ストレッチャブルFPC(前編)見た目はまるで湿布薬、美顔器電極シートに採用された伸縮性「基板」はこうして生まれた
電子機器の主要な構成部品の一つである電子回路基板。基板と聞くと、多くの場合は文字通り硬い板の上にたくさんのICチップが配置されたものをイメージするかもしれない。ただ、カメラやスマートフォン、タブレットといった小型・薄型の機器などを中心に、柔軟性があり、繰り返し変形させることも可能なフレキシブルプリント基板(FPC)が使われている。NOKグループには、FPCを進化させ、新たな用途を開拓したプレーヤーがいる。メクテックだ。
メクテックが開発したのは、極薄で、伸縮性を持たせた「ストレッチャブルFPC」である。まるで湿布薬シートのように薄く柔らかい。その柔軟性・伸縮性を生かし、身体に貼り付けて脳波などを測定する医療機器に採用されている。最近では美容機器の一部として、やはり身体に貼る電極シートとして活用されるようになった。
これほどの柔軟性・伸縮性を実現した基礎技術が、電子回路を基板に「印刷」するプリンテッドエレクトロニクス(PE)技術である。PE、ストレッチャブルFPCがこうして日の目を見るまでの道のりは、決して平坦ではなかった。PEを生かした製品開発プロジェクトは二度にわたって開発中止に追い込まれた。それでも、そこからの気づきを生かし、目指す製品形態を少しずつ変えて研究開発を続けてきた。その粘り強い「継続」の力と、「社会のニーズを捉える」という発想の転換により、たどり着いたのが、今のストレッチャブルFPCである。もともとはFPCの製造コストを下げることを目指してPEに挑んだメクテックが、医療機器用や美顔器用の電極シートの製品化に至るまでのストーリーを紹介しよう。
「PEならFPCの製造工程をこんなに効率化できるじゃないか」
FPCの歴史は意外に古く、もともとは1960年代に宇宙開発・航空・軍事などの用途に使われたのが始まりだといわれている。その後、1970年代になると、小型化を要求される光学一眼レフカメラや薄型電卓など一般用途にも転用され急速に普及する。日本メクトロン(現メクテック)も、1969年にFPCを製造するメーカーとして設立され、1986年以降は台湾やアメリカ、タイ、香港、シンガポール、中国、ベトナム、欧州など、海外での生産拠点及び販売拠点を拡充させてきた。
電子機器製造の分野では、2000年頃から電子デバイスや素子の全てを印刷技術で作るPEが世界的に注目されるようになり、メクテックでも2008年に新たに創設された商品企画室で事業化の検討を始めた。PEに注目したのは、従来のフォトリソ・エッチング方式で11ステップのプロセスが必要だったFPCの前工程(パターン形成)を、3ステップで済ませられるから。それだけ作業を効率化でき、大幅な製造コスト抑制効果があると見込んだわけだ(図1)。
画面を拡大してご覧下さい。
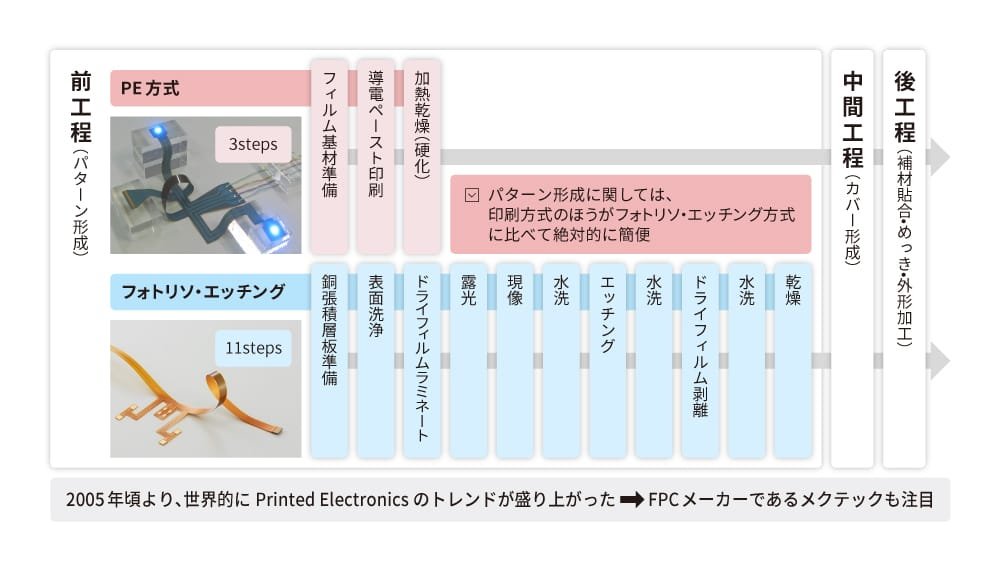
ほかにもPEによるFPC製造には、工程に溶液を使わないドライプロセスであるため環境に優しく、多品種・小ロットでの生産を安価にできるメリットも見込める。そんな理想像を描いたメクテックは、実際に社内にFPCの前工程を印刷できるラインを作るだけでなく、印刷性能を有する銀ペーストを新たに開発し、印刷した銀パターンの上にめっき付けして、FPCにハンダのリフローで電子部品を実装できるようにした。
ただ、開発を進めてみると、想定とは違っている実態が徐々に明らかになっていった。例えばPEでFPCを製造し、展示会に出品するなどして市場性をリサーチしたが、やはり印刷物になると性能的に無理が出てくる。特に、PEの場合はフォトリソ・エッチングほど微細な配線ができないので、対応できる製品が制限される。高温時の絶縁特性など信頼性の観点でも、フォトリソ・エッチングで作ったFPCに比べて実用性に劣る。
コスト抑制効果も、実は思った通りには得られなかった。PEによって前工程を簡便にできるものの、製造コスト全体では、中間工程と後工程のコストが占める割合が大きく、そのコストは従来通りであるため、効果が薄いことが分かった。前工程についても、フォトリソ・エッチングでも低コストで大量にFPCを作れるメクテックにとっては、逆にPEのコストのほうが高くなってしまう。加えて、当時はまだ環境問題に関して今ほど敏感ではなかったため、低環境負荷であるという長所も顧客への訴求力に乏しかった。
全工程を含めたFPCの製造コストに関する気づきについて、当時商品企画室でPEの研究に関わった技術本部 開発部 開発二課 課長の岩瀬雅之氏は、「当時、こういう気づきが得られたのは、弊社だけだったかもしれない」と振り返る。その理由として、岩瀬氏は「当時はメクテックのように、PEの導入を検討していたメーカーの中でも、後工程まで含めた基板の製造に関わっていたメーカーは少なかった」と説明する。「PEで基板を作ろうとしているメーカーはスタートアップが多く、彼らは前工程にしか着眼していなかったのです」(岩瀬氏)。
こうして、PEによるFPC製造という新たな挑戦は、結果的に「PEでなくてはならない」という理由を見つけられず、2011年中に中断することになった。その時の心境を、岩瀬氏は「欧州を起点に立ち上がったPEは、当初は業界全体で期待が高まったが、そのトレンドも2011年くらいになるとトーンダウンしてきた。すでにFPCを低コストで大量に作れる強みを持つ弊社では、これ以上取り組みを続けていてもメリットがないといった考え方になり、研究に関わった商品企画室員もかなりモチベーションが下がっていた」と振り返る。
タッチパネルの需要増に対応する透明FPCにPEを適用
PEに関しては、実はこれとは別に、2010年頃から並行して別の研究が進められていた。当時急激に需要が高まってきたタッチパネル用の透明FPCの量産化である。スマートフォンやタブレットの台頭が背景にある。当然、ディスプレイメーカーもタッチパネルの量産を進めていたが、液晶ディスプレイや有機ELディスプレイなどの透明電極として使われていたITO材料枯渇への懸念があった。曲げたり巻いたりできるという高付加価値化を狙ったフレキシブルなタッチパネルのニーズも見えてきた。
そこで、メクテックとしては岩瀬氏が属する同じ商品企画室において、導電性を持ちながら可視光を透過する性質を持つ、ITO代替材料(PEDOT/PSS、AgNW)によるフレキシブルタッチパネル(透明FPC)の研究を2010年から並行して進めていた。
当時のITO代替材料はPEDOT/PSSやAgNWを含有する塗材がフィルムの片面にコーティングされたものが主流だった。このため、これらの素材を使ってフレキシブルタッチパネルを作るには、図2に示すようにX軸方向とY軸方向に並んだ電極パターン(紫色の部分)を別個のパネルとして作成し、後工程で貼り合わせることになる。こうした電極を高透明フィルム状に形成するためには、エッチングレジストパターンを形成した後に専用の薬液を使ってエッチングする必要がある。
画面を拡大してご覧下さい。
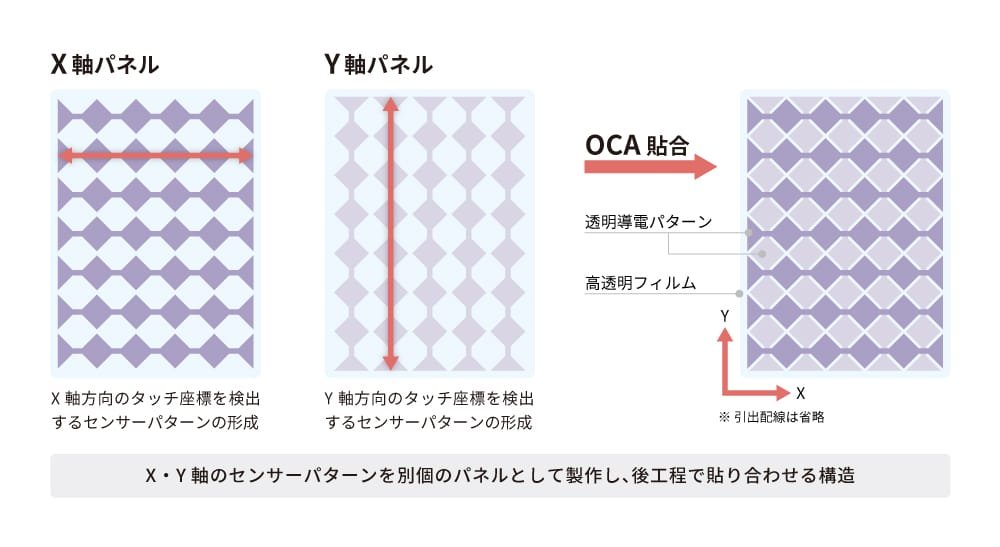
ところが、当時のPEDOT/PSSは薬液耐性が低くデリケートな材料だったために、従来のフォトリソ・エッチング工程のような多重の薬液プロセスには耐えられず、性能が劣化してしまうという問題があった。そのような制約の中でメクテックは、エッチング工程こそ薬液を使うものの、前段階ではスクリーン印刷を使う(薬液を使わない)ドライプロセスを適用することで、性能劣化を最小限にとどめるようにした(図3)。
画面を拡大してご覧下さい。
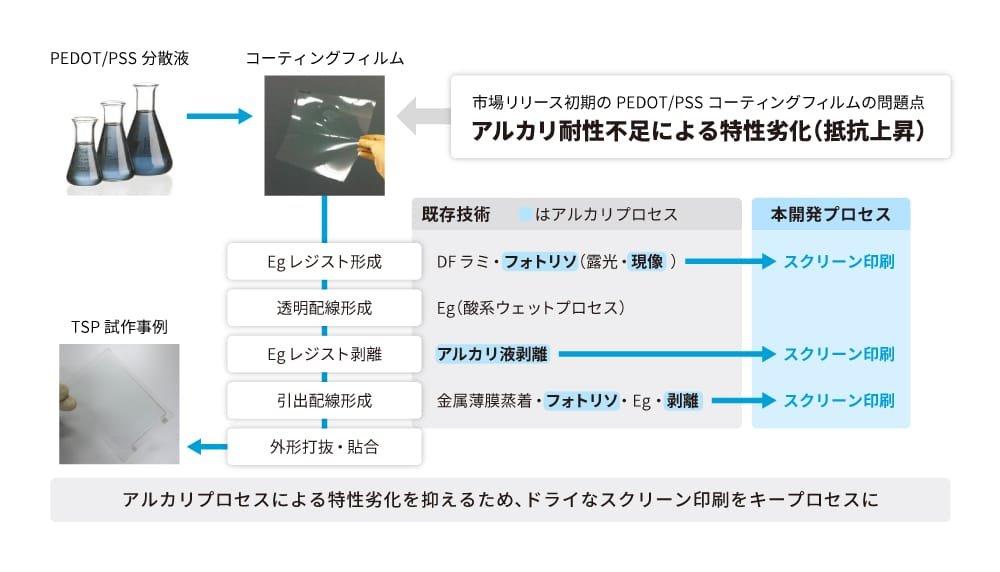
しかし、PEDOT/PSSをスクリーン印刷で適正に使用するには、増粘剤などの添加物を含有させる必要があり、それによって導電性が低下する。かといって、透明基板の配線抵抗を下げるために厚膜化すると、今度はPEDOT/PSSが持つ青色の特性が強くなり、透明性が落ちてしまう。こうして試行錯誤を繰り返し、なんとか要件を満たす製品を目指している中、iPhoneなどで高透明なタッチパネルが使われるようになったなどの背景もあって顧客側が開発を断念。必然的に、サプライヤーであるメクテックの開発プロジェクトも終了を余儀なくされた。
印刷用銀ペーストとエラストマーシートの出合いで生まれたストレッチャブル
PE活用を起点とした2つのプロジェクトが中断という結果に終わった。だが、メクテックの挑戦はここで途絶えたわけではない。PEによるFPC製造など新規トレンドのキャッチアップと商品企画に取り組んできた商品企画室は、2014年頃からは実際の商品を作る商品開発課となり、よりPEの事業化に集中することになる。そして次にPEの事業化のターゲットとなったのが、全方向に伸縮するストレッチャブルFPCである。
伸縮するFPCに関してメクテックでは、2010年頃からすでに製品化していた。ただし、当初は銅を波形形状にパターンニングして、ウレタンシートで挟む構造だったため一方向にしか伸ばせず、伸縮性も110%と小さいことが課題になり、あまり拡販にはつながっていなかった。
新しい展開は、材料メーカーが新たに開発した印刷で伸びる銀ペーストを採用し、エラストマーのシートの上にパターンニングしていくと、全方向にゴムのように伸びる基板ができるという気づきがきっかけとなった。
この銀ペーストも、当初から伸縮性が分かっていたわけではない。メクテックでは、もともと3D成形用のフィルム上に印刷できる銀ペーストを、柔らかいシートにパターンニングすればゴムのように伸びる配線ができるのではないかと考えていた(図4)。「そのタイミングで、FPC用部材を供給しているサプライヤーが、薄くて伸びやすく、かつ水蒸気や空気をよく通すエラストマーシートを持ってきたことが、PEで伸縮するFPCを作ろうというきっかけになりました」(岩瀬氏)。
画面を拡大してご覧下さい。
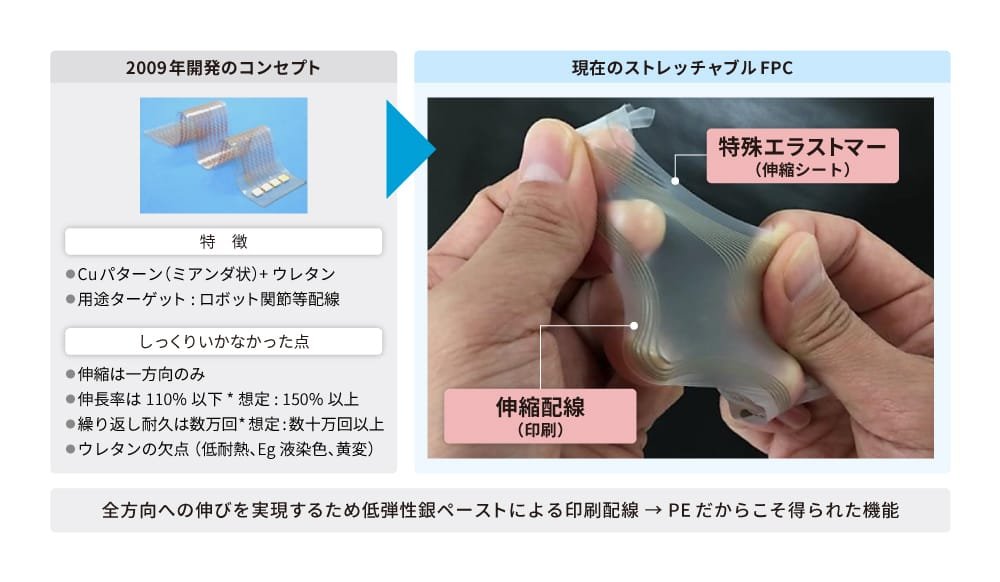
ストレッチャブルFPC事業化の取り組みは、透明FPCの開発が中断された2015年中頃に始まった。当初の銀ペーストでは、フレーク状の銀粉が連続印刷で目詰まりすることが分かったため、メクテックでは銀ペーストの提供元である材料メーカーとタイアップして、独自に細かい粒状の銀粉材料を開発した(図5)。これは、長年、スクリーン印刷技術を磨いてきたメクテックだからこそ見いだせた課題と対策である。
画面を拡大してご覧下さい。
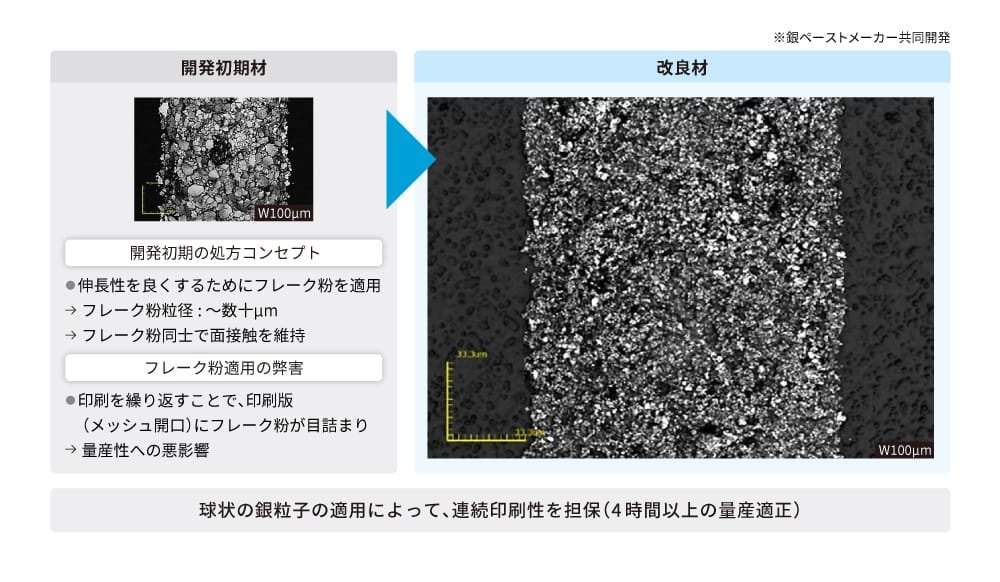
新製品の開発は社会ニーズのキャッチアップから
一方、メクテックはここまでの取り組みで、商品開発の大きな教訓を得ていた。直接顧客のニーズに対応して商品を開発する場合、商品化できるかどうか分からない状態から取り組みを進めなければならない。先方から製品の採用をやめると言われると、手がかりがないままに他の用途を探さざるを得ず、ニーズを見つけられなければ、結局、プロジェクトは中断に追い込まれる。
岩瀬氏は、「ここが大きな転換期でした。二度のプロジェクト中断によって、新技術・新製品の開発は、根底にある社会ニーズに対応したものであるべきだと改めて気付くことができた」と振り返る。こうして新たに立ち上がったPEの開発テーマ「ストレッチャブルFPC」においては、顧客のニーズ主体から、社会ニーズを汲んだ商品開発へと舵を切った(図6)。
画面を拡大してご覧下さい。
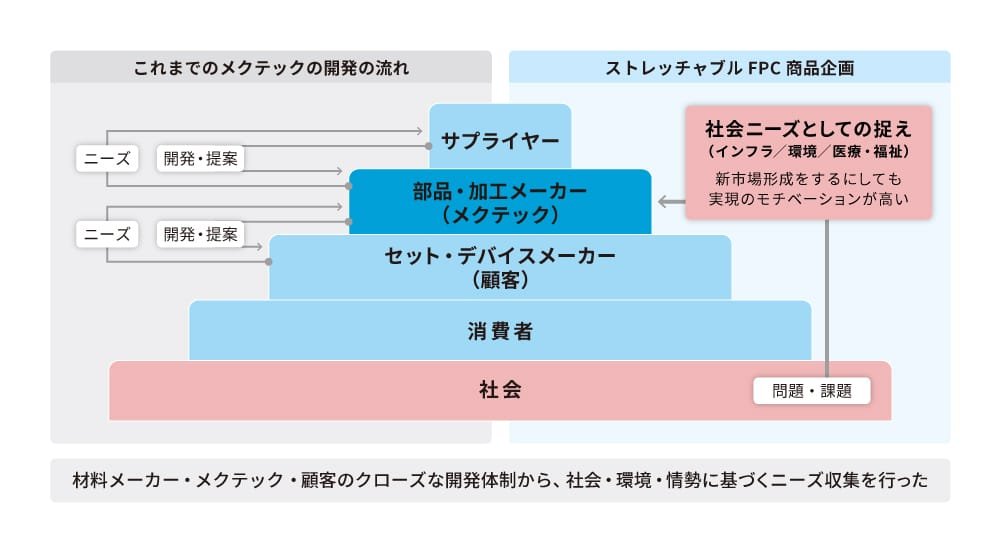
2014年には、ウエアラブルエレクトロニクスのトレンドが沸き上がり、一方で介護・医療費削減のために生体センシングの技術分野が活性化し始めていた。そうした社会ニーズに対して、メクテックは柔軟性に加えて伸縮性を持つことで、生体に不快感なく貼り付けられるFPCが医療分野などで必要とされると考え、パートナー探しを始めた。
後編では、社会ニーズを捉えることで医療用の生体電極シートの量産化に漕ぎ着け、さらには新たに美容分野にも市場を広げたメクテックのストレッチャブルFPCについて、量産化の経緯や商品化にあたっての課題、将来展望などについて紹介する。