Precision Manufacturing Technology Supporting Society:
Challenges in Fuel Cell Development (Part 2)
(Continuation from the previous part)
NOK's development of CELLSEAL — a gasket designed for fuel cells — marked a bold step into a new field. Bridging the gap between customer requirements and practical implementation involved analyzing specifications, uncovering underlying principles and mechanisms, negotiating with customers to fine-tune the required specifications, and ultimately establishing a mass-production system — a journey that took four years. So, how did the FC Solution Mass Production and Advanced Development Department engineers overcome challenges such as achieving micrometer-level precision and preventing gas leakage at the molecular level?
Interpreting requirements from first principles and adjusting specifications over four years
Designing the CELLSEAL first required clarifying the component's purpose, function and performance requirements (see Figure 1). This required close communication with the customers to understand their specifications and constraints while collaboratively refining and adjusting the details. According to Toshihiro Shimazoe, who oversees product design at the FC Solution Mass Production Development Department, the CELLSEAL project began with over 50 pages of detailed performance and functional requirements provided by customers. "Additional requirements were introduced during the development process," he explains.
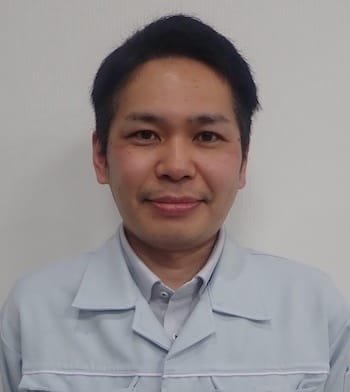
Please enlarge the screen to view
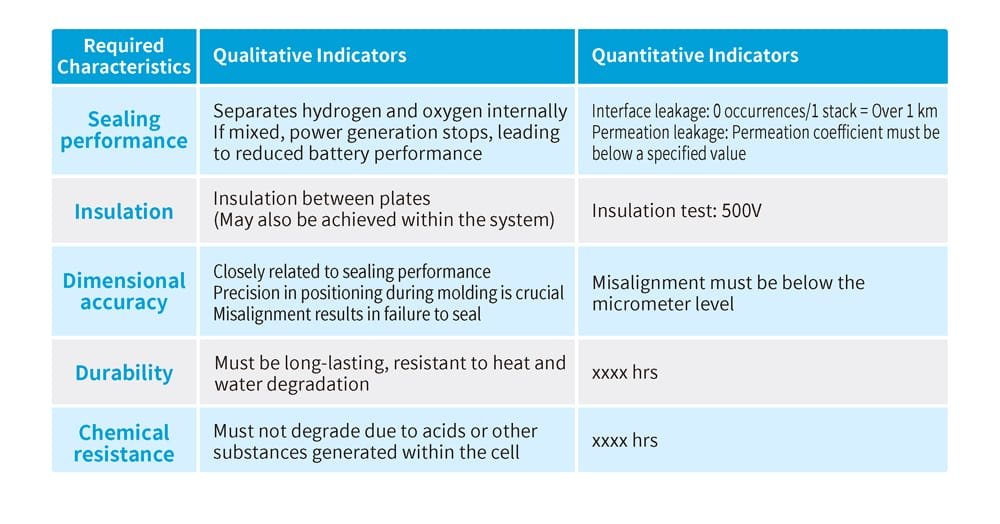
Among the specifications the customer requested, many are determined based on theoretical calculations. This is not always practical from an implementation perspective. If NOK were to meet these requirements as they were, the hurdles for implementation would be extremely high. With that in mind, the team needed to identify the specification limits that could balance the performance and durability requirements of the fuel cell with the feasibility of actual implementation.
This process proved to be the most challenging part. Even when reviewing the requested specifications, there were often uncertainties that could only be clarified through design and testing. Verification was essential to ensure that the specified performance and functionality could be achieved, even if the specifications were followed. "We carefully analyzed the specifications provided and verified the details of each," explains Shimazoe. Throughout this process, alternative solutions were considered whenever certain requirements proved unfeasible. "We repeatedly negotiated and presented alternative proposals for each specification," he adds.
The difficulty of this negotiation process lay in the fact that the customer was not always be convinced just by hearing the verification results. The team had to articulate the underlying principles and mechanisms to gain approval to modify the specifications. This required exhaustive validation, a thorough explanation of the mechanisms involved, and collecting evidence to support alternative approaches. "We went through several prototyping stages, repeatedly tested, and incorporated areas where requirements could not be met into updated specifications," Shimazoe shares. Ultimately, it took three to four years from receiving the specifications to completing the design before mass production could begin.
Breaking preconceived notions with innovative thinking
One key factor behind the successful design was NOK's company culture, which encouraged open brainstorming and diverse perspectives within the development team. Initially, the team considered using existing manufacturing methods with a proven track record for attaching the seal to the separator. However, this approach could not achieve the precise height tolerances the seal required, which would compromise sealing performance. Recognizing this early on, the team shifted to a novel application method with which NOK had no prior experience.
"We realized early that simply refining conventional methods would eventually hit a wall, so we pivoted toward a new application method. We focused on breaking away from traditional approaches and collaboratively developing ideas with an open mindset," Shimazoe explains.
When it came to materials, NOK's extensive knowledge from years of studying permeation leakage played a critical role (Figures 2 and 3). "We've conducted research and simulations on permeation leakage for various materials and have developed seals with a sound theoretical understanding. This experience allowed us to select materials carefully, clearly explain the rationale behind our choices, and secure client approval," Shimazoe notes.
Please enlarge the screen to view
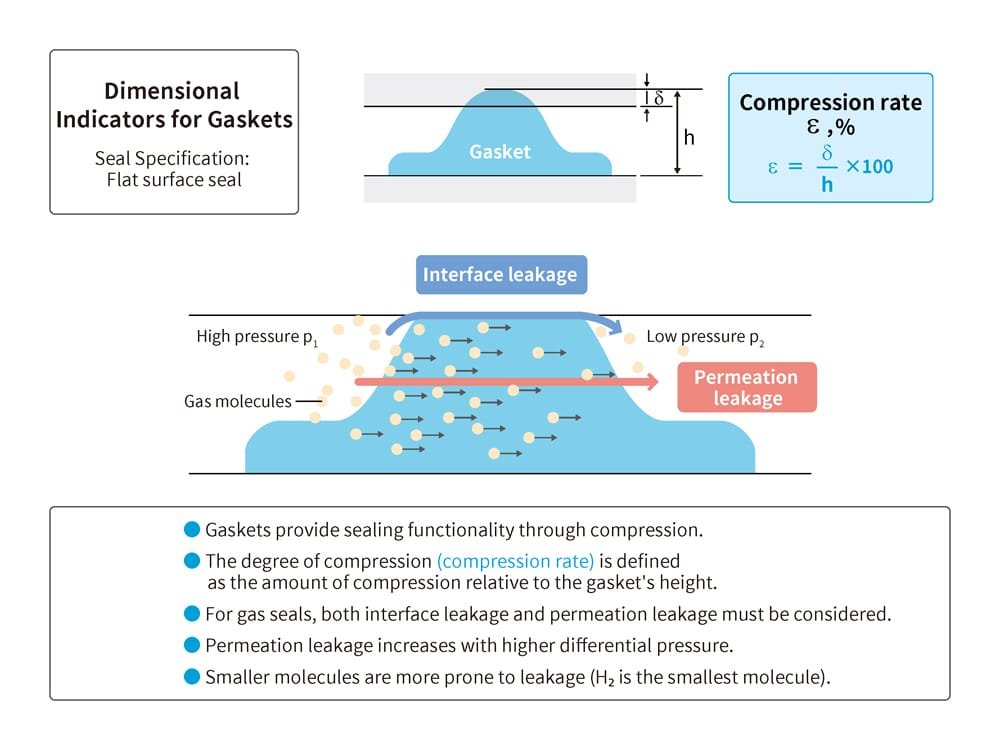
Please enlarge the screen to view
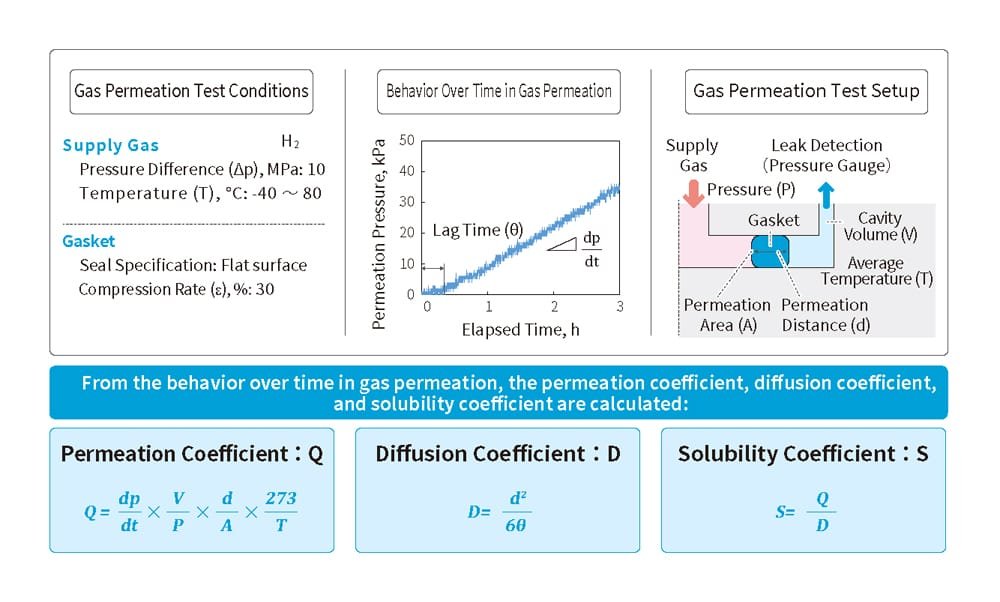
"Doesn't this overlook the stress caused by press molding?"
During the development stage, simulations are conducted to evaluate the performance and durability of product designs. This process involves stress analysis, thermal analysis and fluid analysis of the components to identify any issues. "We create analysis programs that allow us to input material properties, manufacturing methods, and customer-specified requirements such as temperature and pressure. Using those programs, we run simulations, adjusting the parameters according to the conditions," Shimazoe explains.
An analysis program was naturally developed for the CELLSEAL, and simulations were conducted. However, the process proved to be anything but straightforward. The development of CELLSEAL was unprecedented, and even the analysis program for evaluating it was still in its developmental phase. When the design data was applied, it sometimes failed to meet performance requirements as expected.
The cause was an overlooked parameter: stress caused by press molding. Some separators the CELLSEAL is applied on undergo press molding, and during this process, stress is generated internally when pressure is applied to the metal. The simulation did not initially account for this stress. "At first, we didn't factor in the stress press molding generated. When we ran the program as-is, the surface pressure during compression didn't match actual conditions and was lower than expected. As a result, when the CELLSEAL was integrated with the separator, it couldn't meet the sealing performance requirements," explains Takeshi Masaka, who is responsible for process design at NOK R&D's FC Solution Advanced Development Department.
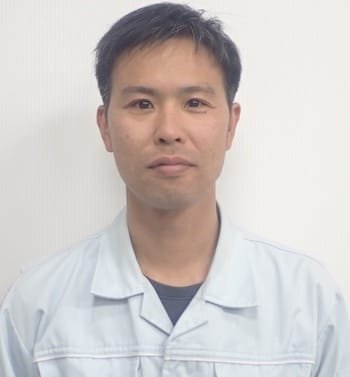
When simulations fail to deliver the desired results, the next step is to narrow down the possible causes. "In the case of stress in the separators, there were many aspects that the design department alone couldn't identify. We requested the participation of a team experienced in press molding to start by uncovering the realities of what was happening and then pinpointing the cause. It was like forming multiple hypotheses and systematically verifying each one," explains Shimazoe.
Encountering unexpected issues during prototype testing.
After completing the analyses and simulations of the designed components, the process moves to creating prototypes using 3D printers or machining equipment. However, this stage often required repeated back-and-forth between analysis and prototype creation.
In some cases, the process even required revisiting the detailed design phase. For instance, when the customer tested the prototype CELLSEAL NOK created during cell assembly, the company received urgent feedback: "The sealing performance isn't functioning at all."
Rushing to retrieve and examine the prototype, the team confirmed the lack of performance. Through painstaking investigation from multiple perspectives, Masaka says it became clear that "there was an issue with the structure of the cell when the CELLSEAL was incorporated and the cells were stacked."
When stacking fuel cells, precise control over how much the rubber of the CELLSEAL is compressed is critical. This control aspect had been overlooked in the initial design, resulting in a structure where the CELLSEAL was being compressed beyond its limit when the cells were stacked. This excessive compression deformed the rubber, lowering the intended sealing performance. Initially, the rubber was supposed to act as a spring to align the separators. However, further analysis revealed that this functionality was not being realized as designed.
After extensive trial and error, the team identified a solution: introduce a stopper on the separator to prevent the rubber from being overly compressed. "We designed a structure where a slightly elevated edge on the separator's outer frame limits the compression," explains Shimazoe. Simulations confirmed the effectiveness of this solution, leading to a revised prototype. When the client tested the updated prototype by stacking cells again, the desired sealing performance was achieved.
The final design was eventually settled through repeated testing and improvements using prototypes. The revisions and verifications the prototypes required totaled dozens of iterations. "For components like powertrains or engines, the number of prototypes typically depends on the client, but it's usually around two rounds of prototyping, followed by three additional validation cycles before moving to mass production," Masaka notes. A part like the CELLSEAL, which encountered issues dozens of times during prototyping, is highly unusual.
"The challenges stemmed from the lack of a standardized design for CELLSEAL and limited prior experience in this area," Shimazoe reflects. Addressing each issue head-on, unraveling mechanisms through repeated trial and error, and collaborating closely with customers to resolve challenges — this persistent approach is the driving force behind enhancing NOK's manufacturing and development capabilities.