Precision Manufacturing Technology Supporting Society:
Challenges in Fuel Cell Development (Part 1)
From automobiles and motorcycles to televisions, refrigerators, vending machines used for frozen foods and medical equipment in hospitals, countless machines are part of our daily lives. These devices are made up of thousands to tens of thousands of components. Their reliable operation is mainly due to critical and often unseen components performing their roles flawlessly. Behind these components lies advanced manufacturing technology: the ability to produce parts at sizes far smaller than the diameter of a single strand of hair and still ensure precision, durability under extreme conditions, and long-term performance. This craftsmanship plays a vital role in making such machines dependable.
This article focuses on fuel cells, a key technology for society's future. By exploring their mechanisms and the development stories from NOK’s R&D team, we will uncover the remarkable aspects of manufacturing that make these innovations possible.
Seal technology to suppress gas leaks: A pillar of the hydrogen society
Fuel cells generate electricity through a chemical reaction between hydrogen and oxygen. Although called "cells," they are more akin to generators, converting fuel into electrical energy with greater efficiency than conventional combustion-based power generation methods. One of their most notable benefits is their environmental impact: fuel cells produce no carbon dioxide (CO2) or nitrogen oxides (NOx). This makes them a critical technology for achieving a carbon neutral society. They are expected to gain traction, especially in applications like commercial vehicles (such as trucks and buses) that require continuous, long-distance operation.
Since its founding in 1941, NOK has been researching and developing oil seals for automotive engines and motors. The company is now leveraging its extensive experience and expertise in sealing technologies to develop gaskets for fuel cells. However, fuel cells remain a developing technology with limited implementation records. Requirements such as shape, performance and functionality vary widely depending on the customer, such as automakers. The gaskets NOK is developing are no exception — they demand highly diverse, high-performance and high-functionality specifications, which requires us to develop the materials and designs entirely from scratch.
Creating sealing rubber products requires micrometer-level precision
Fuel cells consist of a "cell," the smallest functional unit, consisting of two electrodes — an oxygen-supplying cathode (positive electrode) and a hydrogen-supplying anode (negative electrode) — and an electrolyte that facilitates ion movement. Automotive fuel cells have hundreds of these cells in a layered structure called a stack (see Figure 1). NOK supplies a CELLSEAL that attaches to the cathode separator (on the positive electrode side) and the anode separator (on the negative electrode side). These are critical in separating individual cells within the stack structure.
Please enlarge the screen to view
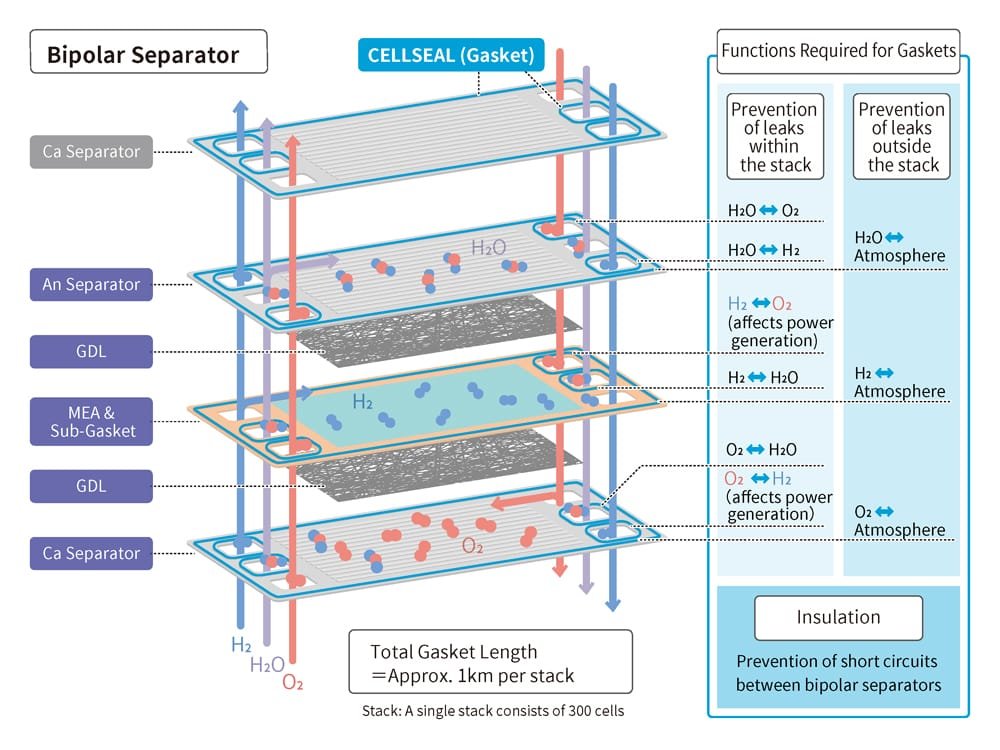
Please enlarge the screen to view
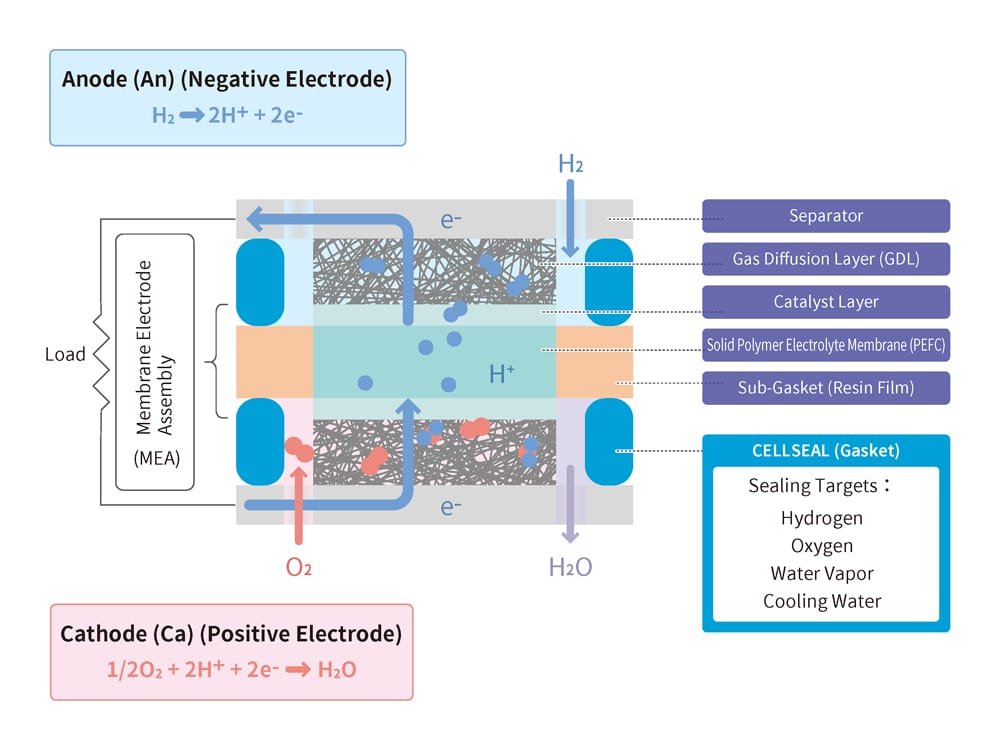
The role of CELLSEAL is to prevent hydrogen, oxygen, water vapor and other substances from leaking out of the cell during the power generation process (Figure 2). Leaking gases can lower power-generation efficiency and/or degrade the cells, causing various issues. To prevent these leaks, CELLSEAL uses the elastic properties of rubber to ensure a tight seal between separators without any gaps. Uniformity is also a crucial factor that enables the uniform stacking of hundreds of cells. For these reasons, micrometer-level precision is required for the positioning and height of CELLSEAL.
Micrometer-level precision may be hard to grasp. Thinking in a different scale, however, illustrates its difficulty. In a fuel cell vehicle, for example, hundreds of cells are stacked together, resulting in a total gasket length of about 1 km per vehicle. For commercial vehicles, which are designed for long-distance travel, two stacks may be installed, bringing the total gasket length to around 2 km. Despite this, the gasket itself is only about 0.8 mm in height. To put this into perspective, consider it as a continuous line, such as a railway track. For example, if we imagine connecting Tokyo and Nagoya (a straight-line distance of 275 km) with railway tracks, the acceptable margin of error in the position of the tracks would be less than 5 cm. This is the level of precision required for the gasket (Figure 3).
Please enlarge the screen to view
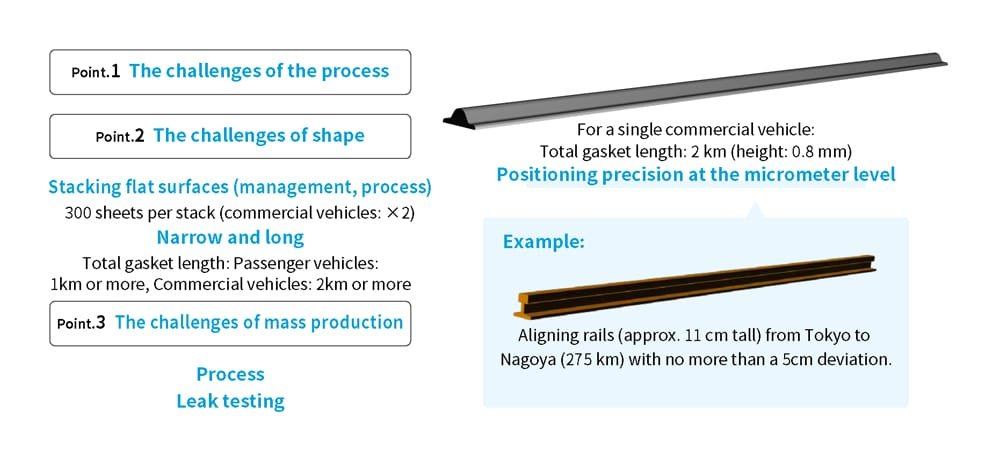
Another major factor influencing the quality of gaskets is how to address hydrogen gas permeation leakage. Gas leakage occurs in two forms: interfacial leakage, which escapes through gaps between the cell seal and the separator; and permeation leakage, which occurs when gas passes through the CELLSEAL. Permeation leakage occurs when gas molecules slip through the spaces between the molecules of the material serving as a membrane. This is the same phenomenon that occurs when a balloon gradually deflates over time, even when untouched.
For this reason, permeation leakage cannot be entirely prevented. The rubber used as the base material for CELLSEAL has a structure in which molecular chains are tangled rather than arranged in an orderly manner. This creates many gaps between the molecules, making it particularly easy for small molecules like hydrogen to pass through (Figure 4). Countermeasures involve understanding the extent of permeation leakage and devising ways to suppress it as much as possible through material selection and cross-sectional design improvements. Developing CELLSEAL when faced with such challenges is no easy task.
In the second part of this article, we will explore how NOK tackled these issues.
Please enlarge the screen to view
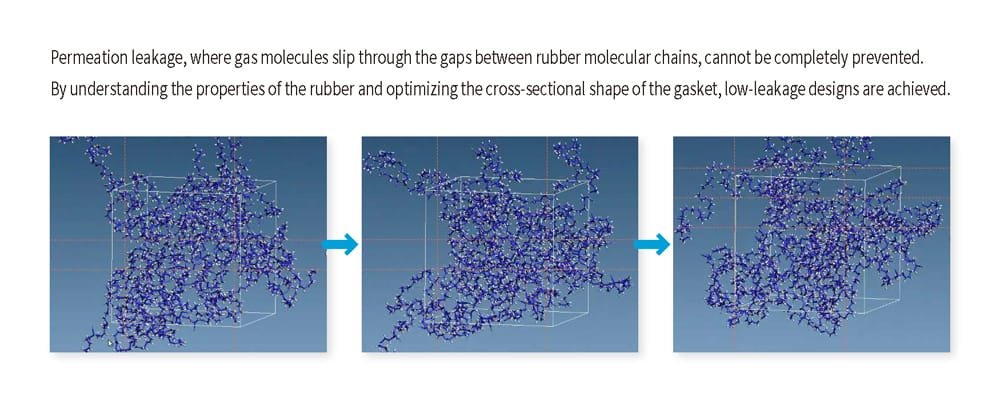