Handling Opposing Functions: Oil Seals and Surface Design
A major independent automotive parts manufacturer highly regarded for its technical capabilities. NOK is a key supplier to all Japanese automakers. Its particular strength lies in oil seals, the product the company was founded to manufacture. Used in engines, gearboxes and hydraulic equipment, oil seals must prevent the leakage of oil, water and gases while simultaneously circulating fluids on the sealing surface to enable lubrication. This low level of friction saves energy. Although they may appear to be simple rubber rings, NOK is constantly upgrading these oil seals through improvements in surface functionality, material selection and structural enhancement when in contact with rotating shafts.
Enhancing functionality through a multifaceted technical approach
NOK supplies approximately 60,000 types of oil seals worldwide. These seals are used in a wide range of products, including automobile engines and powertrains, construction machinery, hydraulic systems and engines for agricultural machinery, office equipment (OA) including multifunctional devices, and household appliances such as electric shavers. Their sizes range from 1.5 millimeters to 6.3 meters in diameter, yet the essential function of balancing sealing capability and reduced friction torque remains consistent.
NOK continues to develop oil seals using three technical approaches to better meet customer needs: surface functional design, material design, and shape design. The Shonan R&D Center (in Fujisawa City, Kanagawa Prefecture) leads this effort, with support from the main plant, the Fukushima Plant (in Fukushima City, Fukushima Prefecture), and other facilities involved in oil seal development.
Reducing friction torque through surface innovation
The first of our three approaches, surface functional design technology, involves modifying the surface shape of the contact area between the rotating shaft and the oil seal (contact surface) to suppress the generation of frictional energy (reducing torque). Traditionally, the focus was on improving surface micro-shapes through processing methods or material variations, but recent developments include applying coatings to the surface, particularly for engine oil seals.
According to Hideaki Nagahamaya, section chief of AI Design Section 1 in the Oil Seal Division of the Design Department at the Fukushima Plant, the "TF Coat" coating developed in 2006 successfully reduces friction torque by 30% compared to conventional products, and maintains its efficacy even after 100,000 kilometers of vehicle use. It has also demonstrated strong adhesion in evaluations based on the Japanese Industrial Standards (JIS), and has been adopted in NOK's new product, Le-μ's.
Please enlarge the screen to view
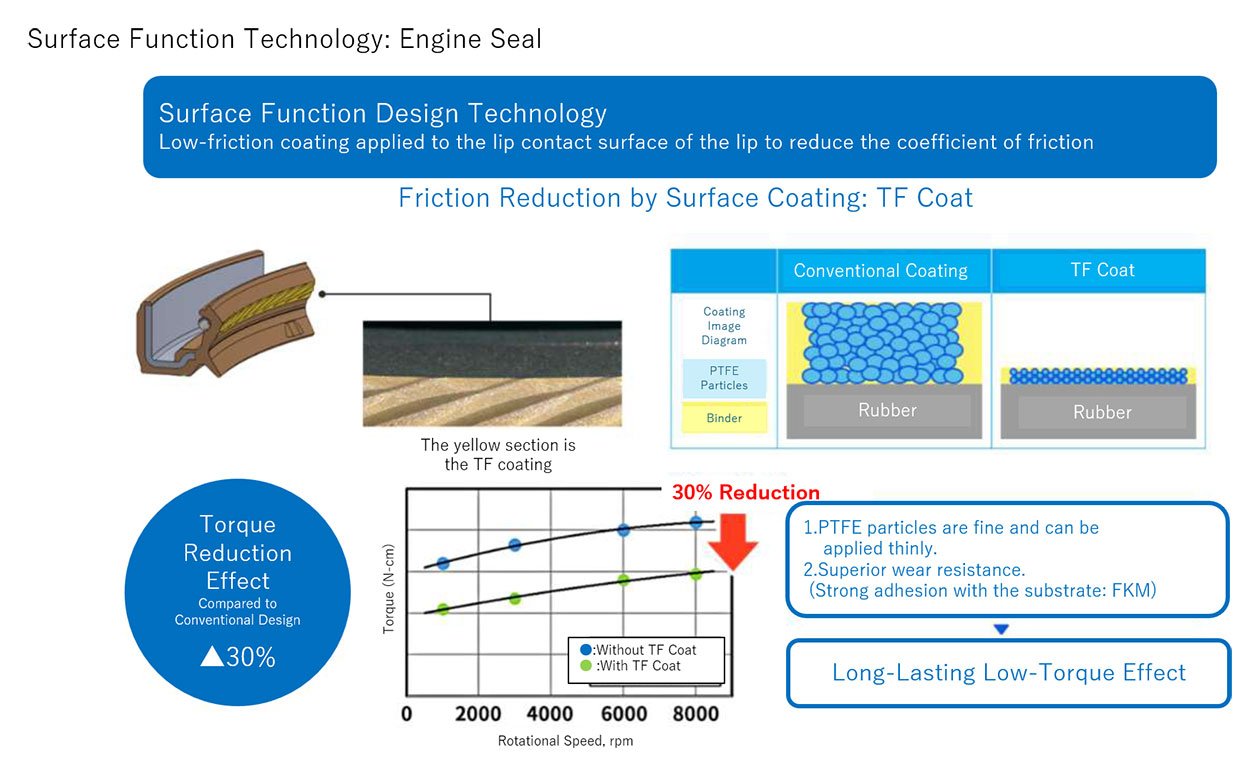
Please enlarge the screen to view
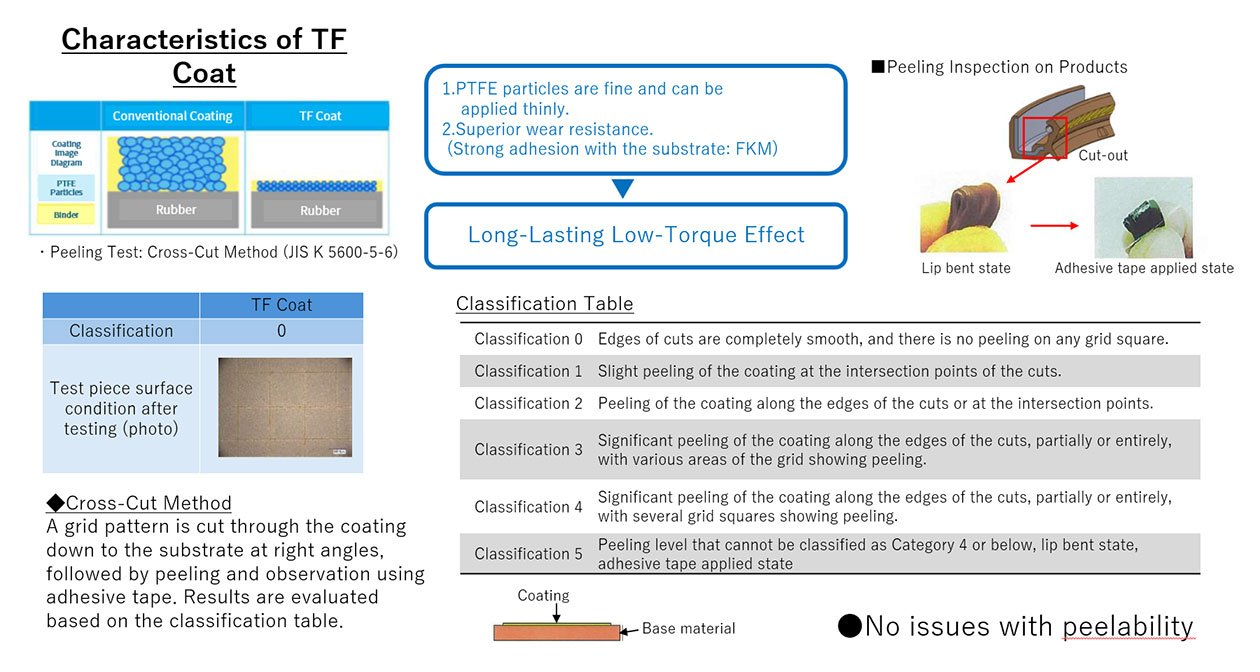
The oil seals used in automotive engine shafts can withstand rotational speeds of up to 8,000 revolutions per minute with minimal wear, requiring no replacement. They are high-durability products that maintain their functionality even after approximately 300,000 kilometers of use.
Why can oil seals effectively seal oil while minimizing wear? Because of their unique shape. When the rotating shaft starts turning, oil fills a gap of a few micrometers (one-millionth of a meter) between the shaft and the oil seal, preventing wear on the oil seal. Moreover, the oil does not escape from this gap. While this phenomenon has long been known, the specifics remained unclear. NOK has named this the "Sealing Theory" based on the company's internal analysis.
The TF Coat coating was developed to take advantage of the Sealing Theory by reducing the size of PTFE (polytetrafluoroethylene) particles in the material. This creates a thinner coating layer and ensures that the particles evenly cover the surface. Nagahamaya recalls: "We faced challenges in selecting the resin (binder) that would bond the PTFE particles, since each sample had to be tested individually." The development process involves constant trial and error. It is this diligent effort that enhances product functionality.
The importance of technology amid electrification
The automotive industry is moving toward electrified vehicles such as electric vehicles (EVs), shifting the primary driving force from engines to motors. However, as Nagahamaya notes: "Oil seals are still needed on the rotating shafts of EV drive motors." For that reason, development continues unabated. Unlike engines, motor shafts rotate at higher speeds and can reverse direction, requiring oil seals with functions different from those previously used. Oil seals must also evolve to maintain their sealing performance specs while further reducing frictional energy. Nagahamaya, who is primarily responsible for evaluating oil seal performance, is intent on the crucial goal of cutting frictional energy by an additional 30%. Development on this is about 80% complete, and the team is now addressing any remaining issues before incorporating this innovation into existing mass-production facilities.
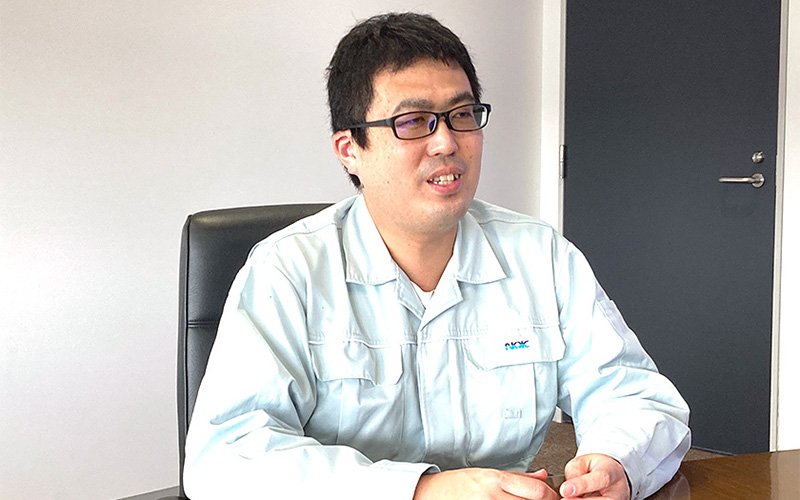
Hideaki Nagahamaya
Section Manager, AI Design Section 1, Design Department, Oil Seal Division, NOK Corporation
After joining NOK, Nagahamaya was responsible for testing engine seals and transmission-related seals, as well as evaluating products using TF Coat. In 2013, he worked in product design for transmission seals, contributing to the development of differential side seals with enhanced resistance to muddy water. After serving as an experimental section assistant manager and product design section assistant manager, he became the section manager of AI Design Section 1 in 2021, leading a team of 21 members.
- Note:Data, positions and titles in this article are current as of February 2023.