Stretchable FPC (Part 1):
How a Stretchable Substrate Resembling a Medical Patch Found Its Way into Beauty Device Electrode Sheets
Printed circuit boards are a key component of electronic devices. When thinking of circuit boards, many people picture rigid boards densely populated with IC chips. However, flexible printed circuits (FPC), which are pliable and capable of withstanding repeated deformation, are commonly used in thin, compact devices such as cameras, smartphones and tablets. Within the NOK Group, Mektec is a key player in advanced FPC technology and has pioneered new applications.
Mektec developed the ultra-thin, stretchable FPC, which is as soft and pliable as a medical patch. This flexibility and stretchability make it suitable for medical devices that adhere to the body to measure brainwaves and other vital signals. More recently, FPC have been used in beauty devices as electrode sheets that adhere to the skin.
The core technology enabling this level of flexibility and stretchability is called printed electronics (PE), which prints electronic circuits directly onto substrates. However, the journey to commercialize the PE-based stretchable FPC was far from straightforward. Two development projects utilizing PE technology were halted. By leveraging the lessons learned and gradually adapting their product goals, however, Mektec persevered. This persistence, combined with a shift in mindset toward addressing societal needs, ultimately led to the creation of the stretchable FPC we have today. Originally driven by the goal of reducing FPC manufacturing costs, Mektec's journey to producing electrode sheets for medical and beauty devices is a story of innovation.
"With PE, we could make FPC manufacturing so much more efficient!"
FPC history dates back further than expected, with origins in the 1960s when they were used in space exploration, aviation and military applications. By the 1970s, they expanded into consumer markets, rapidly being adopted for products requiring compact designs, such as single-lens reflex cameras and slim calculators. Nippon Mektron (now Mektec) was founded in 1969 as an FPC manufacturer and began expanding its production and sales bases to regions including Taiwan, the U.S., Thailand, Hong Kong, Singapore, China, Vietnam and Europe, starting in 1986.
PE gained global attention in electronics manufacturing around the year 2000, focusing on creating entire electronic devices and components through printing technology. Mektec began exploring the commercialization of PE in 2008 through its newly established Product Planning Office. The appeal of PE lay in its potential to simplify the pattern formation process for the FPC — which traditionally required 11 steps using photolithography and etching — into just three steps. This drastic process simplification promised significant efficiency gains and substantial manufacturing cost reductions (Figure 1).
Please enlarge the screen to view
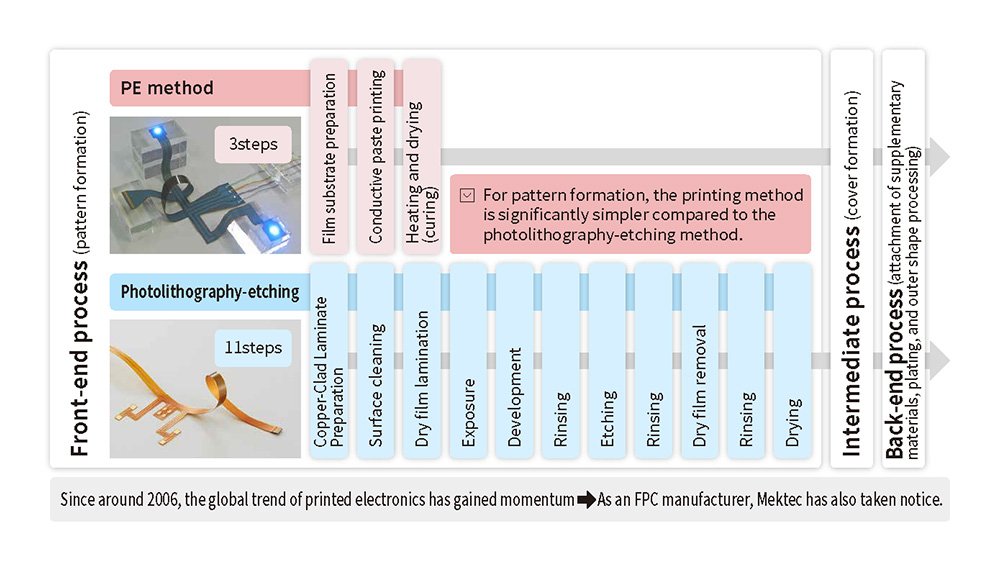
PE-based FPC manufacturing offers additional advantages: as a "dry" process that avoids solutions, it is environmentally friendly and allows for cost-effective production of diverse, small-lot product lines. With this ideal in mind, Mektec not only built an in-house printing line for the front-end FPC processes but also developed a new silver paste with printing capabilities. The company enabled electroplating on printed silver patterns, making it possible to perform solder reflow for mounting electronic components on the FPC.
As development progressed, however, it became clear that realities needed to align with expectations. For instance, while Mektec manufactured FPC using PE and showcased the technology at trade shows to assess market potential, the limitations of printed products began to emerge. In particular, PE could not achieve the fine wiring possible with photolithography and etching, restricting the range of applicable products. From a reliability perspective, such as high-temperature insulation characteristics, FPC made with PE proved less practical than those made with photolithography and etching.
Even the anticipated cost-reduction effects did not materialize as expected. While PE simplified the front-end process, the intermediate and back-end processes still accounted for a significant portion of the total manufacturing cost, and those costs remained unchanged. For Mektec, which could already mass-produce the FPC cost-effectively using photolithography and etching, PE turned out to be more expensive. Additionally, the environmental benefits of PE — its lower environmental impact — did not resonate strongly with customers at the time, since environmental concerns were not as prominent as they are today.
Reflecting on the insights gained regarding FPC production costs across all processes, Masayuki Iwase, then the manager of Development Section 2 in the Development Department at Engineering Division, who was involved in PE research within the Product Planning Office, notes: "At the time, this realization might have been unique to our company." He elaborates: "Among the manufacturers considering PE adoption back then, few were involved in the full spectrum of substrate manufacturing, including the back-end processes, as Mektec was. Most companies working on PE-based substrates were startups and focused only on the front-end processes."
Ultimately, the ambitious project of producing FPC using PE failed to uncover a compelling reason to continue, leading to the project's suspension by the end of 2011. Reflecting on this period, Iwase recalls: "PE, which originated in Europe, initially generated significant industry-wide excitement. By around 2011, though, that enthusiasm had waned. Given that we already had the capability to mass-produce FPC at low cost, the consensus was that continuing this effort wouldn't bring additional benefits. This perspective led to a significant drop in motivation among the Product Planning Office members involved in the research."
Applying PE to transparent FPC to meet growing touch panel demand
PE-related research was not limited to FPC manufacturing alone. Around 2010, Mektec began pursuing a parallel project aimed at mass-producing transparent FPC for touch panels — a response to rapidly growing demand driven by the rise of smartphones and tablets. Display manufacturers were ramping up production of touch panels, but concerns arose over the depletion of ITO (indium tin oxide) materials, widely used as transparent electrodes in liquid crystal displays and organic EL displays. At the same time, there was increasing demand for flexible touch panels with added value, such as bendability and rollability.
To address these needs, Mektec's Product Planning Office, where Iwase was based, started research in 2010 on FPC for touch panels using ITO-alternative materials like PEDOT/PSS and AgNW. These materials offer both conductivity and the ability to transmit visible light.
At the time, the mainstream ITO alternatives were coating materials containing PEDOT/PSS or AgNW applied to one side of a film. As shown in Figure 2, creating flexible touch panels using these materials required forming electrode patterns (indicated in purple) aligned along the X and Y axes as separate panels, which were later laminated together. To form such electrodes into a highly transparent film, it was necessary to create etching resist patterns and use specialized etching solutions.
Please enlarge the screen to view
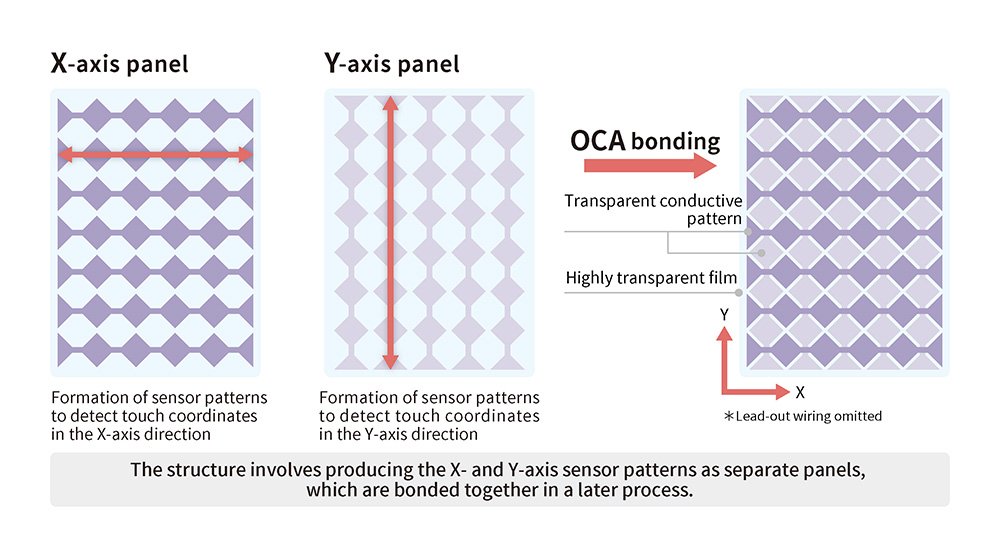
At the time, PEDOT/PSS was a delicate material with low chemical resistance. That posed a problem — it could not withstand the multiple chemical processes used in conventional photolithography and etching methods, degrading performance. To address these limitations, Mektec minimized performance degradation by adopting a "dry" process using screen printing (which avoids using chemicals) in the initial stages while retaining a chemical-based etching process for later stages (Figure 3).
Please enlarge the screen to view
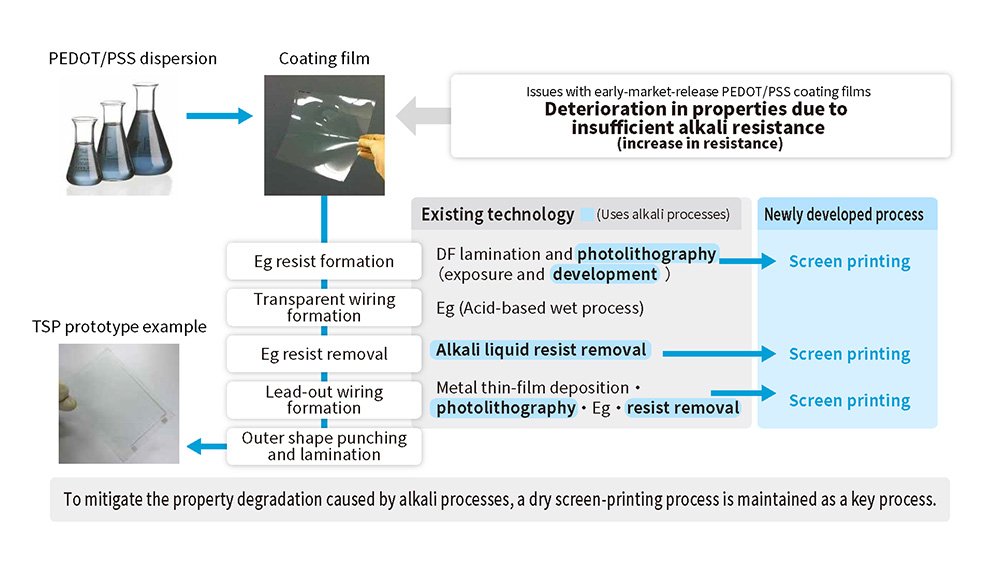
To properly use PEDOT/PSS with screen printing, however, required additives such as thickeners, which lowered conductivity. Increasing the thickness to reduce the wiring resistance on the transparent substrate also intensified the blue tint inherent to PEDOT/PSS, reducing transparency. Despite repeated trial and error to meet requirements, developments like the emergence of high-transparency touch panels in devices like iPhones led clients to abandon the project. As the supplier, Mektec was also forced to discontinue its development efforts.
Stretchable circuits born from the combination of printed silver paste and elastomer sheets
So two projects utilizing PE were suspended, and Mektec's challenges continued. The Product Planning Office, which had been working on catching up with new trends like FPC manufacturing through PE, transitioned in 2014 to become the Product Development Department, focusing more intensively on PE commercialization. The next target for PE commercialization was creating stretchable FPC capable of extending in all directions.
Mektec was already producing the stretchable FPC by around 2010. However, these early products featured a design in which copper was formed into a wave shape and sandwiched between urethane sheets, limiting stretchability to a single direction. Furthermore, the stretchability was also limited to 110%, which hindered any significant market expansion.
The breakthrough came when a materials manufacturer adopted a newly developed, stretchable silver paste. By patterning the paste onto an elastomer sheet, they discovered that it was possible to create a substrate that could stretch in all directions, just like rubber.
Interestingly, the stretchability of this silver paste was not initially recognized. Mektec hypothesized that printing the silver paste — originally intended for film used in 3D molding — onto a soft sheet could result in stretchable wiring resembling rubber (Figure 4). "At that time, a supplier of FPC materials brought us a thin, highly stretchable elastomer sheet that also allowed vapor and air to easily pass through it. This was the spark that inspired us to develop stretchable FPC using PE," Iwase recalls.
Please enlarge the screen to view
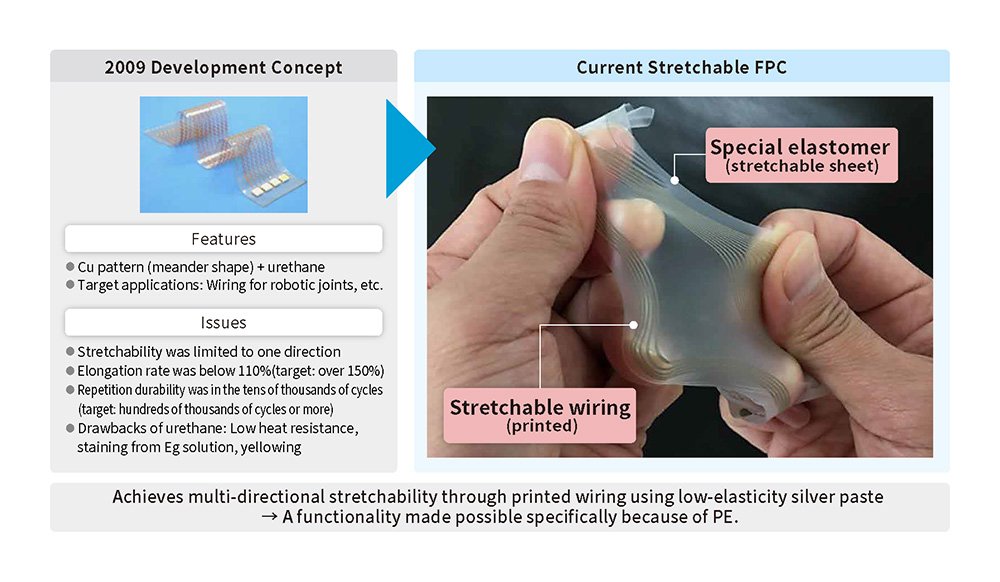
Efforts to commercialize stretchable FPCs began in mid-2015 following the suspension of transparent FPC development. Initially, the silver paste contained flakes of silver, which caused clogging during continuous printing. To address this issue, Mektec collaborated with a silver paste material supplier to independently develop fine granular silver particle materials (Figure 5). This challenge and its solution were identified thanks to Mektec's extensive experience refining screen printing technologies.
Please enlarge the screen to view
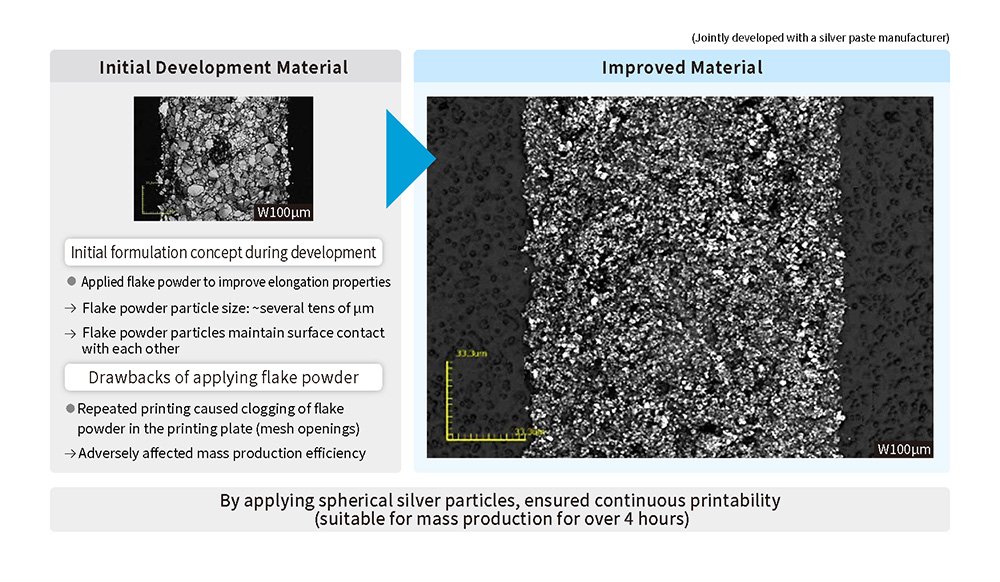
Product development rooted in societal needs
Through its previous endeavors, Mektec gained significant lessons in product development. When developing products directly in response to specific customer needs, the process often begins without any certainty regarding commercialization. If a customer decides not to adopt a product, the team is left with no choice but to search for other applications without clear leads. If no suitable needs are identified, the project risks being suspended.
"This marked a major turning point for us," Iwase notes. "After the suspension of those two projects, we realized that any development of new technologies and products must fundamentally address societal needs." As a result, the new PE development initiative, centered on the stretchable FPC, shifted its approach from being customer need-driven to one that focuses on addressing broader societal demands (Figure 6).
Please enlarge the screen to view
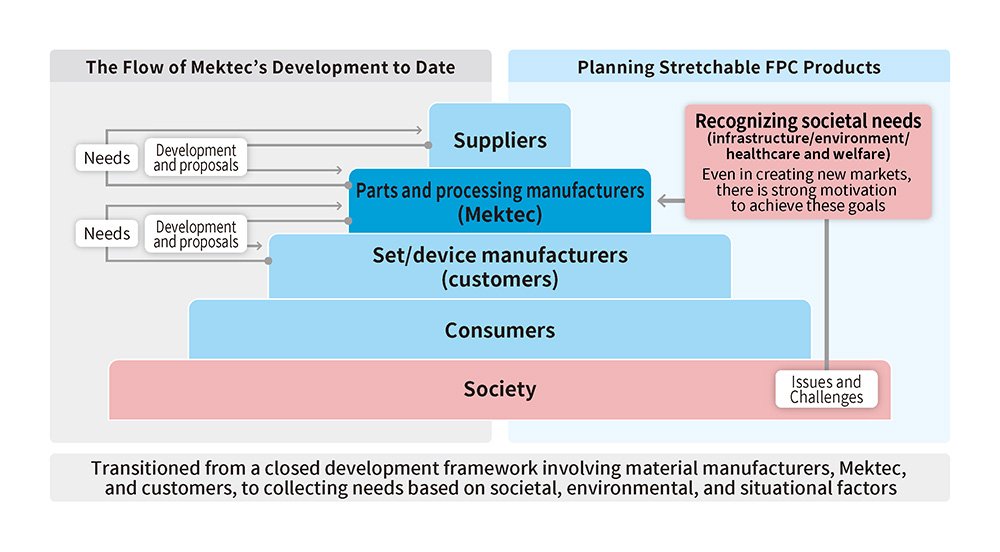
By 2014, the wearable electronics trend was gaining momentum, while the field of biosensing technology was also becoming more active, driven by the need to reduce caregiving and medical costs. Responding to these societal needs, Mektec identified demand for FPC that offered flexibility and stretchability, qualities that enable them to be comfortably applied to the human body for use in the medical field. The company then began seeking suitable partners for collaboration.
In the second part of this article, we will explore how Mektec considered societal needs to successfully mass-produce medical bioelectrode sheets and even expand into the beauty industry. We will explore the path to mass production, the challenges faced during commercialization, and the prospects of Mektec's stretchable FPC as a solution for industries.