微細なものづくり技術が社会の支えに――燃料電池開発への挑戦(前編)
自動車やバイク、テレビや冷蔵庫をはじめとする家電製品、冷凍食品にまで利用対象が広がっている自動販売機、工場の製造ラインや病院に設置されている医療用機器……。我々の身のまわりには、さまざまな機械が存在している。1台当たり数千~数万点に及ぶ部品から作られている。これらの機械がきちんと動作し続けているのは、直接的には我々の眼には触れないところで重要部品が、その役割をしっかりと果たしているからだ。もちろん、それを生み出しているのは、髪の毛1本の直径よりもはるかに小さなサイズでの高精度な製造、長期にわたって過酷な環境にさらされても性能・機能を損なわない仕組みと品質、そんなものづくりである。
以下では、そうしたもののうち未来の社会の一端を担う「燃料電池」にフォーカスを当て、その仕組みと開発を手掛けたNOKの開発現場における体験談から、ものづくりの“凄み”を紹介しよう。
気体の漏れを抑制するシール技術が水素社会を支える
燃料電池は、水素と酸素を使った化学反応によって電気を生み出す装置。電池とは呼ばれているものの、燃料から電気エネルギーをつくる発電機の一種で、従来の熱機関を使った発電方式より高い発電効率を期待できる。特に注目されている理由が、電気を生み出す際に二酸化炭素や窒素酸化物を排出しないという環境配慮面のメリット。社会全体としてカーボンニュートラルを目指すうえで、カギを握る技術の一つであり、トラックやバスといった長い距離を継続して走らせたい商用車などの用途を中心に、今後採用が進んでいくと見られている。
1941年の創業から、自動車のエンジンやモーターで使うオイルシールの研究開発に取り組んできたNOKでは、これまでのシール技術の開発経験やノウハウを、燃料電池に使われるガスケットにも適用しようとしている。とはいえ燃料電池自体、まだ発展途上の技術であり、製品実装の実績も数少ない。自動車メーカーなど発注元によって、形状や性能・機能の要件はまちまち。NOKが開発するガスケットに求められた要件も、極めて多様かつ高性能・高機能で、材料や形状を含めてゼロからの設計となった。
シーリング用ゴムの実装にはマイクロメートル単位での精度が必要
燃料電池は、酸素が供給される正極(カソード)と水素が供給される負極(アノード)という2つの電極と、イオンが移動する電解質で構成された「セル」が最小単位となっている。自動車用の燃料電池は、このセルを数百枚積層させたスタック構造となっている(図1)。NOKが自動車メーカーに供給するのは、こうしたスタック構造において個々のセルを区切る役割を持つ「カソードセパレータ」(正極側)と「アノードセパレータ」(負極側)に貼り付ける「セルシール」と呼ばれる製品だ。
画面を拡大してご覧下さい。
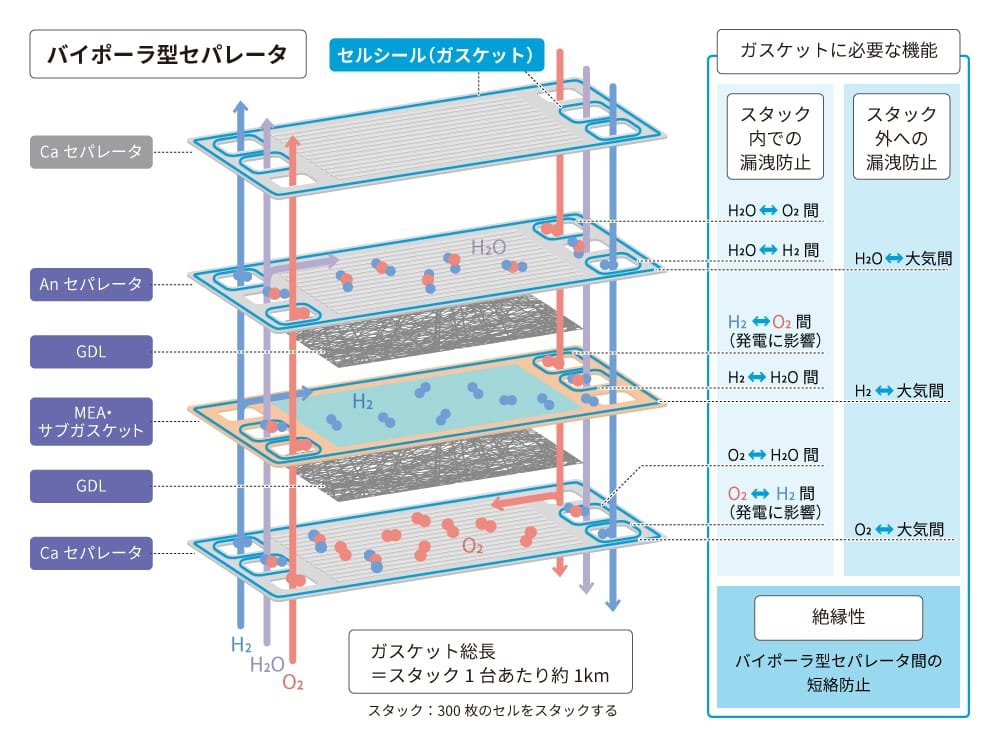
画面を拡大してご覧下さい。
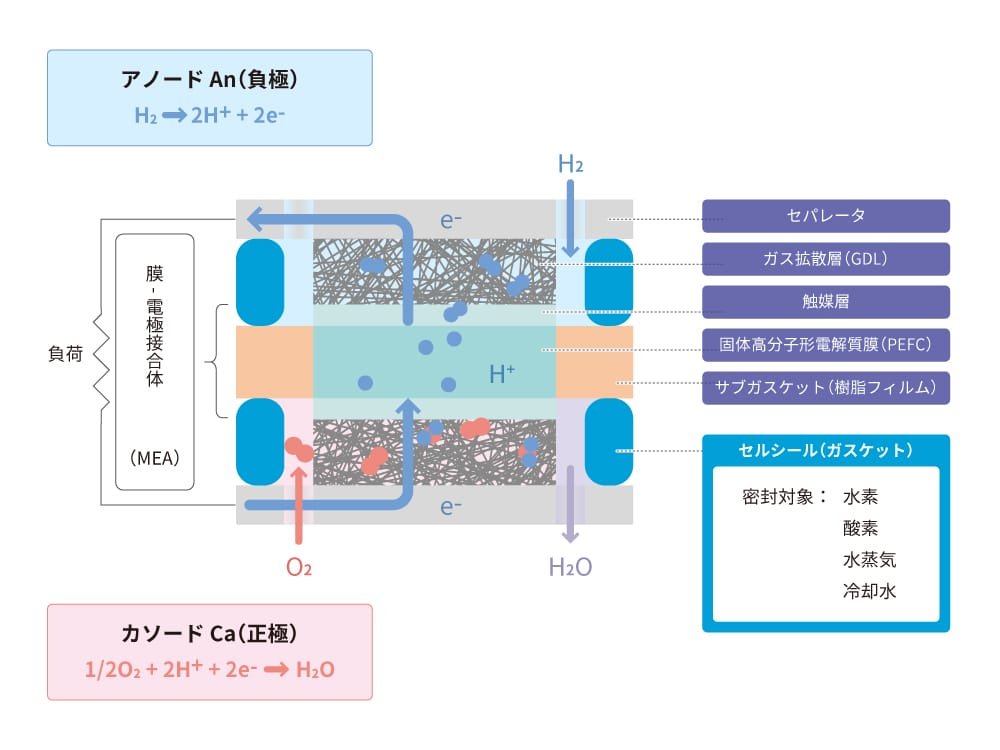
セルシールの役割は、発電の過程でセルから水素や酸素、水蒸気などが漏れないようにすること(図2)。ガスが漏れると、その分、発電効率が低下したり、セルの劣化要因につながったりといった問題が生じる。そこで、それぞれのガスが漏れないよう、伸縮するゴムの性質を生かしてセパレータを隙間なく密着させる。加えて、数百枚ものセルをまっすぐに積み上げるために、均一性も重要なポイントになる。こうしたことから、セルシールの位置・高さにはマイクロメートルオーダーの精度が求められる。
マイクロメートルオーダーの精度と言われてもピンとこないかもしれないが、違う尺度で考えてみるとその難しさがよく分かる。燃料電池車では1台当たりで数百枚のセルがスタックされているので、ガスケットの長さは約1kmになる。商用車の場合は長距離走行するためにスタックが2台積まれることもあり、ガスケットの総長は約2kmにもなってくる。ガスケットの高さは0.8mmくらいしかない。1本のつながった線という観点から、これを電車のレールに置き換えてみると、例えば東京-名古屋間を直線で結んだ距離275kmに対して、敷かれたレールの位置の誤差が5cmも許されない、という次元である(図3)。
画面を拡大してご覧下さい。
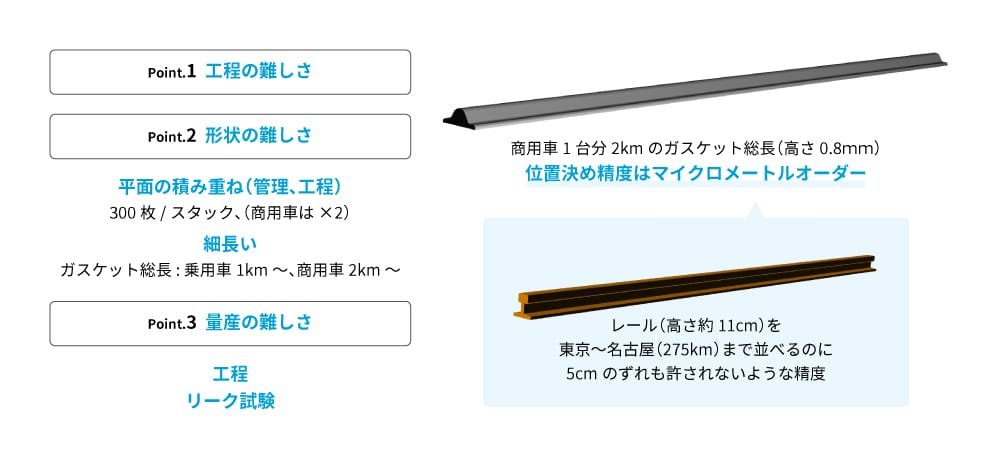
ガスケットとしての品質を左右するもう1つの大きなポイントが、水素ガスの「透過漏れ」への対策である。ガスの漏洩には、セルシールとセパレータの隙間から漏れる界面漏れと、セルシールの中を透過する透過漏れがある。このうち透過漏れは、膜に相当する物質の分子と分子の間をガス分子が通り抜けてしまうことで起こる。ガスを入れた風船が何もしなくても次第にしぼんでしまうのと同じ現象である。このため透過漏れは原理上防げない。セルシールの原材料となるゴムは分子が規則正しく並んでいるのではなく、分子鎖が絡み合った構造をしていて、分子と分子の間の隙間が多く、水素のように小さな分子は特に通り抜けやすい(図4)。対策は、透過漏れの程度を把握することと、透過漏れを少しでも抑制できるよう素材、断面形状などを工夫することである。
こういった難しさがあるセルシールの開発。後編では、NOKがどのように取り組んだのか、見てみよう。
画面を拡大してご覧下さい。
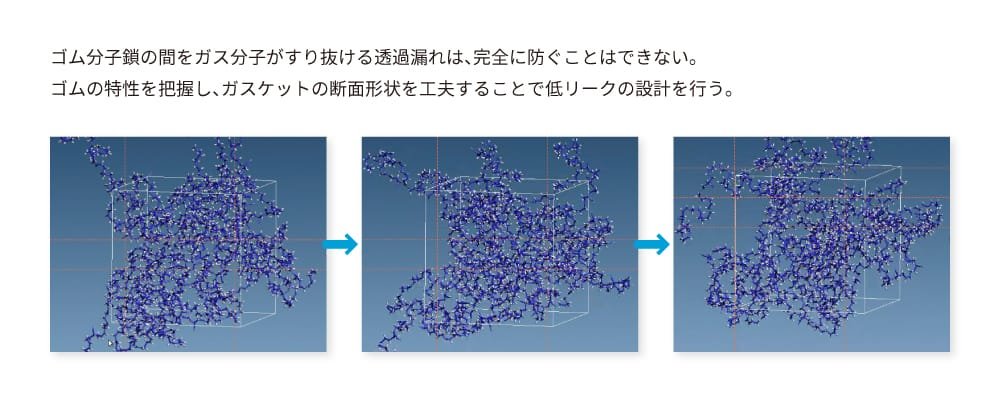