Stretchable FPC (Part 2):
Developing Applications for the Stretchable FPC through Tireless Engineering Efforts That Address Societal Needs
Developing technologies and products that address societal challenges and needs became Mektec's new focus after a bitter experience prompted a shift in their approach to printed electronics (PE) and flexible printed circuits (FPC). The personal connections established during a previous project proved invaluable in this endeavor. A promising application they identified — sensing devices for the medical and healthcare fields — matched perfectly with their technology's ultra-thin, stretchable properties. Since this was a new domain, however, they encountered numerous challenges during the development process that differed from their prior experiences.
"What if it were disposable?"
Unlocking new applications with a bold shift in thinking
Where could they find a market for the stretchable FPC made with PE? Initially, Mektec envisioned applications such as the surfaces of soft robots, which began gaining attention around 2010. However, when they tested a sample that used silver paste to create electronic circuits (patterning) on elastomer material sheets, they discovered that stretching it just once caused the resistance to increase. Even when it reverted to its original state, it failed to regain its initial properties. Further stretching cycles increased resistance even more, making it unsuitable for precise current control, such as in robot control systems.
This led to a shift in perspective. If repeated use was unfeasible, what about making the products disposable? They then explored domains where the benefits of the stretchable FPC could be maximized, such as flexibility that allows the entire FPC to stretch, thin and lightweight properties, and high breathability and moisture permeability. Considering both the strengths and weaknesses of the product, they identified medical and healthcare fields — which prioritize hygiene management — as an area with significant societal demand. At the time, wearable electronics were gaining attention, although the market was still in its infancy and specific applications were lacking. With this in mind, they turned to Professor Takeshi Sekiya of Osaka University, with whom they had established ties during past FPC research.
Around this time, Professor Sekiya was intensifying his research in brain science to tackle issues associated with Japan's super-aging society, such as preventing brain diseases and Alzheimer's-related dementia. As part of this effort, he launched a project to develop a brainwave meter that could easily measure brainwaves for risk diagnosis of such diseases. Professor Sekiya wass using electrode sheets formed on thin film as the bio-interface to capture brainwaves. The challenge was that even though the film was thin, its lack of pliability when applied to the human body made it to feel tight, causing discomfort.
Since brainwaves are extremely weak signals — measuring just a few millionths of a volt — achieving a snug fit to the skin is essential, even when attached to the forehead. At this critical juncture, Professor Sekiya encountered Mektec's stretchable FPC. He realized that the product could serve as an electrode sheet capable of closely conforming to skin wrinkles and enabling accurate brainwave acquisition. This led to Mektec and Professor Sekiya's collaborative development of an electrode sheet for patch-style brainwave sensors (Figure 1). Iwase recalls visiting Professor Sekiya's lab on December 22, 2014, to show him the stretchable FPC. "I will never forget Professor Sekiya's words when he saw it: 'With this technology, my brainwave sensor can become a reality.'"
Please enlarge the screen to view
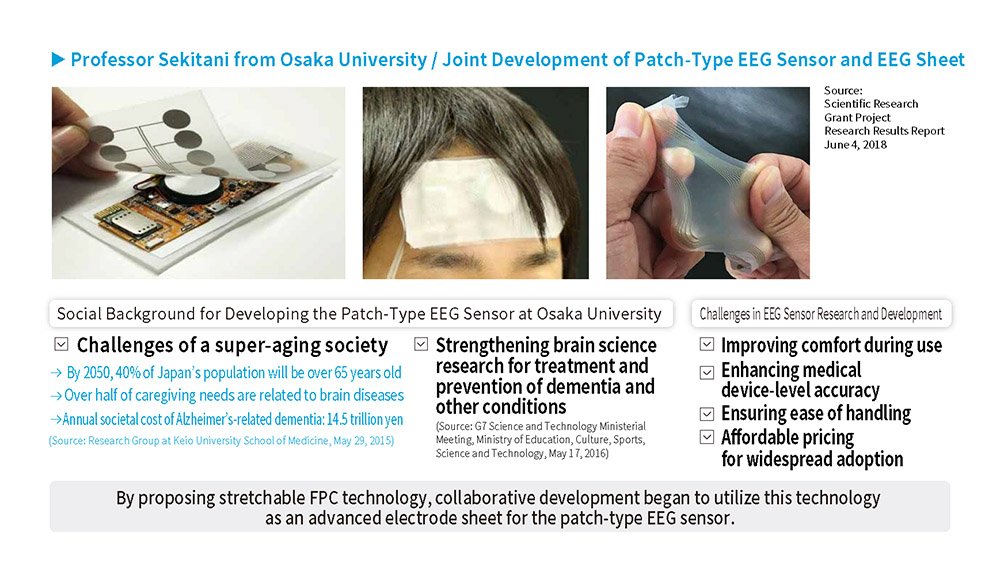
Building support through internal lobbying efforts to achieve commercialization
Although external connections provided a glimmer of hope, the project had faced two derailments that had lowered internal enthusiasm for PE development. The number of members in the Product Development Section had also been cut. Despite this, Iwase believed that issues related to brain diseases in older people were crucial societal challenges that needed to be addressed. He also felt confident about the potential for commercializing the electrode sheet.
Iwase carried out lobbying efforts to rebuild motivation and support internally. He invited Professor Sekiya to NOK and Mektec headquarters to present the technology to executives, and even demonstrated brain age measurements using brainwave sensors. He also explained to factory workers how the electrode sheets would be used through videos and other tools. "Unlike traditional FPC that were embedded in devices and hidden from view, electrode sheets are visible as products. This aspect also boosted morale on the production floor," Iwase explains.
Unlike the photolithography and etching processes typically used to make the FPC, PE requires only three steps for pre-processing, making it much simpler. This simplicity intrigued the management of MEK-J, a Mektec subsidiary responsible for FPC production. "We received strong support for commercialization from MEK-J, which was another helpful tailwind," Iwase notes.
Iwase himself created development samples to meet Professor Sekiya's requests for the electrode sheets. After delivering a sample in about two weeks, they would identify issues on the spot, and Iwase would return two weeks later with an improved version. This cycle of rapid response earned him growing trust as a development partner. "Above all, forming a network of collaborators — both external contributors and internal colleagues in manufacturing, process manufacturing, and production engineering departments — was crucial," Iwase reflects.
Several technical challenges had to be addressed during the commercialization of these electrode sheets. For example, a cable to allow external connections had to be integrated into the sheet to transmit signals from the electrode sheet to the measuring device. Its flexible nature, however, made it hard to directly link the stretchable FPC to a connector. To resolve this, a deliberate choice was made to incorporate a non-stretchable, film-based cable in the stretchable FPC (Figure 2).
Please enlarge the screen to view
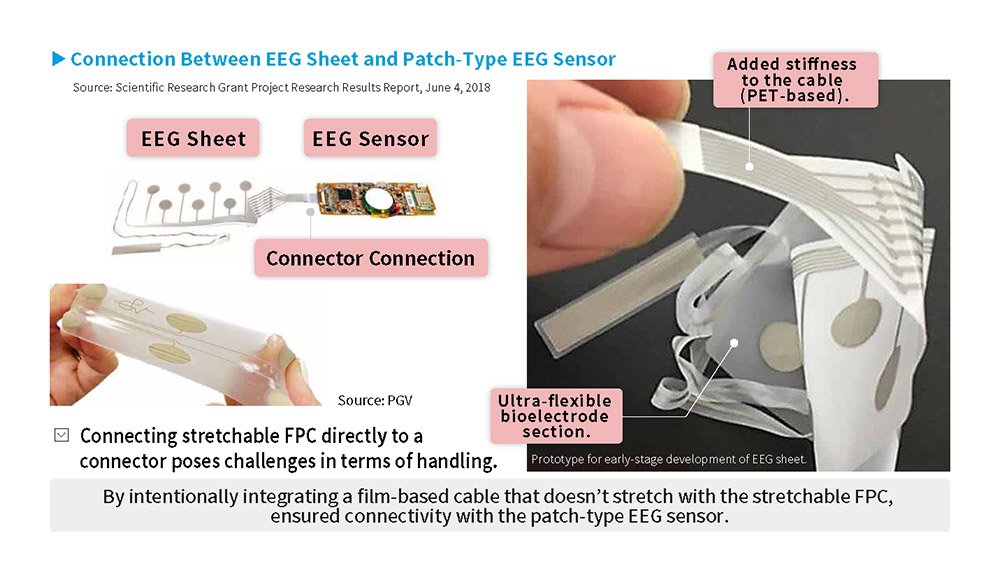
A biocompatible adhesive was incorporated into the stretchable FPC to ensure that the electrode sheet would stay in place on the skin. However, Mektec had not previously used materials with such properties during FPC production. "Finding a reliable supplier for medical-grade materials was a significant challenge," Iwase explains.
When considering mass production, using new materials not previously handled in FPC manufacturing also posed other hurdles. "We consulted experts familiar with these materials and worked with external analysis and testing organizations to verify that no environmentally harmful substances were being used," Iwase adds.
On the path to mass production: The next challenge is usability
By the second half of 2016, Professor Sekiya's patch-style brainwave sensor development project had evolved into a business venture with the establishment of the startup company PGV. In tandem with this development, Mektec finalized plans for the mass production of its electrode sheet (Figure 3).
Please enlarge the screen to view
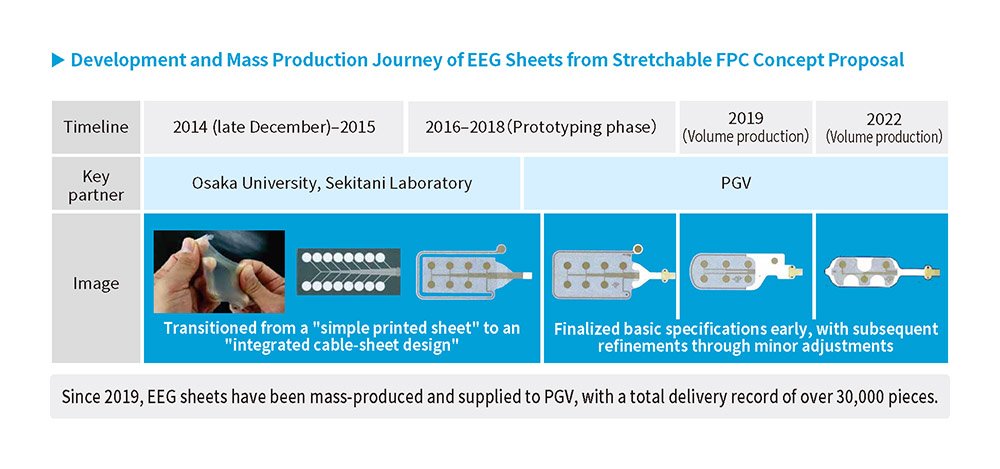
After mass production of the electrode sheets began, areas for improvement — such as making them easier to apply to the forehead — soon became apparent. Takumi Kaneko, assistant manager of Development Section 2 in the Technical Headquarters Development Department, explained: "At present, users must handle both the electrical and mechanical connections themselves when attaching the electrode sheet to their foreheads. That can be a bit cumbersome for those unfamiliar with the process." To address these challenges, the team is working to upgrade usability, such as developing conductive adhesive items that allow bioelectric potentials to be measured immediately after the sheet is applied to the forehead.
As development continued, new ideas emerged from Professor Sekiya and his team, including ways to refine the electrode sheet and explore applications for different uses. For instance, if usability improves to the point where anyone can easily use a patch-style brainwave sensor, it could be distributed through drugstores. This would allow users to measure their brainwaves regularly, much like using a thermometer. They could visit a hospital for a more thorough examination if abnormalities were detected, enabling applications like early dementia diagnosis.
There is also interest in innovative uses such as measuring brainwaves while playing sports and various other activities. Potential applications that go beyond measuring brainwaves are also being explored. For example, attaching an A3-sized electrode sheet to the rounded belly of a pregnant woman could allow the measurement of uterine electromyographic signals during childbirth. "According to Professor Sekiya, analyzing these bioelectric signals could also determine whether a pregnant woman can deliver normally, and even capture the bioelectric signals of the baby inside the womb," Iwase explains.
Expanding applications: "Could it be used for beauty devices?"
With a mass-production system in place for its electrode sheets, Mektec began exploring ways to expand its technology and expertise into other applications. These efforts mainly aimed to showcase examples of stretchable FPCs and brainwave sensor applications at wearable-related exhibitions to reach as many people as possible. This steady activity paid off in January 2022 when a representative from the development team of YA-MAN, a manufacturer of beauty and health devices, took note of Mektec's electrode sheets at an exhibition.
"Could this be used as an EMS sheet for beauty devices?" While Mektec had been actively targeting medical and healthcare applications, beauty was unexpected territory. Although the patch-style brainwave sensor was already in mass production, using the technology for beauty devices meant catering to a much broader and more frequent user base. Naturally, consumer-facing products would face different hurdles compared to medical-grade applications. Nevertheless, this represented an exciting new opportunity.
Other manufacturers were also showcasing stretchable circuits and electrodes at wearable-related exhibitions, so why did YA-MAN take an interest in Mektec? The deciding factor was the product's simplicity.
Competitors highlighted their ability to incorporate components into the substrate as well as the multifunctionality of their products. However, a simpler structure with lower costs is preferable for disposable products like bioelectrodes. "At Mektec, we were aware of the demand for mounting components onto the stretchable FPC. The fact that we had already established a production system capable of supplying a simple structure in mass quantities matched YA-MAN's needs," Iwase explains.
Although EMS sheets for beauty devices and electrode sheets for brainwave sensors share a similar structure, EMS sheets work differently. Instead of measuring voltage signals, they send low-frequency signals into the body to provide electrical stimulation. Daisuke Shiokawa of Development Section 2 in the Development Department at Engineering Division says: "We began by verifying whether this was even possible. Additionally, there were requests to apply the electrode sheet to skin moistened with beauty serum for beauty device applications. This led us to collaborate with the client and develop the idea of using hydrogel," he recalls (Figure 4).
Please enlarge the screen to view
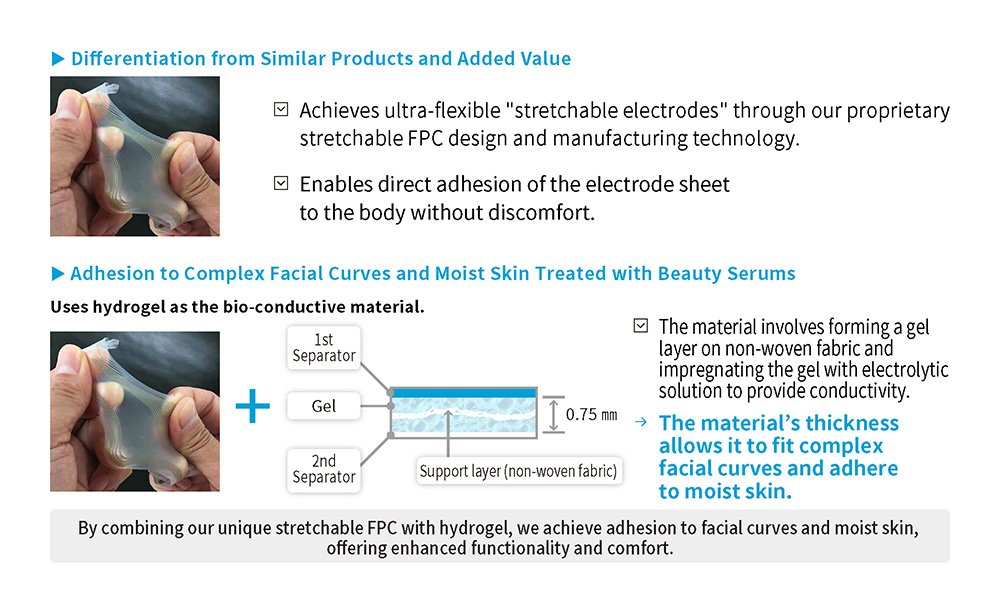
The formidable challenge of halogen
The decision to use hydrogel introduces a significant obstacle: hydrogel is essentially a halogen compound.
Mektec's flagship FPC products must meet halogen-free standards. This is because halogen-based materials release substances during incineration that can negatively affect the manufacture of electronics requiring high corrosion resistance. For the beauty device project, however, halogen materials were necessary to meet customer demands. Overcoming this hurdle required significant internal explanation, persuasion, and procedural adjustments. Strict regulatory thresholds also had to be met to allow halogen materials in the factory. The hydrogel being considered far exceeded these internal limits. Negotiations were anything but straightforward. "We began by quantitatively analyzing how much halogen the hydrogel contained, and determining the rules necessary to prevent it from coming into contact with the FPC," Shiokawa explains.
Shiokawa proposed creating a designated area with a dedicated production line to ensure that existing products would not come into contact with halogen. This included setting strict rules for items like work uniforms and gloves used within the area. He traveled extensively to meet with internal stakeholders across departments, presenting the case to gain approval for producing the EMS sheets for beauty devices. "We held weekly meetings with staff from almost all relevant departments — including materials procurement, manufacturing, and quality control — to explain the situation and propose solutions," he recalls.
As a result, the commercialization of the EMS sheets for beauty devices was finalized in March 2023. Reflecting on Shiokawa's efforts, Iwase remarks: "For over a year before commercialization was approved, he went above and beyond his development duties, managing everything from interdepartmental coordination to handling miscellaneous tasks on the mass-production floor. His efforts helped establish trust with the production teams."
The speed of the events that followed was remarkable. In April, just a month after commercialization was approved, mass-production plans were finalized, and by July — only three months later — mass production had begun. Even within Mektec, this pace was astonishing.
"Can we do this?"
"We have to do it."
There were countless challenges to tackle, including procurement, operating the production line and ensuring quality, leaving no room for hesitation. However, a spirit of actively embracing new product challenges is part of the NOK Group's corporate culture. With the full support of MEK-J, a NOK Group manufacturing subsidiary that had strongly backed the project since recognizing the benefits of PE, the team met these tough demands.
At this stage, new challenges emerged since Mektec was handling a B2C product for the first time. The EMS sheets for beauty devices manufactured at Mektec's factory had to be packed into consumer-facing bags specified by YA-MAN and shipped. "From their perspective, the packaging was considered part of the product. For us, since we had never had to think about packaging while producing the FPC for B2B clients, this was a completely new experience," Shiokawa explains.
Since this product was meant to reach consumers directly, even details like ensuring that the heat-sealed areas of the packaging were perfectly aligned required a high level of quality control. With an extremely tight timeline to launch production, there was no time to seek external expertise. Instead, the team — with help from their colleagues— introduced new packaging equipment. "We decided to tackle this ourselves, researching, experimenting and repeatedly refining the packaging process," Shiokawa shares.
As a result, a system was established to produce up to 100,000 EMS sheets for beauty devices per month under the product names Design Lift and Design Lift More. "I believe no company but Mektec has achieved this scale of mass production for the stretchable FPC. This vertical integration was only possible because developers like us worked as one with teams from design, technical departments, quality assurance, procurement and manufacturing. This success will serve as a springboard for further expansion," Iwase concludes.