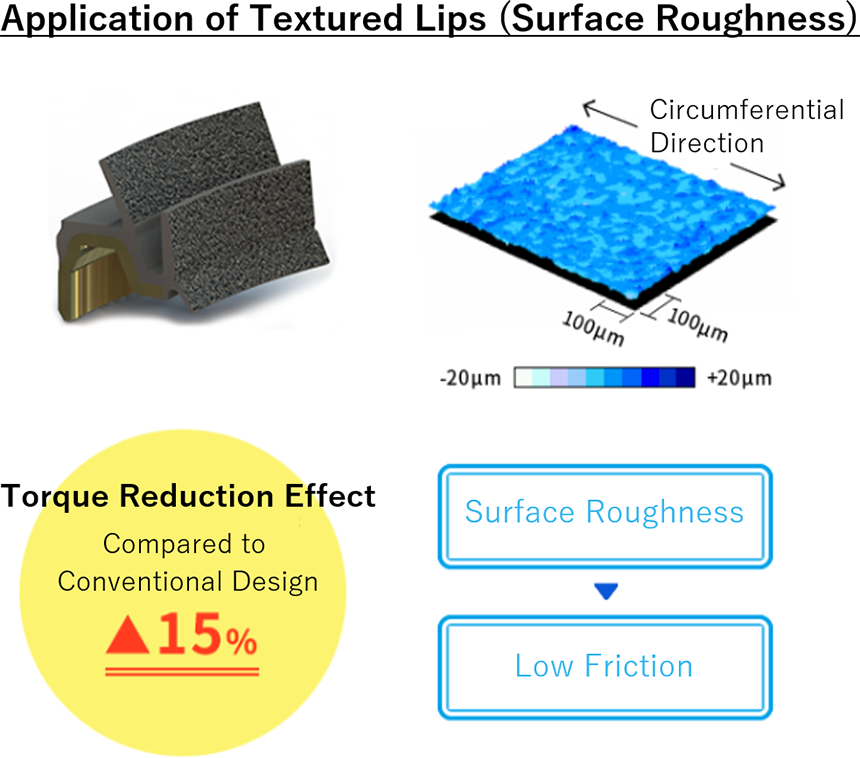
Please enlarge the screen to view
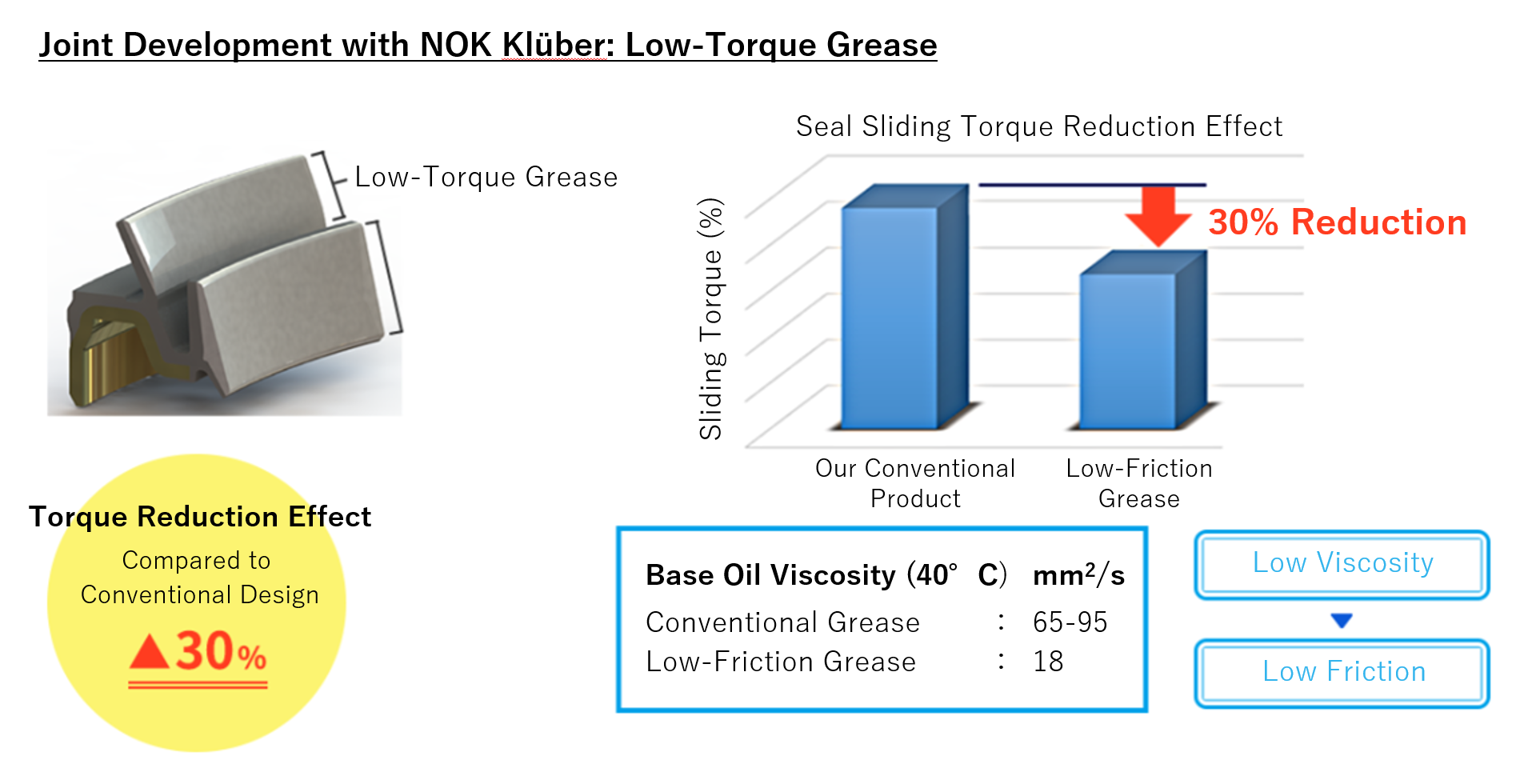
Enhanced functionality in the era of electrification
How will hub bearing oil seals evolve? Hirota emphasizes that adapting to electrification is essential. Hub bearings will continue to be used in electric vehicles (EVs) and are expected to play an even greater role in improving energy efficiency. In internal combustion engine (ICE) vehicles, energy loss occurs within the engine itself, but this loss disappears in EVs. As a result, the proportion of total vehicle energy loss attributed to hub bearing friction increases, making further torque reduction more crucial than ever.
But is further evolution even possible? Hirota reveals: "Although still in the development phase, we are on track to create products that reduce torque by several dozen percent. These new products align with the low-torque requirements of Tier 1 suppliers, and promotional efforts are gradually advancing." To solidify their position in the era of EVs, though, Hirota mentions an ambitious goal: "First, we aim to cut torque in half — and ultimately, to achieve zero."
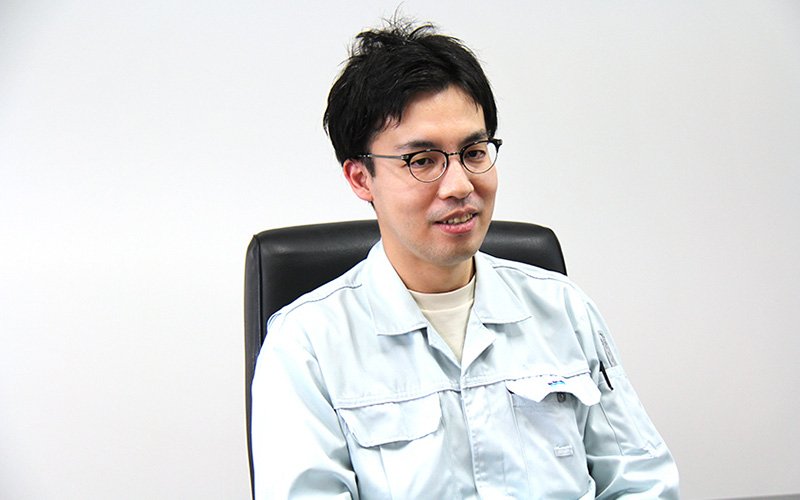
Kazuki Hirota
NOK Corporation, Oil Seal Division, Design Department, AI Design Section 3
After working at a parts manufacturer, Hirota joined NOK and was assigned to AI Design Section 3. Initially, he was responsible for experimental work on automotive mud seals used in intermediate shafts and coupling components. Since 2018, however, he has engaged in product design and experimental work on hub seals. In 2021, he was promoted to assistant section manager of AI Design Section 3, focusing on developing hub seals and promoting the Le-μ's (pear-skin texture × low-torque grease) series.
- Note:Data, positions and titles in this article are current as of February 2023.