Using Trial and Error to Find the Perfect Blend: Oil Seals and Material Design Technology
Oil seals are one of NOK's core products. Of NOK's consolidated sales of 682.5 billion yen for the fiscal year ending March 2022, the sealing business — including oil seals — accounted for approximately 336.2 billion yen, or nearly 50%. NOK produces 60,000 types of oil seals globally, manufacturing 1.83 billion units annually. Despite their seemingly simple ring-like design, oil seals combine rubber material, metal rings, and springs to prevent oil and water leakage, achieve low friction, and ensure durability. They are essential mechanical products for all types of machinery, and one of the supporting technologies is material design.
Matching characteristics to functional requirements
For oil seals used in rotating bodies, the primary development focus is on low-torque materials that reduce friction energy at the contact surface between the seal and rotating body. Of course, maintaining seal integrity is essential and cannot be compromised. According to manager Hiroki Matsui of the Design Department in the Oil Seal Division at the Fukushima Plant — NOK's main production plant for oil seals: "The shape and materials of oil seals vary depending on the composition of the oil being sealed and the performance of the rotating body, which means nearly every product requires a unique development process."
The main development approaches include surface functional design, material design, and shape design. Material design in particular involves altering the rubber material composition to enhance performance. According to Suguru Yoshida, section manager of Material Technology Section 4 in the Materials Technology Department at the Fukushima Plant, the "low-torque seal material" the company first marketed in 2008 reduced torque by approximately 20% compared to conventional products at the time. It retains its low-torque qualities even if the coating on the contact surface (sliding surface) with the rotating shaft wears down. This material has already been adopted by three Japanese automakers.
While developing low-torque seal materials, attention was focused on the microbubbles (cavities) that form on the sliding surface of the oil seal when the rotating shaft begins to move. These bubbles come from the fine oil between the oil seal and the rotating shaft due to pressure differences generated during rotation. It was discovered that producing more evenly distributed bubbles helps reduce torque friction.
Please enlarge the screen to view
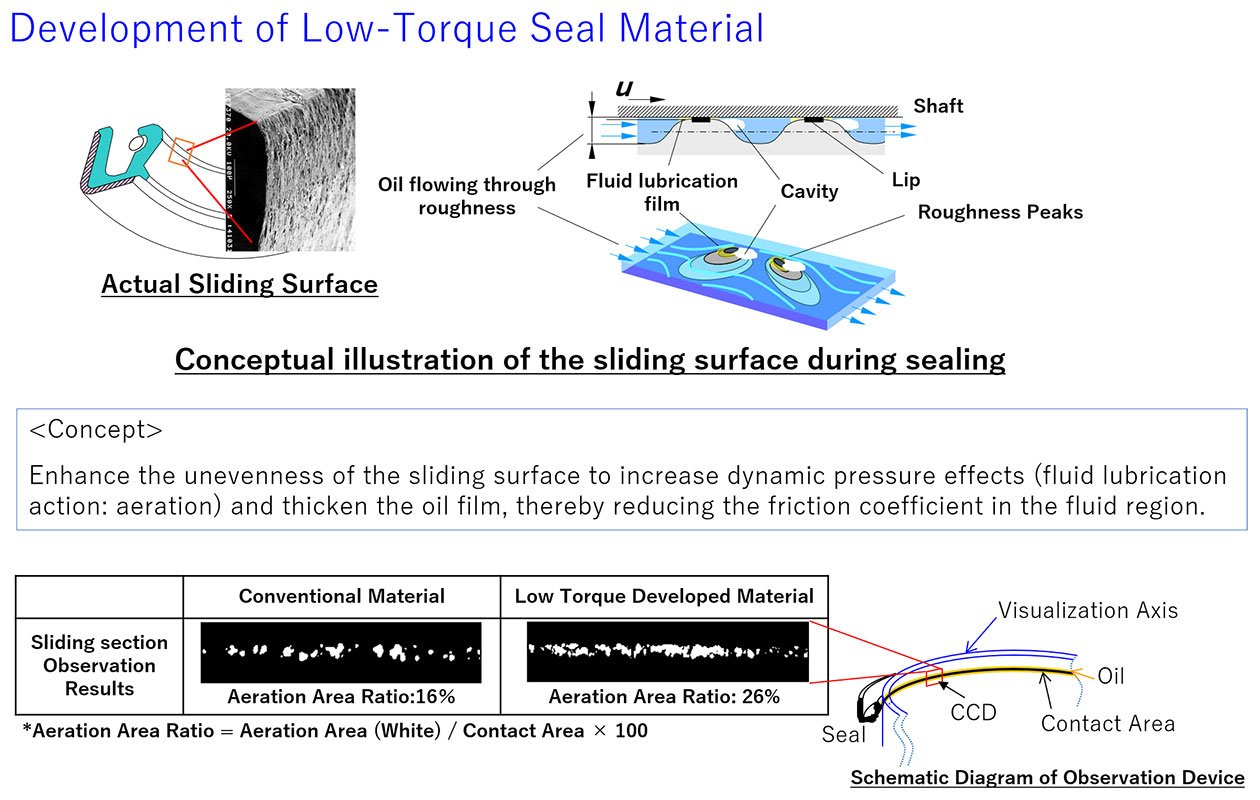
The challenges of mass production
Yoshida notes that there were several challenges during the development phase. One fundamental difficulty was determining the material composition needed to create the microscopic irregularities on the sliding surface — the proportion of fillers in the material had to be increased to generate more bubbles. However, oil seals used in engines must also maintain heat resistance and sealing capability, so compromising these capabilities would render the product unusable. Boosting the filler content also reduces the softness of the rubber material. Through repeated trial and error, the team pushed the filler ratio to its limit, ultimately increasing the bubble area on the sliding surface by 10% compared to conventional products.
Mass production presented even more significant difficulties. For example, while new materials could be tested in devices with a capacity of several liters during research and development, mass production required devices with capacities more than ten times greater. "When scaling up, issues such as when the material doesn't mold properly can arise, and we sometimes have to start over from scratch," Yoshida admits. Since oil seals incorporate multiple materials, even a slight adjustment to the composition of one material can affect functionality, forcing a complete reconfiguration of all materials.
There is also a constant demand to reduce production costs. This means that mass production must use existing equipment as-is, and changes in production items (setup) must proceed smoothly. "Oil seals may appear to be simple products, but they are composites with complex structures," Yoshida explains, highlighting the challenge. "Each adopted technology introduces various factors." In the past, for example, a sudden switch from Japanese-made oil to Chinese-made oil during development caused unexpected leakage issues and created panic. As the shift to electric vehicles (EVs) progresses, it remains to be seen what types of oils Chinese EV manufacturers will adopt.
Even so, Yoshida smiled as he said: "Development work is very rewarding." Sometimes material development can unexpectedly produce new characteristics as a byproduct. Achieving the desired performance metrics after repeated failures also brings an unparalleled sense of accomplishment.
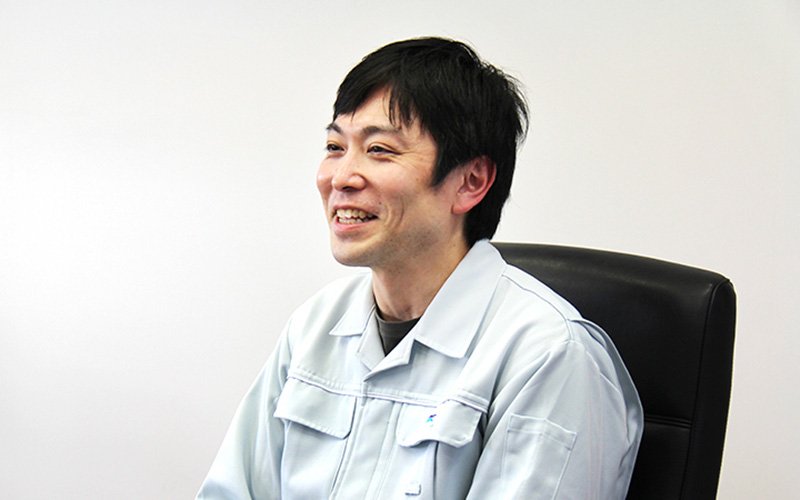
Suguru Yoshida
Material Engineering 4, Material Engineering Department, Corporate Technology Office, NOK Corporation
After being assigned to Eagle Industry Co., Ltd., Yoshida was responsible for developing and improving materials for water pump seals and car compressor seals at the Okayama Plant. In 2014, he transferred to NOK, where he worked on oil seal material development at the Shonan R&D Center. In 2017, he relocated to the Fukushima Plant, where he continues his quest to develop and improve oil seal materials.
- Note:Data, positions and titles in this article are current as of February 2023.