微細なものづくり技術が社会の支えに――燃料電池開発への挑戦(後編)
NOKとして新分野への挑戦となった、燃料電池向けガスケット「セルシール」の開発。要件と実現可能な実装のはざまで、要件の分析、原理やメカニズムの解明、要件にあるスペック調整のための顧客との交渉を重ね、量産体制に至るまでに4年の歳月を費やした。マイクロメートルオーダーでの精度確保や分子レベルのガス漏れ防止という難題に、FC Solution量産開発部・先行開発部のエンジニアたちはどのように挑んでいったのか。
要件を原理から読み解き、4年をかけて実装可能なスペックに調整
セルシールの設計にあたっては、まず設計する部品の目的や機能、性能要件を明確にする必要があった(図1)。そのため、顧客と綿密なコミュニケーションを取り、仕様や制約条件を把握して内容を協議調整しなければならない。FC Solution量産開発部で製品設計を担当する島添稔大氏によると、今回NOKが受注したセルシールについては、顧客から提示された50ページ以上の資料に性能・機能の明確な仕様がまとめられていた。加えて「開発の途中段階でも項目が追加されていった」。
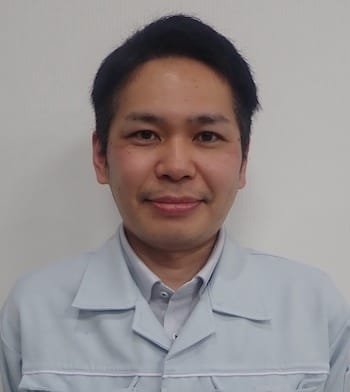
画面を拡大してご覧下さい。
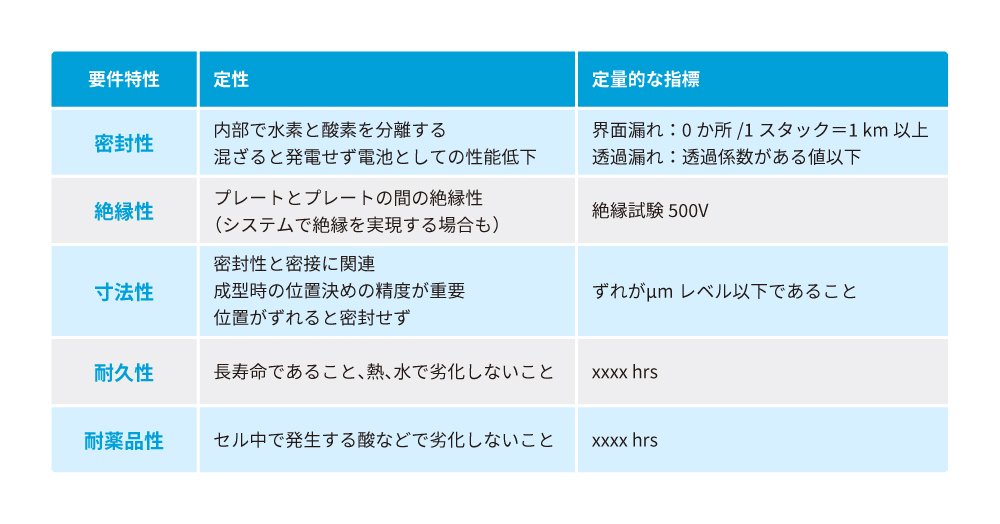
ただ要求仕様の中には、発注者側が机上計算に基づいて決めるスペックも多く含まれていて、実装という観点から必ずしも現実的とはいえないことがある。そのまま要件を満たそうとすると実装のハードルが極めて高くなる、といったことだ。そこで、燃料電池の性能や耐久性といった観点からの要件と、実現可能な実装方法を両立できる「スペックの限界」を探さなければならない。この作業が一番難しい。要求された仕様を見ても、実際に設計を進めてみないと分からないことは少なくない。仕様に合わせても、それによって要求される性能・機能を達成できるかどうか、検証する作業は不可欠である。「もらった仕様書を読み込んで、仕様一つひとつの内容を検証した」(島添氏)。その作業の中で、この水準までは難しいが、ここまでだったらできる、という具合に代替案を検討。「それぞれについて、代替案を提示する交渉を重ねていった」(島添氏)。
この交渉作業の難しさは、検証結果を伝えても、必ずしも相手が納得してくれないことにある。その結果に基づく原理やメカニズムといったところまではっきりさせなければ、スペックの緩和までは認めてもらえない。必然、仕様の検証、原理やメカニズムの解明、代替案の考案とそのエビデンス収集に明け暮れることになった。「何回か試作のステージがあって、検証を繰り返し、要件を満たさないところは新しく仕様に反映させていった」(島添氏)。最終的に、量産する前段階の設計完成に至るまでには、仕様を受け取ってから3~4年かかったという。
既成概念にとらわれず自由な発想で
設計を乗り切った背景には、開発チーム内で多角的にアイデアを出し合える社風の影響が少なからずある。例えば、最初はセルシールをセパレータに貼り付ける方法として、従来品目で実績のある製法を使うことを考えた。ただ、それでは前編で説明したセルシールの高さ誤差を許容範囲内に収められない。そうなればシール性能も高まらない。そこで、NOKでは経験のない新しい塗布方法に変えることにした。「普通に従来製法を突き詰めていくのでは、どこかで限界が来ることを早い段階で察知したため、塗布方法の変更にかじを切った。製法にこだわらず、自由な概念でアイデアを出し合いながら作り上げていった」(島添氏)。
素材についても、NOKが長年にわたって透過漏れを研究してきた知見が生きた(図2、図3)。「さまざまな素材における透過漏れについて研究、シミュレーションし、きちんと理論的に理解しながらシールを開発してきた。その経験に基づいて採用する材料を選び、その理由をきちんと説明し納得してもらった」(島添氏)。
画面を拡大してご覧下さい。
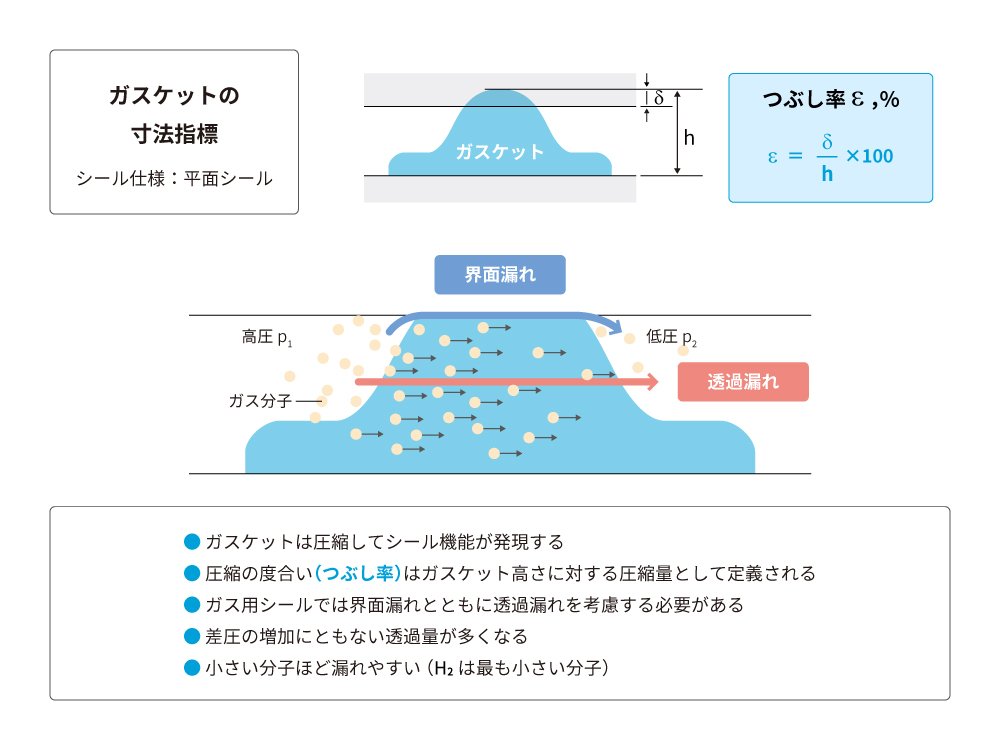
画面を拡大してご覧下さい。
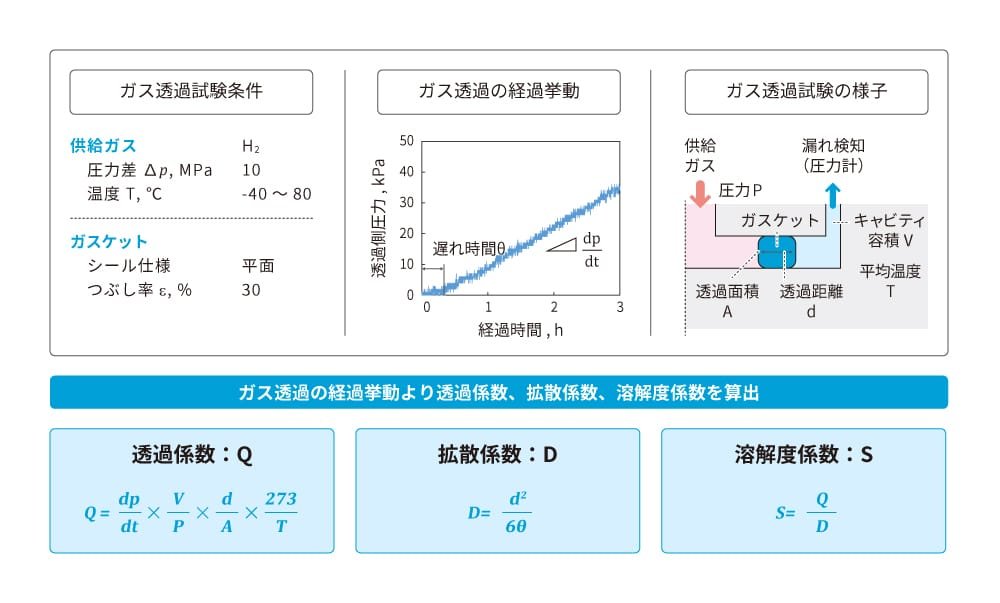
「プレス成形で生じる応力を考慮していないじゃないか」
開発段階では、設計した部品の性能や耐久性を評価するためにシミュレーションを行う。この工程で、部品の応力解析や熱解析、流体解析などを実施し、問題点を特定する。「材料や製造方法を設定し、顧客から指示された温度や圧力などに関する要件を入力できるような解析プログラムを作る。そのプログラムを使って、条件によってその値を変えながらシミュレーションを行っている」(島添氏)。
セルシールについても、もちろん、解析プログラムを作り、シミュレーションを実施した。ところが、これが一筋縄ではいかない。セルシールの開発自体、これまでの経験がなく、それを解析するプログラムそのものも開発段階だったためだ。実際に設計データを反映させてみると、考えた通りに性能要件を満たせないことがあった。原因はパラメーターを見落としていたこと。セルシールを貼り付けるセパレータにはプレス成形するものもあるが、その際金属に圧力を掛けると内部に応力が発生する。その応力の影響をシミュレーションに反映させていなかった。「最初はプレス成形で発生する応力まで考慮できておらず、そのままプログラムを実行すると、圧縮時の面圧が実機通りにならず低く出ていた。それによって、セルシールをセパレータと一体化させた際にシーリング性能の要件を満たせなかった」(NOK R&DのFC Solution先行開発部で工程設計を担当する眞坂武史氏)。
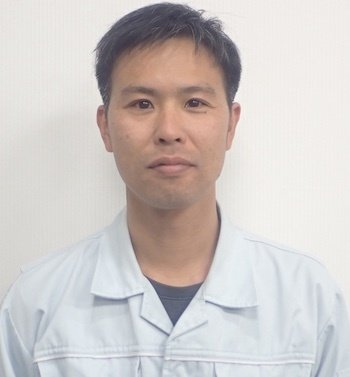
シミュレーションで望んでいる結果が得られなければ、その原因を絞り込んでいく。「セパレータの応力の例では、設計部門だけでは原因が分からない部分が多かったため、プレス成形に詳しいチームに参加を要請し、リアルに起こっていることの洗い出しから始めて、原因を特定していった。いくつもの仮説を立て、それぞれについて答え合わせをしていくイメージだ」(島添氏)。
プロトタイプによる検証で、想定していなかった不具合に遭遇
設計した部品の解析とシミュレーションを終えたら、次は3Dプリンターや加工機械を使用してプロトタイプを作成する作業に入る。ただ、ここでも解析とプロトタイプ作成の工程を何度も往復した。
何度となくプロトタイプを作って検証する中では、詳細設計の段階まで戻らなければならなくなることもあった。例えば、NOKが作ったセルシールのプロトタイプを使って顧客側でセルを組んでみたときのこと。なんと顧客から「全くシーリング性能が発揮されない」との連絡があった。急ぎ、納めたプロトタイプを引き取って確認すると、確かに性能が出ていない。さまざまな角度から検証していくと、「セルシールを組み込んだセルをスタックさせたときの構造に問題があることが見えてきた」(眞坂氏)。
セルのスタックには、どこまでセルシールのゴムを圧縮するのかのコントロールが必要になる。その制御の部分が、初期の設計には含まれていなかったため、実際にセルを積み上げた際に、セルシールが限界まで潰されてしまう設計になっていた。これによってゴムが変形してしまい、設計通りのシーリング性能が発揮できなくなった。本来の設計では、ゴムがバネの役割を担ってセパレータの位置が揃うはずだが、そうなっていなかったことが新たな解析によって分かってきた。
試行錯誤の結果、解決策として挙がったのは、セパレータにこれ以上ゴムが潰れなくなるストッパーを設けること。「セパレータの外枠の部分に少し高さを設け、そこまでしか締め付けられない構造を考えた」(島添氏)。シミュレーションでも、この方法が効果的だという結果を得て、改めてプロトタイプを作成。顧客側で再びセルをスタックしたところ、求めていたシーリング性能が得られたという。
こうして、プロトタイプによるテストと改善を重ね、最終的な設計を確定させた。プロトタイプの試作・検証を経た仕様変更は、数十回に及んだ。「パワートレインやエンジンなどの部品を開発する場合、発注元にもよるが試作は大体2回くらい。次の段階では試作で検証した内容で量産型を起こし、さらにそこであと3巡くらい試作と検証を繰り返したら量産となることが多い」(眞坂氏)。セルシールのように、試作イベントの中で何十回もトラブルが起こるような部品は普通はないという。
「セルシールの設計が定型化されていないことと、それまでの経験値が少なかったこと」。島添氏は、開発が難しかった背景を、こう振り返る。一つひとつの問題に向き合い、試行錯誤を重ねてメカニズムを解き明かし、顧客と一緒に課題解決に当たる。この粘り強い取り組みこそが、ものづくりの開発力を高めていく源泉といえる。